Table of Contents
Introduction
In the realm of precision cutting, the diamond cutting wire loop emerges as a remarkable technological innovation, revolutionizing how materials are sliced in various industries. From the intricate world of semiconductor manufacturing to the rugged terrains of stone quarrying, the diamond cutting wire loop has proven to be an indispensable tool. This article delves deep into the world of diamond cutting wire loops, offering a comprehensive understanding of their mechanism, applications, benefits, and the latest advancements in this field.
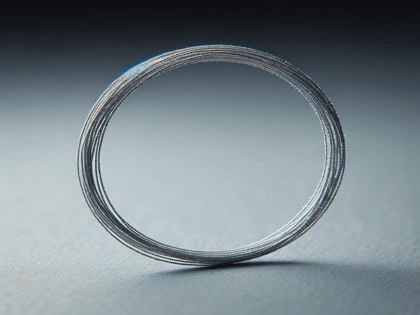
The Essence of Diamond Cutting Wire Loop
Understanding the Tool
At its core, a diamond cutting wire loop is a sophisticated cutting instrument, equipped with diamond particles, the hardest naturally occurring material on Earth. These particles are embedded onto a strong wire base, typically made of steel, forming a loop. The fusion of diamond grit with the flexible wire creates a cutting tool that combines hardness with flexibility, a combination perfect for precision cutting.
Historical Background
Tracing back to its origin, the concept of using diamonds for cutting has been around for centuries; however, the adaptation of this concept into a wire loop format is a relatively modern innovation. It was in the 20th century that the diamond wire loop began to take its current form, driven by the need for more precision and efficiency in industrial cutting.
Types of Diamond cutiing wire loop
there are 3 types of diamond wire loop, click product page to learn more
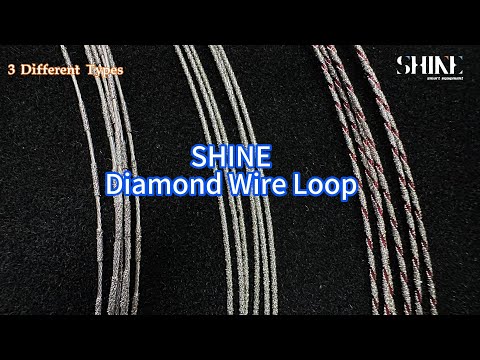
Detailed Composition and Design
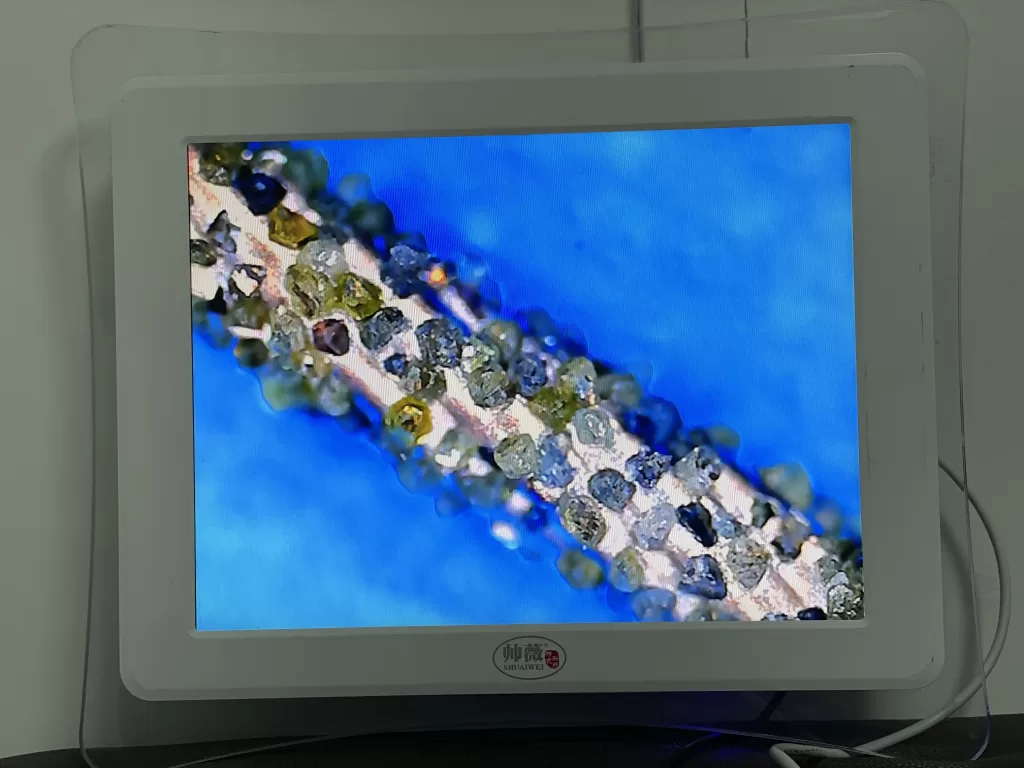
Materials Used
The efficacy of a diamond cutting wire loop primarily hinges on the quality of diamonds used. Typically, synthetic diamonds are preferred due to their uniformity and strength. These diamonds are carefully embedded onto the wire in a specific pattern, ensuring consistent cutting ability along the entire length of the wire.
