Keywords: CNC Wire Cutting, Endless Diamond Wire Cutting, Precision Machining, Material Cutting, Manufacturing, Automation, Cutting Speed, Material Compatibility, Precision cutting
Table of Contents
Unlocking Precision:
In the realm of precision machining, CNC Wire Cutting has traditionally referred to EDM (Electrical Discharge Machining) wire cutting. However, a new player has emerged on the scene – Endless Diamond Wire Cutting, a revolutionary advancement within the Computer Numerical Control category. In this article, we’ll delve deep into the world of differentiating CNC Wire Cutting, which now includes Endless Diamond Wire Cutting, highlighting their applications and how they are reshaping the landscape of precision machining.
CNC Wire Cutting: The Symphony of Precision
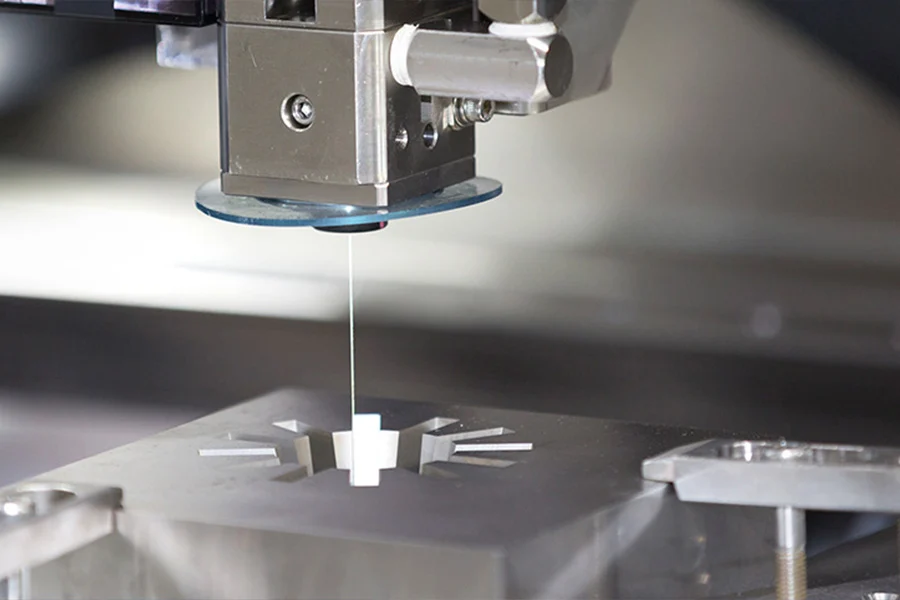
Let’s begin by revisiting the classic CNC Wire Cutting, primarily known for EDM wire cutting. CNC, short for Computer Numerical Control, represents the pinnacle of automation in machining. In traditional CNC Wire Cutting, a charged wire electrode is precisely guided, often by a computer program, to cut through various conductive materials, crafting precision components. The operation of CNC Wire Cutting involves guiding the movement and position of the wire electrode, thus achieving precise cutting, making it a form of CNC machining.
Key Features and Advantages of Traditional CNC Wire Cutting:
- Microscopic Precision: Traditional Computer Numerical Control Wire Cutting achieves levels of precision that were previously challenging with traditional machining methods. It can manufacture intricately detailed parts while reducing material wastage.
- Mastering Complex Geometries: With its computer-guided precision, traditional Computer Numerical Control Wire Cutting conquers complex part geometries that are challenging with conventional machining.
- Reducing Material Stress: Unlike traditional machining, which may introduce thermal stress, traditional CNC Wire Cutting’s non-contact method minimizes material stress, preserving material integrity.
