Table of Contents
Introduction
In the intricate world of material processing, the multi wire cutting machine emerges as a technological marvel, bridging the gap between precision and efficiency. This article delves deep into the realm of multi wire cutting machines, exploring their types, applications, and the innovative cutting wires they employ.
Section 1: The Fundamentals of Multi Wire Cutting Machines
Understanding the Technology
Multi wire cutting machines represent a significant leap in cutting technology, utilizing multiple wires simultaneously to cut through various materials. These machines can be broadly categorized based on their primary use: in semiconductor manufacturing and in stone processing.
Design and Mechanics
- Semiconductor Industry: These machines use ultra-thin diamond wires, around 0.027 mm in diameter, for slicing semiconductor wafers with utmost precision.
- Stone Processing: In contrast, stone cutting machines use thicker diamond wires, ranging from 0.5mm to over 1mm, designed to slice through hard stone materials like granite and marble.
Section 2: Multi Wire Cutting Machines in Semiconductor Manufacturing
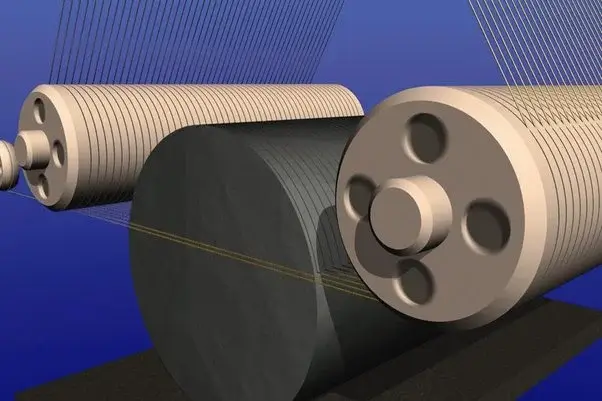
A Multi Wire Cutting Machine is an advanced industrial device designed for slicing various materials, notably stone and semiconductor wafers, using multiple wires simultaneously. This machine is especially prominent in industries where high-volume, precision cutting of materials is required. Here’s an overview of its features, operation, and applications:
Features and Operation:
- Multiple Wire System: The defining characteristic of a Multi Wire Cutting Machine is its use of several parallel wires, each impregnated with abrasive particles like diamonds. This multi-wire setup allows the machine to perform multiple cuts in a single pass, significantly increasing productivity.
- Precision Cutting: These machines are designed to achieve high precision and consistency in cutting. The wires can be finely adjusted to achieve the desired thickness of slices.
- High Efficiency: By using multiple wires, these machines can process large blocks of material or several smaller blocks simultaneously, making them highly efficient for large-scale production.
- Control and Customization: Modern Multi Wire Cutting Machines often come with advanced control systems, allowing for precise adjustments in speed, tension, and wire spacing. This level of control enables customization of the cutting process according to specific material and size requirements.
Applications:
- Stone Processing: In the stone industry, Multi Wire Cutting Machines are used for slicing large blocks of natural stone, such as granite and marble, into slabs or tiles. This method is much more efficient than traditional single-blade cutting, allowing for quicker production of stone slabs with uniform thickness.
- Semiconductor Manufacturing: In the semiconductor industry, these machines are used for slicing silicon ingots into thin wafers. The ability to cut multiple wafers at once is crucial for meeting the high-volume demands of semiconductor production.
- Other Materials: Multi Wire Cutting Machines can also be adapted for cutting other materials that require precision and volume, such as sapphire, glass, and certain advanced ceramics.
The Diamond Wire Saw(cutting wire) in Semiconductor Processing:
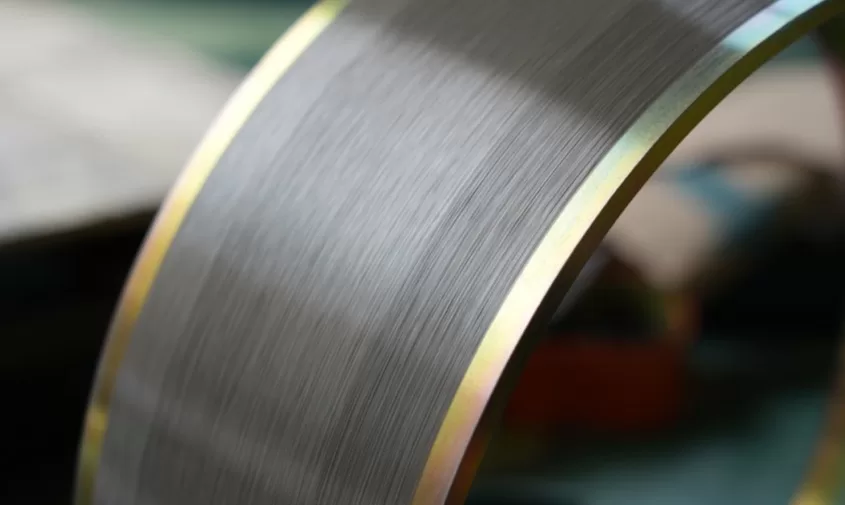
the cutting wire used in Multi Wire Cutting Machines, is an ultra-thin diamond wire, typically around 0.027 mm in diameter. This specialized wire is designed for precision cutting tasks and has specific characteristics and applications:
Characteristics of Ultra-Thin Diamond Wire:
- Diamond Impregnation: The wire is embedded with fine diamond particles. Diamonds, being the hardest natural substance, enable the wire to cut through hard materials efficiently.
