Inhaltsverzeichnis
Einführung - Optoelektronisches Materialschneiden
In der sich ständig weiterentwickelnden Technologie- und Innovationslandschaft spielen optoelektronische Materialien eine entscheidende Rolle in verschiedenen Branchen, von der Telekommunikation bis zum Gesundheitswesen. Das präzise Schneiden dieser Materialien ist für die Herstellung komplizierter Komponenten mit optimalen optischen Eigenschaften unerlässlich. In diesem umfassenden Leitfaden gehen wir auf die Feinheiten des Schneidens optoelektronischer Materialien wie optisches Glas, Quarz, YAG, Ge und andere ein, von den damit verbundenen Herausforderungen bis hin zu den besten Verfahren, um makellose Ergebnisse zu erzielen.
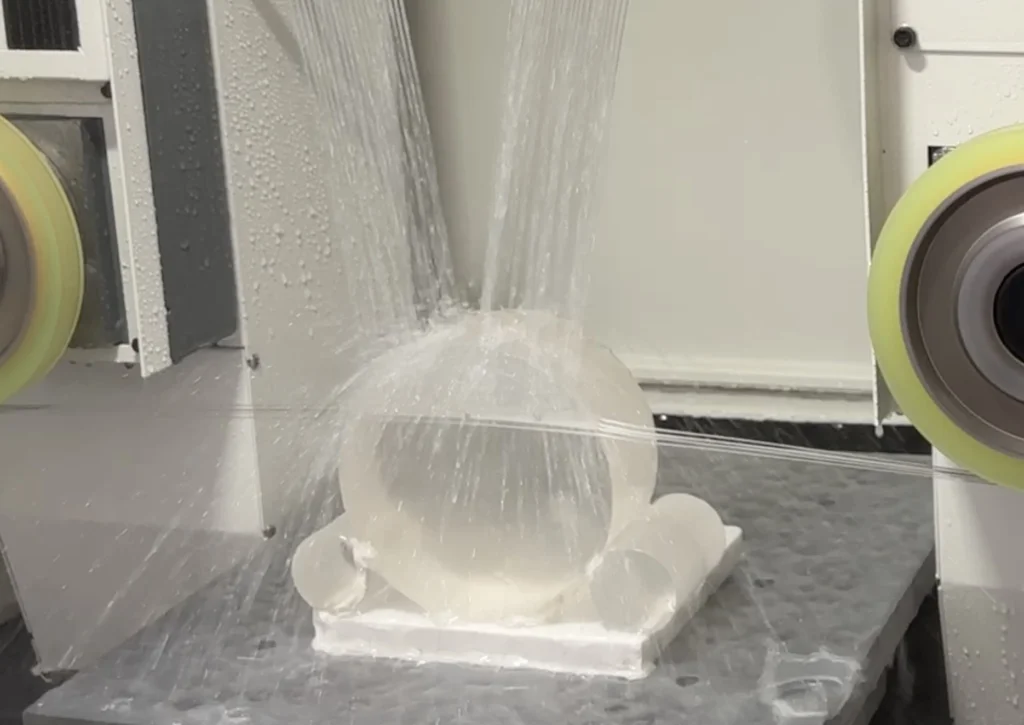
Erforschung von Schneidverfahren für optoelektronische Materialien
In der sich ständig weiterentwickelnden Technologie- und Innovationslandschaft spielen optoelektronische Materialien eine entscheidende Rolle in verschiedenen Branchen, von der Telekommunikation bis zum Gesundheitswesen. Das präzise Schneiden dieser Materialien ist für die Herstellung komplizierter Komponenten mit optimalen optischen Eigenschaften unerlässlich. In diesem umfassenden Leitfaden gehen wir auf die Feinheiten des Schneidens optoelektronischer Materialien wie optisches Glas, Quarz, YAG, Ge und andere ein, von den damit verbundenen Herausforderungen bis hin zu den besten Verfahren, um makellose Ergebnisse zu erzielen.