Endless Diamond Wire Cutting: The Efficiency Revolution within CNC Wire Cutting
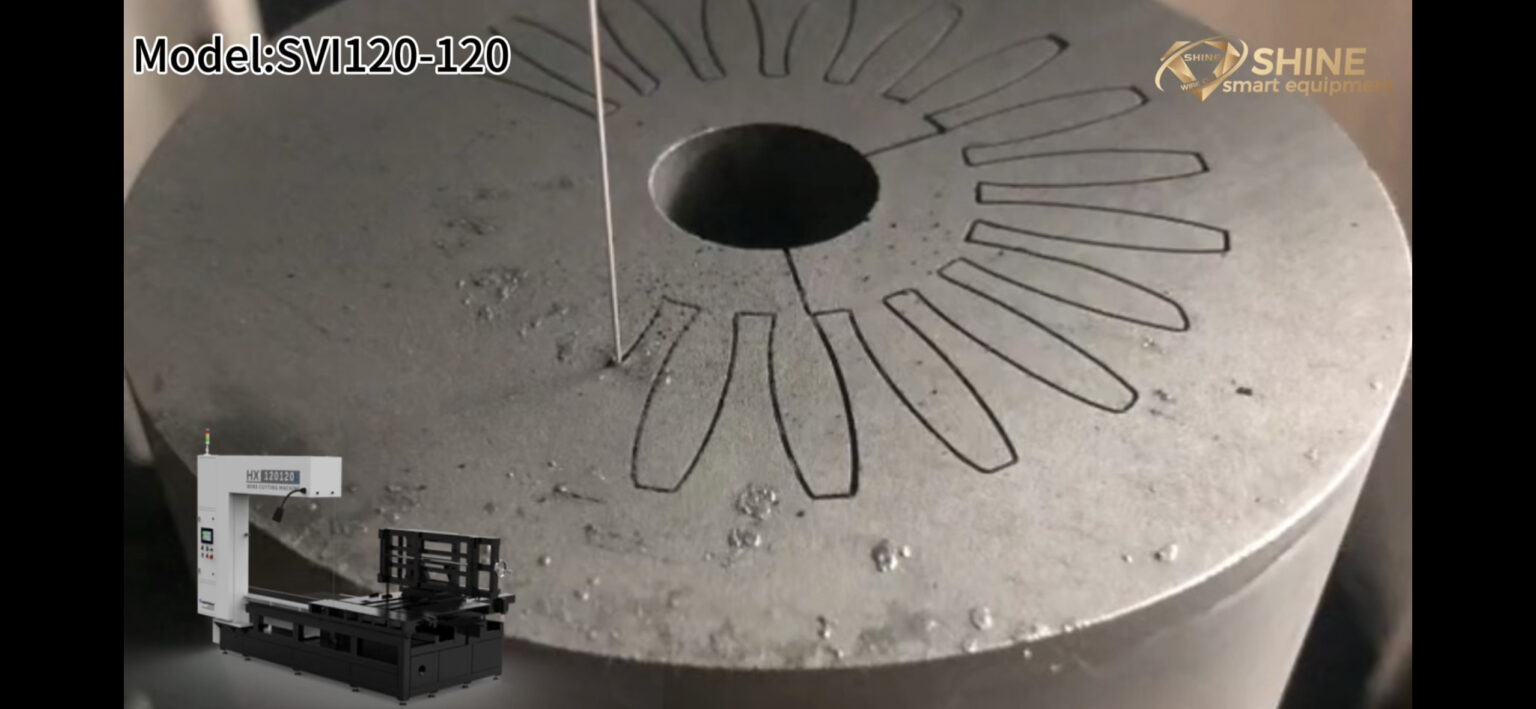
Now, let’s shine a spotlight on Endless Diamond Wire Cutting, a groundbreaking technology that belongs to the Computer Numerical Control Wire Cutting category. This innovative method uses a wire embedded with tiny diamond particles to cut through various materials, both conductive and non-conductive. Its applications span across industries, including semiconductor manufacturing, solar cell production, and optical glass shaping, among others.
Key Features and Advantages of Endless Diamond Wire Cutting:
- Material Versatility: Endless Diamond Wire Cutting is highly versatile, capable of cutting both conductive and non-conductive materials, making it the top choice for various industries.
- Enhanced Efficiency: Compared to traditional methods, Endless Diamond Wire Cutting typically boasts higher cutting speeds, greatly enhancing production efficiency.
- Unparalleled Precision: The use of diamond wire allows for exceptionally high cutting precision, ensuring the manufacture of high-quality components.
Comparing CNC Wire Cutting and Endless Diamond Wire Cutting:
- Material Compatibility: Traditional Computer Numerical Control Wire Cutting is primarily suited for conductive materials, whereas Endless Diamond Wire Cutting excels in cutting both conductive and non-conductive materials.
- Cutting Speed: Endless Diamond Wire Cutting often exhibits higher cutting speeds, crucial for large-scale production.
- Precision Paradigm: In terms of precision, traditional CNC Wire Cutting retains its position as an unparalleled choice for intricate and fine components.
Conclusion
CNC Wire Cutting, which traditionally referred to EDM wire cutting, has expanded its horizons with the advent of Endless Diamond Wire Cutting. While traditional Computer Numerical Control Wire Cutting excels in precision for conductive materials, Endless Diamond Wire Cutting adds versatility, cutting speed, and the ability to handle non-conductive materials into the mix. Together, these two methods offer unmatched precision and efficiency in modern industry, shaping the future of manufacturing.
“Circular diamond wire cutting” is typically a highly precise cutting method suitable for applications that require high accuracy and surface smoothness, such as semiconductor manufacturing and optoelectronics. This technology allows for the cutting of complex geometries and can, in some cases, reduce material waste.
If you need more information about “circular diamond wire cutting” technology, I would recommend consulting with relevant manufacturers or experts for further details on technical specifications and application cases. This field of technology is continuously evolving and may have various different variants and applications.