- Thin Diameter: At approximately 0.027 mm, the wire is extremely thin, allowing for very precise cuts and minimal material wastage. This thin diameter is crucial for applications requiring high precision and minimal kerf (the width of the cut).
- High Tensile Strength: Despite its thinness, the wire possesses high tensile strength, which is necessary to withstand the stress of cutting hard materials without breaking.
- Smooth Cutting Surface: The use of such fine wire results in a smoother cut surface, reducing the need for additional finishing processes.
Section 3: Multi Wire Cutting Machines in Stone Processing

- Design and Operation:
- These saws are designed to handle large, heavy blocks of stone.
- They typically consist of a series of parallel wires mounted on a frame, which can simultaneously cut multiple slabs from a single stone block.
- The wires are guided over pulleys and tensioned appropriately to ensure efficient cutting.
- Heavy-Duty Construction:
- Due to the demanding nature of cutting stone, these saws are robustly constructed.
- They are equipped to handle the significant abrasion and resistance encountered when slicing through dense materials like granite.
Applications in Stone Industry
- Quarrying: They are extensively used in quarries for extracting natural stone blocks.
- Architectural and Decorative Stone: The machines are crucial in the production of stone for construction and decorative purposes.
The Diamond Cutting Wire Used in Stone Processing:
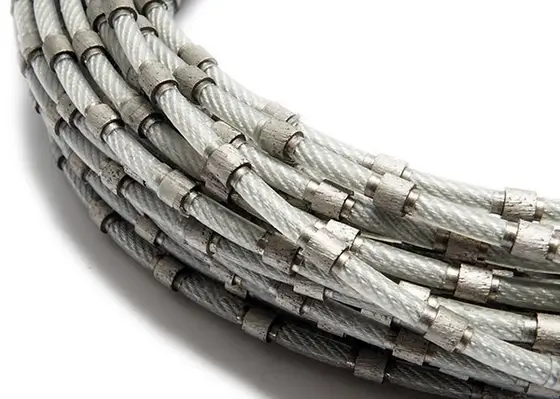
- Thicker Diameter:
- The diamond wire used in stone processing is thicker than that used in semiconductor slicing, usually ranging from 0.5mm to 1mm or more in diameter. This increased thickness is necessary for the greater durability and strength required to cut through large stone blocks.
- Diamond Impregnation:
- The wire is impregnated with industrial-grade diamonds, which are larger and more rugged compared to those used for semiconductor wire saws. This is to ensure effective cutting through hard stone materials.
- Beaded or Sintered Wire:
- Often, the wire is designed with diamond-impregnated ‘beads’ spaced along its length, separated by springs or rubber. These beads act as the cutting segments.
- In some designs, the diamond grit is sintered directly onto the wire, providing a continuous cutting surface.
Section 4: Comparing the Two Types of Multi Wire Cutting Machines
Precision vs. Volume
- Semiconductor Saws: Focus on ultra-precision for delicate, high-value materials.
- Stone Cutting Saws: Prioritize volume and robustness for large-scale material processing.
Wire Specifications
- Semiconductor Wires: Ultra-thin for minimal material loss.
- Stone Processing Wires: Thicker and more durable for cutting through hard materials.
Section 5: Technological Innovations in Multi Wire Cutting Machines
In recent years, there has been a notable shift in the approach to stone processing in China, marked by an innovative integration of technologies originally developed for the semiconductor industry. Companies have begun adapting the machine structure of multi-diamond wire saws, a mainstay in semiconductor manufacturing, for use in the stone industry. This technological cross-pollination is not just a mere transfer of equipment; it represents a significant leap in the way stone is processed.

The use of such advanced cutting technology also means that stone can be processed at a faster rate without sacrificing quality.
Furthermore, using diamond wire with 0.5 mm diameter opens up new possibilities in terms of design and the types of stone products that can be created. Intricate patterns and fine details, which were once challenging or even impossible to achieve with traditional stone cutting methods, are now within reach.
This trend also reflects a broader movement towards sustainable practices in the industry. By reducing waste, manufacturers are not only cutting costs but also minimizing their environmental footprint. The efficient use of resources is increasingly important in modern manufacturing, and the stone industry’s adoption of semiconductor technologies is a prime example of this shift.
Conclusion
The multi wire cutting machine, in its various forms, has become an indispensable component in modern manufacturing and material processing. Whether it’s the precision required in semiconductor fabrication or the robustness needed in stone quarrying, these machines exemplify innovation and efficiency. As we advance, the multi wire cutting machine is set to play an even more pivotal role, pushing the boundaries of what’s possible in material cutting.