Vorteile | Nachteile | |
Laser schneiden | Hohe Präzision Minimaler Materialkontakt Vielseitigkeit beim Schneiden verschiedener Materialien | Begrenzte Dicke bei einigen Materialien Höherer Energieverbrauch |
Wasserstrahlschneiden | Vielseitigkeit beim Schneiden verschiedener Materialien Minimale wärmebeeinflusste Zone | Geringere Genauigkeit im Vergleich zu anderen Methoden Langsamere Schnittgeschwindigkeiten |
Mechanisches Schneiden (z. B. Sägen, Fräsen) | Geeignet für dicke Materialien Geringere Erstinvestitionskosten | Kann Oberflächenschäden verursachen Geringere Präzision Beschränkung auf bestimmte Materialien |
Abrasives Schneiden (z. B. Abrasives Wasserstrahlschneiden) | Vielseitig Geeignet für harte Materialien Minimale Wärmeentwicklung | Langsamere Schnittgeschwindigkeiten Höhere Betriebskosten durch den Einsatz von Schleifmitteln |
Diamantdrahtschneiden (DWC) | Hohe Präzision Minimale Sachschäden Effizienz Vielseitigkeit | Die anfänglichen Investitionskosten können höher sein |
Laser schneiden:
Vorteile:
Hohe Präzision: Das Laserschneiden bietet präzise und genaue Schnitte, mit der Möglichkeit, komplizierte Designs zu realisieren.
Vielseitigkeit: Das Laserschneiden eignet sich für verschiedene Materialien, darunter Metalle, Kunststoffe, Holz und Stoffe.
Minimaler Materialkontakt: Das Laserschneiden ist berührungslos und minimiert das Risiko von Materialverformungen oder -verunreinigungen.
Minimale Wärmeeinflusszone: Das Laserschneiden erzeugt schmale Schnitte und minimale thermische Verformung, wodurch die Materialintegrität erhalten bleibt.
Nachteile:
Begrenzte Dicke: Beim Laserschneiden kann die Dicke bestimmter Materialien begrenzt sein.
Höherer Energieverbrauch: Laserschneidsysteme können viel Energie verbrauchen, was zu höheren Betriebskosten führt.
Erstinvestition: Die Anschaffungskosten für Laserschneidanlagen und deren Wartung können erheblich sein.
Wasserstrahlschneiden:
Vorteile:
Vielseitigkeit: Mit dem Wasserstrahlschneiden kann eine breite Palette von Materialien geschnitten werden, darunter Metalle, Keramik, Stein und Verbundwerkstoffe.
Minimale Wärmeentwicklung: Das Wasserstrahlschneiden ist ein Kaltschneideverfahren, das das Risiko einer thermischen Schädigung der Materialien minimiert.
Umweltfreundlich: Beim Wasserstrahlschneiden werden Wasser und Abrasivstoffe verwendet, was es zu einer umweltfreundlichen Option macht.
Keine Begrenzung der Materialhärte: Das Wasserstrahlschneiden kann Materialien unterschiedlicher Härte bearbeiten, ohne dass die Schnittqualität beeinträchtigt wird.
Nachteile:
Langsamere Schnittgeschwindigkeiten: Beim Wasserstrahlschneiden sind die Schnittgeschwindigkeiten im Vergleich zu anderen Verfahren tendenziell langsamer, was die Gesamtproduktivität beeinträchtigt.
Verwendung von Abrasivmitteln: Beim Abrasiv-Wasserstrahlschneiden werden Abrasivstoffe benötigt, was zu zusätzlichen Betriebskosten führt.
Schnittfugenbreite: Das Wasserstrahlschneiden erzeugt im Vergleich zum Laser- oder Diamantseilschneiden breitere Schnittfugen, was zu Materialverlusten führt.
Mechanisches Schneiden (z. B. Sägen, Fräsen):
Vorteile:
Geringere Anfangsinvestitionen: Mechanische Schneidanlagen sind im Vergleich zu anderen Verfahren oft günstiger.
Geeignet für dicke Materialien: Mechanische Schneidverfahren sind für dicke Materialien gut geeignet.
