Diamond Wire Cutting: An Innovative Approach for Graphite Machining
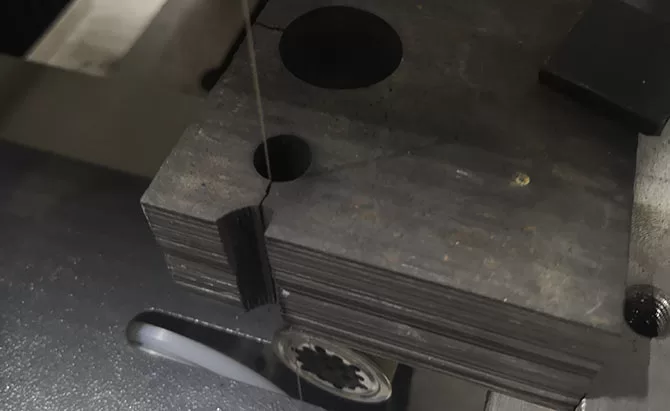
Table of Contents
Introduction
Advantages of Cutting Graphite with Diamond Wire: Diamond wire cutting, a precision machining technique, has gained significant attention in various industries for its ability to cut through hard materials with unparalleled precision and efficiency. One notable application of diamond wire cutting is in the field of cutting graphite, a naturally occurring crystalline form of carbon. In this article, we will explore the advantages of using diamond wire cutting for graphite machining and delve into how this innovative approach is revolutionizing industrial processes.
Advantages of Cutting Graphite with Diamond Wire
Precision and Accuracy:
Cutting Graphite with Diamond Wire: Diamond wire cutting is renowned for its exceptional precision and accuracy. This attribute is particularly beneficial when working with graphite, which is often used in applications demanding intricate shapes and fine details. The thin diamond-coated wire allows for intricate cuts without causing damage to the surrounding material, resulting in high-quality finished products.
Minimal Material Loss:
Cutting Graphite with Diamond Wire: Traditional machining methods for graphite, such as milling or grinding, often lead to significant material loss due to the abrasive nature of these processes. Diamond wire cutting minimizes material waste by producing thinner cuts, optimizing the use of the raw material and reducing the need for subsequent finishing operations.
Reduced Heat Generation:
Graphite is sensitive to temperature changes, and excessive heat generation during machining can result in structural changes or even fracturing. Diamond wire cutting produces less heat compared to conventional methods, making it a preferred choice for machining graphite. The controlled and low heat generation helps preserve the integrity of the material.
Smooth Surface Finish:
Cutting Graphite with Diamond Wire: Diamond wire cutting produces a smooth surface finish directly from the cutting process, eliminating the need for additional polishing or finishing steps. This not only saves time but also ensures a consistent and high-quality surface finish across the entire machined piece.
Versatility:
Diamond wire cutting is adaptable to various graphite grades and types, ranging from soft to highly crystalline graphite. This versatility allows manufacturers to address a wide range of industrial applications, from the production of intricate graphite molds to precision components for the electronics industry.
Reduced Tool Wear:
Conventional machining tools can experience rapid wear and require frequent replacement when machining graphite due to its abrasive nature. Diamond wire cutting employs durable diamond-coated wires that maintain their cutting edge for longer periods, resulting in reduced downtime and tool replacement costs.
Automation and Efficiency:
Cutting Graphite with Diamond Wire: Diamond wire cutting can be easily automated, leading to enhanced efficiency and consistency in the machining process. This is especially advantageous for mass production scenarios where precision and speed are essential.
Applications of Diamond Wire Cutting in Graphite Machining
Electrode Manufacturing:
Graphite electrodes are critical components in electric arc furnace operations for steel production. Diamond wire cutting enables the creation of intricate electrode shapes with precise dimensions, improving the efficiency and effectiveness of the steel-making process.
Mold and Die Production:
Graphite molds and dies are widely used in industries such as glass manufacturing and plastic injection molding. Diamond wire cutting allows for the rapid and accurate production of complex molds, reducing lead times and enhancing product quality.
Electronics Industry:
The electronics industry relies on graphite components for applications such as heat sinks and electrodes. Diamond wire cutting ensures the precise fabrication of these components, contributing to the overall performance and reliability of electronic devices.
Conclusion
Diamond wire cutting has emerged as a cutting-edge technology in the realm of graphite machining, offering a host of advantages that are reshaping industrial processes. Its precision, minimal material loss, reduced heat generation, and versatility make it a preferred method for various applications in industries ranging from steel production to electronics manufacturing. As technology continues to advance, diamond wire cutting is expected to play a pivotal role in enhancing the efficiency, quality, and sustainability of graphite machining processes.