-Wire Cut For Metal/Electric Discharge Machining
Table of Contents
EDM Metal Cut Machine Brief Description
EDM Wire Cutting is a type of mechanical equipment that utilizes the principle of electric spark discharge for metal cut.
It generates electric sparks in a working fluid and uses the high temperature and energy characteristics of the sparks to melt and corrode metal, achieving cutting, processing, and shaping of metal materials. This cutting method is commonly employed for processing hard alloys, mold steel, and other challenging materials, offering high precision and efficiency.
EDM Wire Cutting Machine Client On-site Video
Unique advantages of the DK 7745 EDM Metal Cut Machine
- “pyramid” cross slide structure bed, box structure design, the machine tool has sufficient static and dynamic stiffness, reliable operation, simple operation, convenient maintenance, and conforms to the principle of ergonomics;
- All castings are cast by resin sand process, with long-time natural aging, secondary tempering and complete elimination of internal stress, which improves the rigidity and precision retention of castings; The rigidity of the edm wire cutting machine tool is increased and the deformation is reduced.
- The guide rail is made of bearing structural steel, and the quenching hardness is between hrc56 and 60, ensuring the wear resistance of the guide rail.
- The lead screw adopts ball lead screw with high rolling accuracy and strong wear resistance.
- The worktable and wire carriage are rolled with precision rollers respectively, with smallfriction, stable movement and strong wear resistance.
- All machine tool components and parts are finished by high-end processing equipment such as large grinder and precision machining center to ensure the geometric accuracy and matching accuracy of parts
- The workbench is equipped with T-shaped groove to facilitate the installation and adjustment of workpieces. It is equipped with waterproof cover to effectively prevent the splash of saponification liquid, which is environmentally friendly, beautiful and durable; The fuselage adopts environmental protection closed structure;