Breites Spektrum an Anwendungen: Mechanisches Schneiden kann für verschiedene Materialien verwendet werden, darunter Metalle, Kunststoffe und Holz.
Nachteile:
Oberflächenbeschädigung: Mechanische Schneidverfahren können Oberflächenschäden wie Grate oder raue Kanten verursachen.
Geringere Präzision: Mechanisches Schneiden erreicht unter Umständen nicht den gleichen Präzisionsgrad wie Laser- oder Diamantdrahtschneidverfahren.
Begrenzt auf bestimmte Materialien: Mechanische Schneidverfahren können in ihrer Fähigkeit, bestimmte Materialien zu schneiden, eingeschränkt sein, insbesondere bei spröden oder hitzeempfindlichen Materialien.
Abrasives Schneiden (z. B. Abrasives Wasserstrahlschneiden):
Vorteile:
Vielseitigkeit: Abrasive Schneidverfahren können eine Vielzahl von Materialien bearbeiten, darunter Metalle, Keramiken und Verbundwerkstoffe.
Minimale Wärmeentwicklung: Abrasives Schneiden ist ein Kaltschneideverfahren, das das Risiko einer thermischen Schädigung der Materialien minimiert.
Geeignet für harte Materialien: Abrasives Schneiden ist effektiv für das Schneiden von harten Materialien wie Metallen und Keramik.
Minimaler Materialabfall: Das Abrasivschneiden erzeugt schmale Schnittfugen, was den Materialverlust reduziert.
Nachteile:
Höhere Betriebskosten: Abrasive Schneidverfahren erfordern abrasive Materialien, was zu höheren Betriebskosten führt.
Langsamere Schnittgeschwindigkeiten: Abrasives Schneiden hat im Vergleich zu Laser- oder Diamantdrahtschneidverfahren tendenziell langsamere Schnittgeschwindigkeiten.
Umweltaspekte: Beim Abrasivschneiden können Abrasivstaub und -abfälle entstehen, die ordnungsgemäß entsorgt werden müssen und Umweltaspekte berücksichtigen.
Vorteile des Diamantdrahtschneidens:
Diamantdrahtschneiden ist eine spezielle Schneidetechnik, die einzigartige Vorteile für das Schneiden optoelektronischer Materialien bietet:
Hohe Präzision: Das Schneiden mit Diamantdraht ermöglicht äußerst präzise Schnitte mit minimaler Verformung und ist daher ideal für Materialien, bei denen es auf Genauigkeit ankommt.
Saubere Schnitte: Die Verwendung von Diamantdraht gewährleistet saubere und glatte Schnitte, ohne die Eigenschaften des Materials zu beeinträchtigen, wie z. B. bei Quarz oder optischem Glas.
Effizienz: Das Schneiden von Diamantdraht kann effizient durchgeführt werden, was Zeit spart und den Materialabfall während des Schneidevorgangs reduziert.
Kosteneffizienz: Trotz seiner Präzision und Qualität ist das Schneiden mit Diamantdraht eine kosteneffiziente Lösung für das Schneiden einer Vielzahl von optoelektronischen Materialien.
Geringerer Materialverlust: Der dünne Diamantdraht minimiert den Materialverlust während des Schneidprozesses und maximiert die Ausbeute an wertvollen Materialien wie YAG und Ge.
Zusammenfassend lässt sich sagen, dass die Auswahl eines Schneidverfahrens für optoelektronische Materialien entscheidend ist, um qualitativ hochwertige Ergebnisse bei der Herstellung elektronischer Geräte zu erzielen. Während jede Schneidetechnik ihre eigenen Vor- und Nachteile bietet, zeichnet sich das Diamantdrahtschneiden durch seine Präzision, Effizienz, Kosteneffizienz und minimalen Materialverlust aus. Durch die Einbeziehung des Diamantdrahtschneidens in den Fertigungsprozess können Unternehmen ein Höchstmaß an Qualität und Präzision beim Schneiden optoelektronischer Materialien gewährleisten.
