Keywords: edm wire cut machine,wire cut machine
Introduction to edm wire cut machine
In the realm of advanced engineering and manufacturing, the evolution of cutting technologies has been pivotal in shaping modern production techniques. Among these, the loop diamond wire saw and the electrical discharge machining (EDM) wire cut machine stand out as significant innovations.
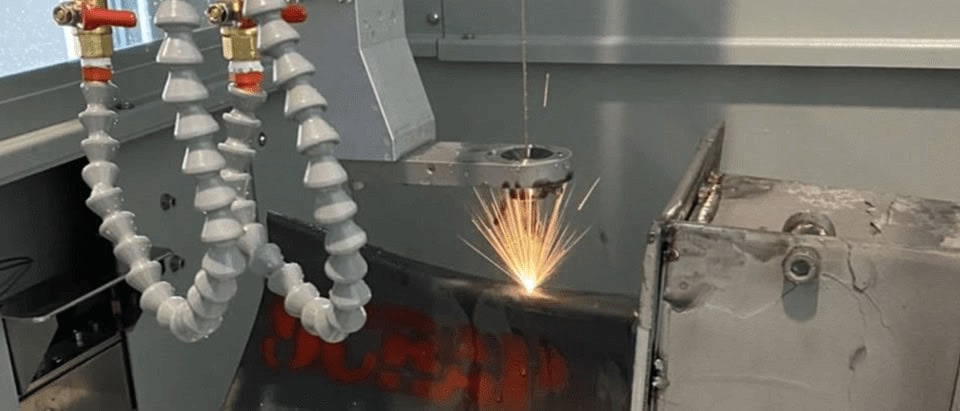
These tools have revolutionized the way materials are cut, offering precision and efficiency previously unattainable with traditional methods. The loop diamond wire saw, known for its exceptional accuracy and versatility, is ideal for slicing through hard materials like stone, silicon, and metals.
On the other hand, the EDM wire cut machine, leveraging the power of electrical discharges, excels in cutting intricate shapes and patterns in conductive materials. This article, from a professional engineer’s perspective, delves into the intricacies of these technologies, exploring their applications, benefits, and the remarkable ways they have transformed the engineering landscape.
Overview of Loop Diamond Wire Saw Technology
The loop diamond wire saw is an advanced cutting technology characterized by a metal wire embedded with diamond particles, forming a continuous loop. This wire, driven by a series of pulleys, slices through materials with precision and minimal waste. Here’s a deeper look into its workings:
Basic Principle: The cutting process of a loop diamond wire saw involves using the abrasive nature of diamonds to grind through the material. The wire, typically made of stainless steel, is coated with diamond grit. As the wire moves at high speed, it creates a cutting action that is both precise and consistent.
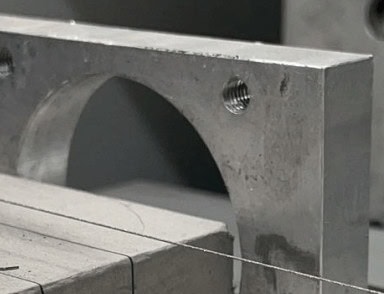
Key Components:
- Diamond Wire: The core element, where the diamonds act as the cutting medium.
- Drive Wheel and Tensioning System: These components keep the wire under appropriate tension and guide its motion.
- Pulley System: A series of pulleys guide the wire in a loop, allowing for continuous cutting action.
- Cooling and Lubrication System: To prevent overheating and reduce wear on the wire, a cooling system is employed, often using water or oil-based lubricants.
Functioning: The loop diamond wire saw operates by moving the diamond-embedded wire through the material at high speeds. The abrasiveness of the diamond particles grinds away at the material, creating a narrow cut with high precision. This technology is particularly effective for slicing through hard materials, such as granite, quartz, and even semiconductor materials like silicon.
Advantages: This technology offers several benefits:
- High Precision: Allows for cutting with great accuracy, producing clean and smooth surfaces.
- Reduced Material Waste: The narrow cut reduces material waste, making it an efficient and cost-effective solution.
- Versatility: Capable of cutting a wide range of materials, including those that are hard or brittle.
