Keywords: Composite materials, Advanced materials, Closed diamond wire cutting, Material cutting, Material processing, Manufacturing innovation, Cutting technology.
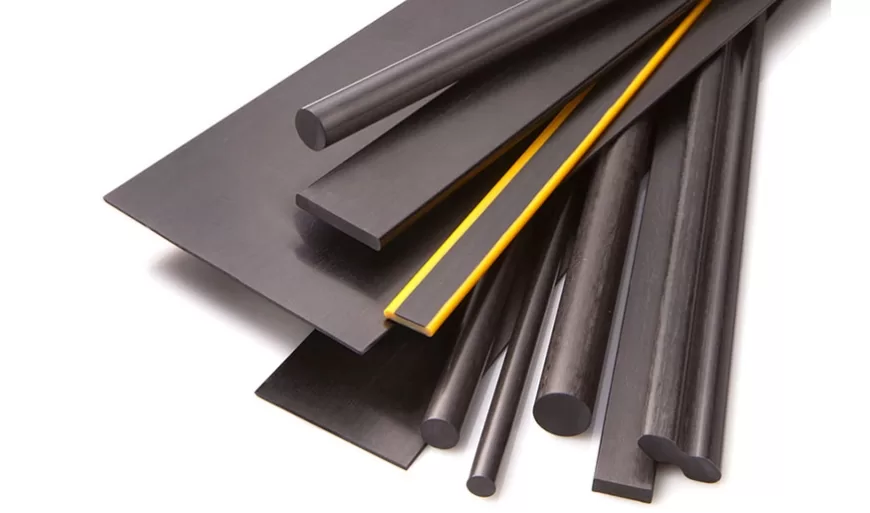
Table of Contents
The Crucial Role of Advanced Materials in Manufacturing
Advanced materials such as composite materials and high-performance alloys have always played a pivotal role in modern engineering. These materials are highly esteemed for their exceptional performance characteristics, but they pose unique challenges in their manufacturing and processing. Traditional machining methods often struggle to meet the demands for high precision, efficiency, and material preservation, driving the need for innovative machining techniques.
Limitations of Conventional Cutting Methods
Conventional material cutting methods such as mechanical cutting and grinding have a long history in material processing. However, they exhibit significant limitations when it comes to addressing the challenges posed by advanced materials:
- Lack of Precision: Traditional methods often fall short of providing the required high precision, resulting in irregular material cut edges and surfaces.
- Material Waste: The use of traditional tools often leads to substantial material wastage, which becomes particularly pronounced when working with expensive high-performance materials.
- Inefficiency: Traditional methods are characterized by lower efficiency and slower production speeds, leading to extended manufacturing lead times and increased costs.
The Revolution of Closed Diamond Wire Cutting Technology
Fortunately, modern technological advancements have brought forth a revolutionary cutting technique known as closed diamond wire cutting technology. Here are the key advantages this technology brings to material processing:
- Precise Material Cutting: Closed diamond wire cutting technology delivers precise cuts in advanced materials, thanks to its outstanding accuracy and stability, ensuring the production of high-precision components.
- Material Conservation: The innovative closed diamond wire cutting machines utilize thin wire profiles, minimizing material wastage. This is crucial when dealing with expensive high-performance materials as it reduces manufacturing costs.
- Enhanced Efficiency: Closed diamond wire cutting machines significantly boost production speeds with high-speed cutting and improved efficiency, reducing manufacturing lead times and costs.
- Smooth Material Surfaces: The cutting process generates exceptionally smooth surfaces, reducing the need for extensive post-processing.
- Complex Geometries: Aerospace components often require intricate and complex shapes. Innovative closed diamond wire cutting excels in producing these shapes with unmatched precision, eliminating the need for time-consuming manual adjustments.
- Diverse Applications: Innovative closed diamond wire cutting is not limited to graphite; it can be applied to a range of high-performance materials, further expanding its utility in aerospace manufacturing.
- Cost Efficiency: Efficient material usage and reduced machining times translate into significant cost savings for aerospace manufacturers.
- Consistency: The technology’s precision ensures consistent quality
Applications of Closed Diamond Wire Cutting Technology in Material Processing
Closed diamond wire cutting technology finds a wide range of applications, not limited to advanced materials alone but also extending to metals, graphite, ceramics, and more. Here are some key application areas:
- Aerospace Industry: The aerospace manufacturing sector demands high-performance materials. Closed diamond wire cutting technology provides an ideal solution for manufacturing high-precision components.
- Medical Sector: The production of medical devices and implants requires highly precise components, precisely what this technology excels in.
- Electronics Industry: The manufacturing of tiny electronic components necessitates high-precision cutting, a forte of this technology.
Future Outlook and Continuous Innovation
As technology continues to advance, closed diamond wire cutting technology will continue to evolve to meet growing manufacturing demands. Future innovations may include higher cutting speeds, increased precision, and broader material applicability. This will further enhance efficiency and sustainability in manufacturing, enabling us to harness the full potential of high-performance materials.
Conclusion
Closed diamond wire cutting technology has redefined material processing, offering precision and efficiency that traditional methods cannot match. In modern manufacturing, the demand for high-performance materials is ever-increasing, and closed diamond wire cutting technology provides an efficient and sustainable solution for addressing this challenge. As technology continues to evolve, this revolutionary technology will drive innovation and progress in the manufacturing industry, transforming the way we work with advanced materials.
In summary, the integration of innovative closed diamond wire cutting into graphite machining is revolutionizing aerospace manufacturing by offering precision, efficiency, and cost-effectiveness that traditional methods cannot match. As we look ahead, this technology will undoubtedly continue to shape the aerospace industry, driving innovation and progress in the creation of high-performance components for the future of aviation and space exploration.