Schneiden mit Diamantdraht im Vergleich zu herkömmlichen Schneidmethoden
Im Bereich des Schneidens von optoelektronischen Materialien hat sich das Schneiden mit Diamantdraht als innovative Technik herauskristallisiert, die große Aufmerksamkeit erregt. Im Vergleich zu herkömmlichen Schneidverfahren bietet das Schneiden mit Diamantdraht verschiedene Vorteile und Unterschiede. In diesem Artikel befassen wir uns mit den Unterschieden zwischen dem Schneiden mit Diamantdraht und herkömmlichen Schneidverfahren.
Vorteile des Diamantdrahtschneidens:
Gesteigerte Effizienz: Beim Diamantdrahtschneiden werden Metalldrähte mit Diamantpartikeln zum Schneiden verwendet, was schnellere Schnittgeschwindigkeiten und eine höhere Produktionseffizienz ermöglicht.
Hohe Präzision: Mit Diamanten, die für ihre extreme Härte bekannt sind, wird beim Schneiden von Diamantdraht eine bemerkenswerte Präzision erreicht, die für glatte und genaue Schnittkanten sorgt.
Geringere Materialbeschädigung: Im Vergleich zu herkömmlichen Methoden minimiert der berührungslose Charakter des Diamantdrahtschneidens die Materialbeschädigung und -verformung, was insbesondere bei spröden Materialien wie optischem Glas von entscheidender Bedeutung ist.
Breite Anwendbarkeit: Das Schneiden mit Diamantdraht ist für eine Vielzahl von optoelektronischen Materialien geeignet, darunter optisches Glas, Quarz, YAG und Ge, was die Vielseitigkeit unterstreicht.
Grenzen traditioneller Schneideverfahren:
Geringere Präzision: Herkömmliche Schneidemethoden erreichen unter Umständen nicht die gleiche Präzision wie das Schneiden mit Diamantdraht, so dass sie für Anwendungen, die eine hohe Schnittgenauigkeit erfordern, weniger geeignet sind.
Beschädigung und Verformung: Einige herkömmliche Schneidverfahren, wie z. B. das mechanische Schneiden, können zu Oberflächenbeschädigungen und Verformungen führen, die die Schnittqualität beeinträchtigen.
Materialbeschränkungen: Bestimmte herkömmliche Schneidverfahren können Einschränkungen bei der Materialauswahl mit sich bringen, da sie nicht in der Lage sind, optoelektronische Materialien mit spezifischen Eigenschaften zu verarbeiten.
Zukunftsperspektiven des Diamantdrahtschneidens:
Mit den laufenden technologischen Fortschritten und der Ausweitung der Anwendungsbereiche bietet das Schneiden mit Diamantdraht vielversprechende Aussichten im Bereich des Schneidens von optoelektronischen Materialien. Ihre Effizienz, Präzision und breite Anwendbarkeit machen sie zur bevorzugten Schneidmethode für eine wachsende Zahl von Herstellern optoelektronischer Materialien.
Das Schneiden mit Diamantdraht hebt sich von herkömmlichen Schneidverfahren durch seine offensichtlichen Vorteile ab, darunter erhöhte Effizienz, Präzision, geringere Materialbeschädigung und breite Anwendbarkeit. Im Zuge der weiteren technologischen Entwicklung wird das Schneiden mit Diamantdraht eine immer wichtigere Rolle im Bereich des Schneidens optoelektronischer Materialien spielen.
Zusammenfassend lässt sich sagen, dass das Schneiden mit Diamantdraht eine überzeugende Alternative zu herkömmlichen Methoden darstellt und den Weg für eine verbesserte Produktivität und Qualität bei der Herstellung optoelektronischer Materialien ebnet.
Herausforderungen beim Schneiden optoelektronischer Materialien
Im Bereich der optoelektronischen Materialien ist das Präzisionsschneiden ein entscheidender Schritt, der sorgfältige Überlegungen und Fachwissen erfordert. Von optischem Glas bis hin zu Quarz, YAG und Ge stellt jedes Material seine eigenen Herausforderungen an den Schneidprozess. In diesem SEO-optimierten Artikel gehen wir auf diese Herausforderungen ein und geben Einblicke, wie man sie für optimale Ergebnisse meistert.