Advantages of Loop Diamond Wire Saw in Engineering
The loop diamond wire saw has emerged as a cornerstone in modern engineering due to its unique set of advantages. These benefits not only enhance the cutting process but also contribute to broader operational efficiencies and environmental considerations.
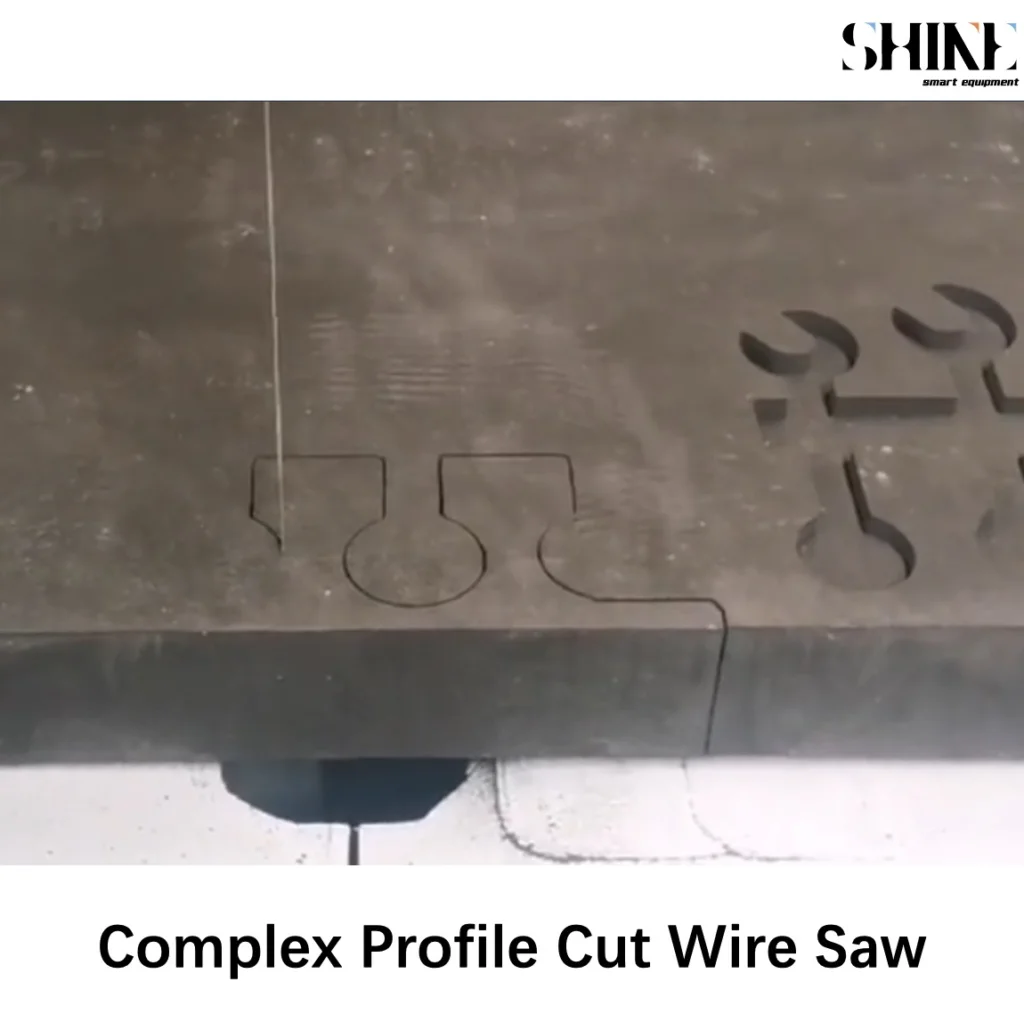
1. Precision and Efficiency: The foremost advantage of the loop diamond wire saw is its unparalleled precision. The ability to produce cuts with such exactness is crucial in industries where dimensions and tolerances are critical, such as in semiconductor manufacturing and precision engineering. This precision, combined with high cutting speeds, results in increased efficiency, reducing production time significantly.