- The screw barrel is welded from thin-walled seamless steel pipe, with dynamic balance detection and small static and dynamic runout; Chrome plated surface, durable and wear-resistant, not easy to produce scratches;
- Variable frequency speed regulation of wire conveying motor, stable operation, low noise, installation of molybdenum wire at low speed, safe and reliable, and wide speed regulation range
- No transformer, no power resistance, no cooling fan, fully enclosed structure, greatly reducing noise, equipment noise ≤ 70dB, and no heat is emitted; Therefore, it can keep clean and not easy to damage than other electrical appliances.
- The high-frequency circuit adopts high-performance digital pulse power supply and patented high-frequency constant current source technology, which has the function of limiting peak current and short-circuit current, reducing the probability of wire breakage. In the cutting process, it has the function of Closed-loop Detection and control, that is, detecting the discharge state and dynamically adjusting the discharge gap to make the cutting stable, especially in the cutting of large thickness materials, this stability and reliability is more obvious;
- Non resistance constant current drive, low power consumption, energy saving and reliable;
- Intuitive, convenient and modifiable parameter library (9 groups in total). Users can flexibly save cutting parameters, straightening and edge collision electrical parameters of different materials, different heights, different speeds and different surface roughness. This design reduces the process requirements of machine tool operators and simplifies and facilitates machine tool operation
Get In Touch
EDM Wire Cutting Machine Product Detail
The working principle of this edm wire cutting machine
NO. | Item | Parameters |
---|---|---|