Wire Design
The wire base is usually a high-strength steel or another durable alloy, designed to withstand the stresses of cutting while maintaining flexibility. The diameter of the wire and the size of the diamond particles are calibrated according to the intended use, balancing cutting speed with the lifespan of the wire.
Mechanism of Operation
Cutting Process
The diamond cutting wire loop operates by moving at high speeds, with the diamond particles grinding through the material. This abrasive process results in a precise and clean cut, with the ability to make both straight and curved cuts.
Efficiency and Precision
This method is highly efficient, offering significant improvements over traditional cutting techniques such as sawing or drilling. The precision of the cut, combined with the reduced risk of material damage, makes it an ideal choice for delicate operations.
Diverse Applications
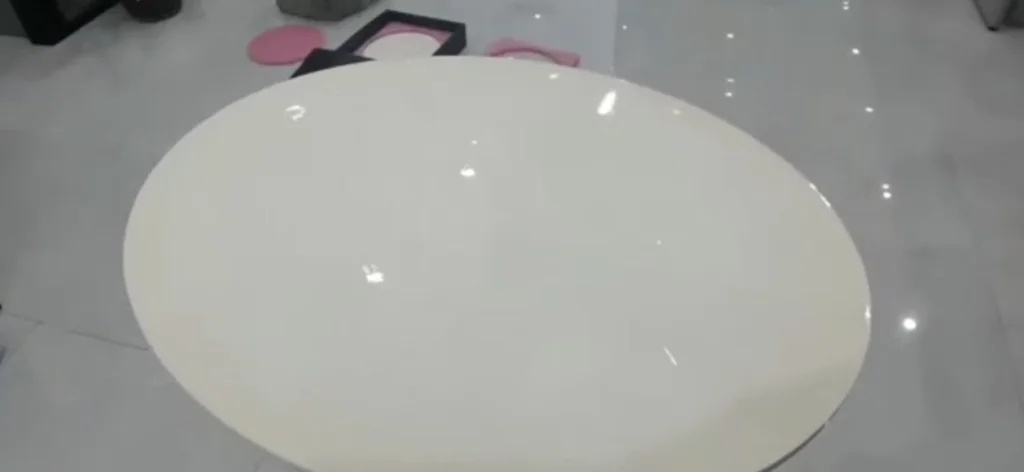
Semiconductor Industry
In semiconductor manufacturing, diamond cutting wire loops are essential for cutting silicon rod’s top and tail. Their precision ensures uniform cutting surfaces and increased cutting efficiency.
Aerospace
Utilized for cutting hard metals and composite materials used in aerospace and defense equipment manufacturing.
Optics Industry
Applied in precision cutting of glass materials, including toughened glass and specialty glasses used in various applications.Used for precision cutting of optical components such as lenses and prisms.
Other Uses
Beyond these industries, diamond wire loops are also used in construction for cutting concrete and in metalworking for slicing through hard metals, showcasing their versatility.
Advantages and Innovations
Advantages of Diamond Cutting Wire Loops
The diamond cutting wire loop offers several key advantages:
- Precision and Consistency: It provides unrivaled precision, crucial for applications requiring meticulous detailing.
- Reduced Waste: The fine cutting ability minimizes material wastage, enhancing resource efficiency.
- Speed: Its ability to cut quickly without compromising quality significantly reduces operation time.
Technological Innovations
make the diamond wire into a closed loop, highly improved cutting efficency and the machine structure was simple too because of the simple cutting tool.
Conclusion
Diamond cutting wire loop technology stands as a testament to the advancements in precision manufacturing. Its applications across various industries underscore its versatility and efficiency. As technology continues to evolve, we can expect further innovations that will enhance its effectiveness and sustainability, solidifying its role as a vital tool in modern manufacturing.