Verständnis für die einzigartigen Herausforderungen:
Optisches Glas:
Optisches Glas, das für seine Transparenz und optische Klarheit geschätzt wird, stellt aufgrund seiner Sprödigkeit eine Herausforderung dar. Das Erzielen präziser Schnitte ohne Mikrorisse oder Oberflächenfehler ist von größter Bedeutung.
Quarz:
Quarz, das für seine Härte und Haltbarkeit bekannt ist, erfordert spezielle Schneidetechniken, um Abplatzungen und Brüche zu vermeiden. Die Unversehrtheit der Quarzoberfläche während des Schneidens ist entscheidend für den Erhalt der optischen Eigenschaften des Materials.
YAG (Yttrium-Aluminium-Granat):
YAG-Kristalle, die häufig in Laseranwendungen eingesetzt werden, müssen präzise geschnitten werden, um Defekte zu vermeiden, die die Laserleistung beeinträchtigen könnten. Die Erhaltung der Integrität der Kristallstruktur und die Minimierung der Oberflächenrauhigkeit sind zentrale Herausforderungen.
Germanium (Ge):
Germanium, das für seine optischen Eigenschaften in Infrarotanwendungen geschätzt wird, stellt aufgrund seines hohen Brechungsindex und seiner Empfindlichkeit gegenüber Oberflächenbeschädigungen eine Herausforderung dar. Präzises Schneiden ist unerlässlich, um die optische Qualität und Funktionalität von Germanium zu erhalten.
Strategien zur Bewältigung von Herausforderungen:
Fortgeschrittene Schneidetechniken:
Verwenden Sie fortschrittliche Schneidmethoden, wie z. B. das Schneiden mit Diamantdraht, die eine hohe Präzision bieten und die Materialbeschädigung im Vergleich zu herkömmlichen Methoden minimieren.
Optimierte Schnittparameter:
Feinabstimmung der Schnittparameter wie Schnittgeschwindigkeit, Vorschub und Abrasivmittelkonzentration zur Gewährleistung einer optimalen Schnittleistung bei gleichzeitiger Minimierung der Oberflächenfehler.
Spezialisierte Ausrüstung und Werkzeuge:
Investieren Sie in spezielle Schneidausrüstung und Werkzeuge, die speziell für optoelektronische Materialien entwickelt wurden, um präzise Schnitte und minimalen Materialabfall zu gewährleisten.
Kontrolle der Oberflächenqualität:
Einführung strenger Qualitätskontrollmaßnahmen zur Überwachung der Oberflächenqualität während und nach dem Schneiden, unter Verwendung von Techniken wie Oberflächenprofilometrie und optischer Mikroskopie.
Um die Herausforderungen beim Schneiden optoelektronischer Materialien zu meistern, bedarf es einer Kombination aus Fachwissen, fortschrittlichen Techniken und Spezialausrüstung. Durch das Verständnis der einzigartigen Eigenschaften und Herausforderungen von Materialien wie optischem Glas, Quarz, YAG und Ge können Hersteller ihre Schneidprozesse optimieren, um hervorragende Ergebnisse zu erzielen. Mit dem Fokus auf Präzision und Qualität können sie die Anforderungen der verschiedenen Anwendungen in der Optik, Photonik und darüber hinaus erfüllen.
Warum sollten Sie sich für Diamantdrahtschneideverfahren entscheiden?
Die Entscheidung für das Schneiden mit Diamantdraht bietet mehrere überzeugende Vorteile und macht es zu einer bevorzugten Methode für das Schneiden verschiedener Materialien, einschließlich optoelektronischer Materialien wie optisches Glas, Quarz, YAG und Ge. Hier sind einige Gründe, warum das Schneiden mit Diamantdraht so besonders ist:
Präzision: Beim Schneiden mit Diamantdraht werden außergewöhnlich präzise Schnitte mit minimalem Materialverlust erzielt. Der dünne diamantbeschichtete Draht ermöglicht das präzise Schneiden komplizierter Formen und Abmessungen und erfüllt die engen Toleranzen, die bei optoelektronischen Anwendungen erforderlich sind.