2. Material Versatility: Another significant benefit is its versatility in handling various materials. From the hardest of stones to delicate semiconductor materials, the loop diamond wire saw can handle a diverse range of substances without compromising on the quality of the cut. This versatility makes it a valuable tool across multiple industries, including construction, electronics, and automotive sectors.
3. Reduced Waste and Environmental Impact: In an era where sustainable practices are increasingly important, the loop diamond wire saw stands out for its minimal waste production. The narrow kerf (cut width) of the wire means less material is wasted during the cutting process. This efficiency not only reduces material costs but also lessens the environmental impact by minimizing waste generation.
4. Enhanced Safety and Reduced Labor: The automated nature of the loop diamond wire saw reduces the need for manual intervention, enhancing safety on the production floor. With fewer manual tasks, the risk of accidents is significantly lowered, making it a safer option compared to traditional cutting methods.
5. Cost-Effective Over Time: While the initial investment in a loop diamond wire saw can be significant, its long-term cost-effectiveness is noteworthy. The reduced material waste, high efficiency, and lower labor requirements contribute to substantial cost savings over time, making it a financially viable option for many businesses.
EDM Wire Cut Machine: A Comparative Analysis
Electrical Discharge Machining (EDM) wire cut machines represent another frontier in precision cutting technology. While they share the common goal of precise material cutting with loop diamond wire saws, their operating principles and applications vary significantly.
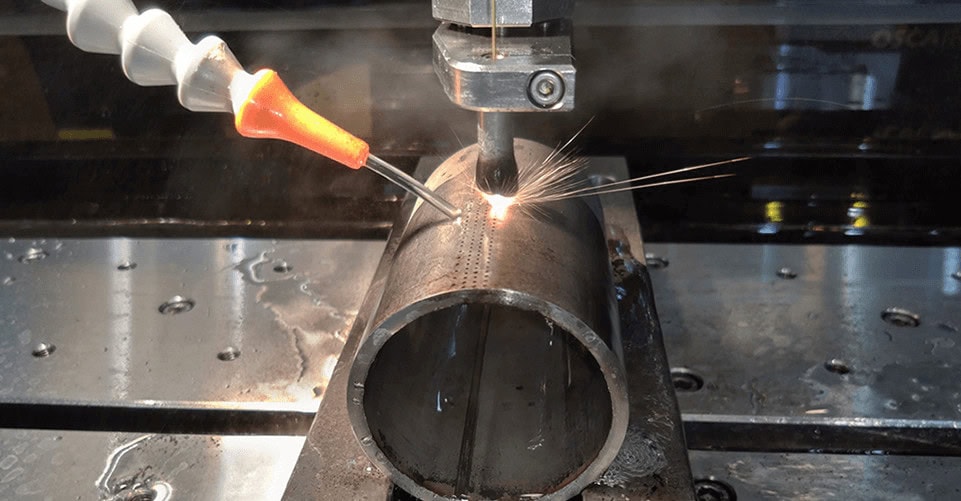
Operating Principle: Unlike the physical cutting action of the loop diamond wire saw, EDM wire cut machines use a series of rapid electrical discharges (sparks) to erode material away. A thin wire, usually made of brass or copper, acts as an electrode and is continuously fed through the workpiece. The sparks occur in a dielectric fluid, typically deionized water, which also helps in flushing away the eroded material.
Key Differences:
- Cutting Mechanism: EDM relies on electrical discharges, not physical abrasion. This allows for cutting extremely hard materials, including those that are difficult to machine using conventional methods.
- Material Suitability: EDM is best suited for conductive materials, limiting its use compared to the more versatile loop diamond wire saw.
- Precision and Complexity: While both technologies offer high precision, EDM excels in producing intricate designs and complex shapes, which might be challenging for wire saws.
- Surface Finish: EDM typically results in a smoother surface finish, reducing the need for additional surface processing.
Applications: EDM wire cut machines find extensive use in tool and die making, aerospace, and medical device manufacturing, where intricate shapes and fine details are paramount. They are particularly valued in creating complex parts, molds, and components with tight tolerances.
Despite these differences, both the loop diamond wire saw and the EDM wire cut machine have their unique places in modern engineering.