Minimale materielle Schäden: Im Gegensatz zu herkömmlichen Schneidverfahren, die thermische Spannungen, Mikrorisse oder Oberflächendefekte hervorrufen können, erfolgt das Schneiden mit Diamantdraht mit minimalem Kontakt, wodurch das Risiko einer Materialbeschädigung verringert wird. Dies ist besonders wichtig für spröde Materialien wie optisches Glas und Quarz.
Hohe Effizienz: Das Schneiden mit Diamantdraht bietet hohe Schnittgeschwindigkeiten und ermöglicht eine schnelle Produktion bei gleichbleibender Präzision. Diese Effizienz führt zu höherer Produktivität und kürzeren Vorlaufzeiten, was Fertigungsprozessen in verschiedenen Branchen zugute kommt.
Vielseitigkeit: Das Schneiden mit Diamantdraht ist äußerst vielseitig und eignet sich zum Schneiden einer breiten Palette von Materialien, von weichen Metallen bis zu harter Keramik. Diese Vielseitigkeit macht sie ideal für das Schneiden verschiedener optoelektronischer Materialien und bietet eine einzige Lösung für verschiedene Schneidanforderungen.
Kosten-Nutzen-Verhältnis: Auch wenn die Anfangsinvestitionen in Diamantdrahtschneideanlagen im Vergleich zu herkömmlichen Methoden höher sein mögen, sind die langfristigen Kostenvorteile erheblich. Weniger Materialverschwendung, geringerer Wartungsaufwand und höhere Produktivität tragen zur Gesamtwirtschaftlichkeit bei.
Saubere Schnittumgebung: Beim Schneiden mit Diamantdraht entstehen im Vergleich zu anderen Schneidverfahren nur minimale Rückstände und Staub, was zu einer saubereren und sichereren Arbeitsumgebung beiträgt. Dies ist vorteilhaft für Branchen mit strengen Sauberkeitsstandards, wie z. B. die Halbleiterfertigung.
Umwelterwägungen: Das Schneiden mit Diamantdraht ist ein nachhaltiges Schneidverfahren, das die Auswirkungen auf die Umwelt minimiert. Durch den geringeren Energieverbrauch und die reduzierte Abfallerzeugung steht es im Einklang mit umweltfreundlichen Fertigungsverfahren und Nachhaltigkeitszielen.
Qualitätssicherung: Das Schneiden von Diamantdraht gewährleistet konsistente und hochwertige Schnitte, die den strengen Qualitätsstandards für optoelektronische Anwendungen entsprechen. Diese Zuverlässigkeit erhöht die Produktqualität und die Kundenzufriedenheit.
Das Schneiden mit Diamantdraht bietet eine ganze Reihe von Vorteilen, darunter Präzision, minimale Materialbeschädigung, Effizienz, Vielseitigkeit, Kosteneffizienz, Sauberkeit, Umweltverträglichkeit und Qualitätssicherung. Diese Vorteile machen sie zu einer ausgezeichneten Wahl für das Schneiden von optoelektronischen Materialien und anderen fortschrittlichen Werkstoffen in verschiedenen Branchen.
Abschluss
Das Schneiden von optoelektronischen Materialien erfordert ein empfindliches Gleichgewicht von Präzision, Fachwissen und Technologie. Im Bereich des Schneidens von optoelektronischen Materialien erweist sich das Schneiden mit Diamantdraht als die optimale Lösung, die unvergleichliche Präzision, minimale Materialbeschädigung, Effizienz und Vielseitigkeit bietet. Seine Fähigkeit, die strengen Anforderungen optoelektronischer Anwendungen zu erfüllen und gleichzeitig kosteneffizient zu sein, macht es zu einer bevorzugten Wahl für Hersteller weltweit. Durch den Einsatz des Diamantdrahtschneidens können Hersteller neue Möglichkeiten beim Schneiden optoelektronischer Materialien erschließen und Innovationen in der sich ständig weiterentwickelnden Technologie- und Fertigungslandschaft vorantreiben.