1 | Main type | GB DK7745, High speed |
2 | Electrical cabinet form | Vertical cabinet (full step type) |
3 | Guide | Steel rail |
4 | Lead screw form | Ball screw |
5 | XYUV motion motor form | Reactive stepping motor |
6 | Working mode of wire conveying motor | Frequency converter speed regulation 1 ~ 12m /s |
7 | Machine tool protection | Environmental protection cover |
8 | Resolution of motion axis | 0.001mm |
9 | Table size | 580*850 |
10 | X/ Y axial stroke | 450*550mm11 |
11 | U, V axis travel | ±30*±30mm |
12 | Machining taper / machining thickness | ±6°/80mm Standard |
13 | Maximum straight cutting thickness | 400mm |
14 | Control mode | 4 axis linkage |
15 | Maximum load capacity | 300kg |
16 | Maximum processing current | 12 A |
17 | Maximum processing efficiency Cr12, H=60mm | ≥180 mm²/m |
18 | Surface roughness (straight cutting, H≤40mm) | Ra≤1.6-2.0μm |
19 | Cutting accuracy Cr12, H=40mm | ≤0.012mm |
20 | Radial runout of wire storage cylinder | ≤0.02mm |
21 | Molybdenum wire diameter range | 0.12~0.22mm |
22 | Wire storage capacity of wire storage cylinder | 250m |
23 | Molybdenum wire loss Cr12, H=40mm | ≤0.02mm /300000mm² |
24 | Cutting power supply | High frequency power supply system without resistance |
25 | Operating system | Windows XP |
26 | Control system | AUTOCUT |
27 | Communication interface | LAN、RS232、USB |
28 | Operation function | Drawing or CAD drawing import |
29 | Working tank volume | 55L |
30 | Working fluid filtration mode | Filter screen filtration |
31 | Weight of whole machine | 1700 kg |
32 | Overall dimension of main engine | 190013001800mm |
33 | Cabinet size | 7306301820mm |
34 | Rated power of electric appliance | ≤ 2.7 kW |
Other Edm Wire Cutting Machine Models with Same Structure
there are machine of different size and additional functio to cut different material size and type.
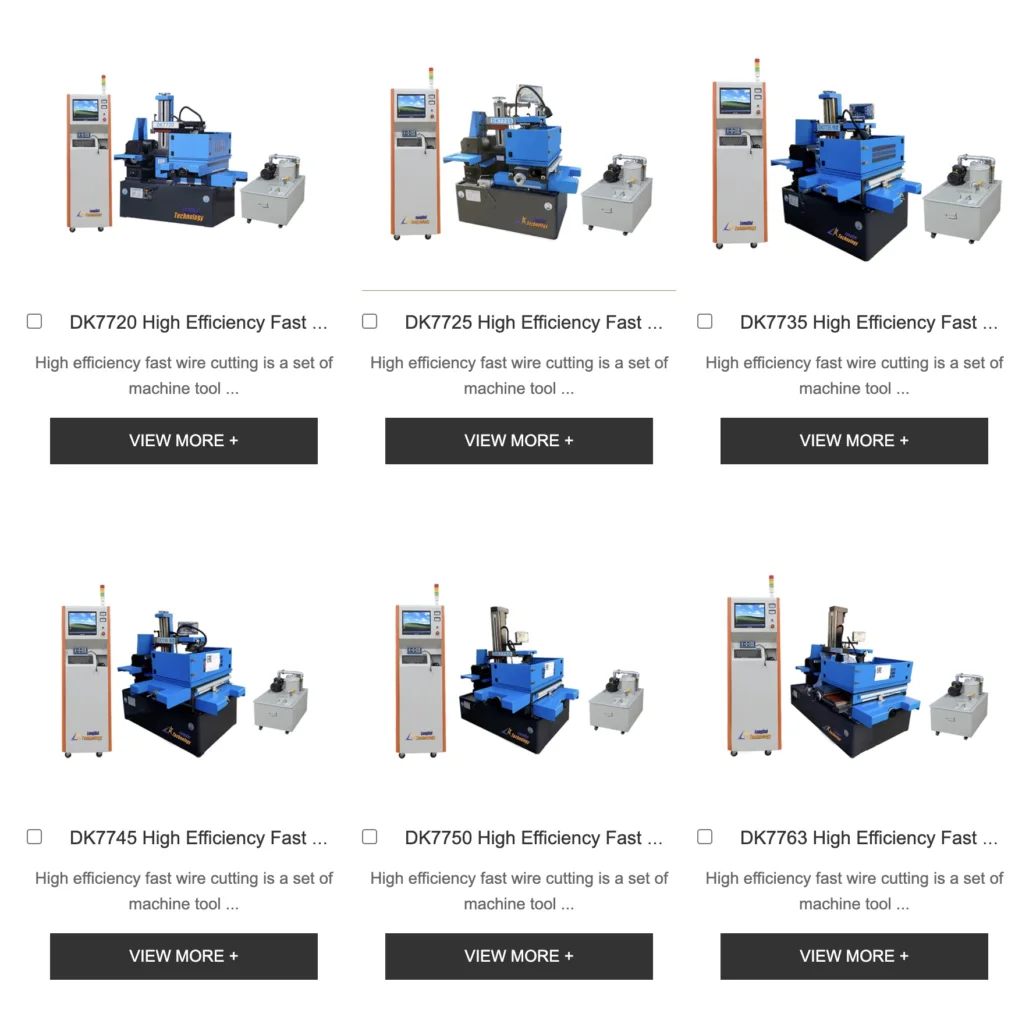
Pictures of successful case of edm wire cutting
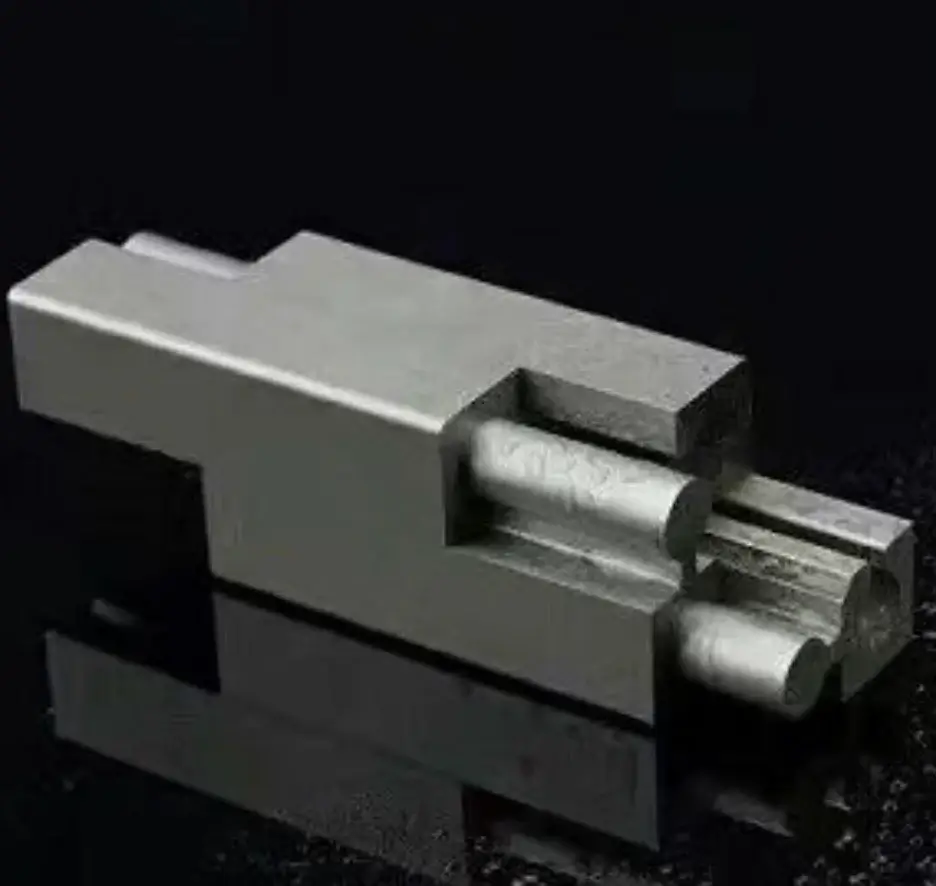
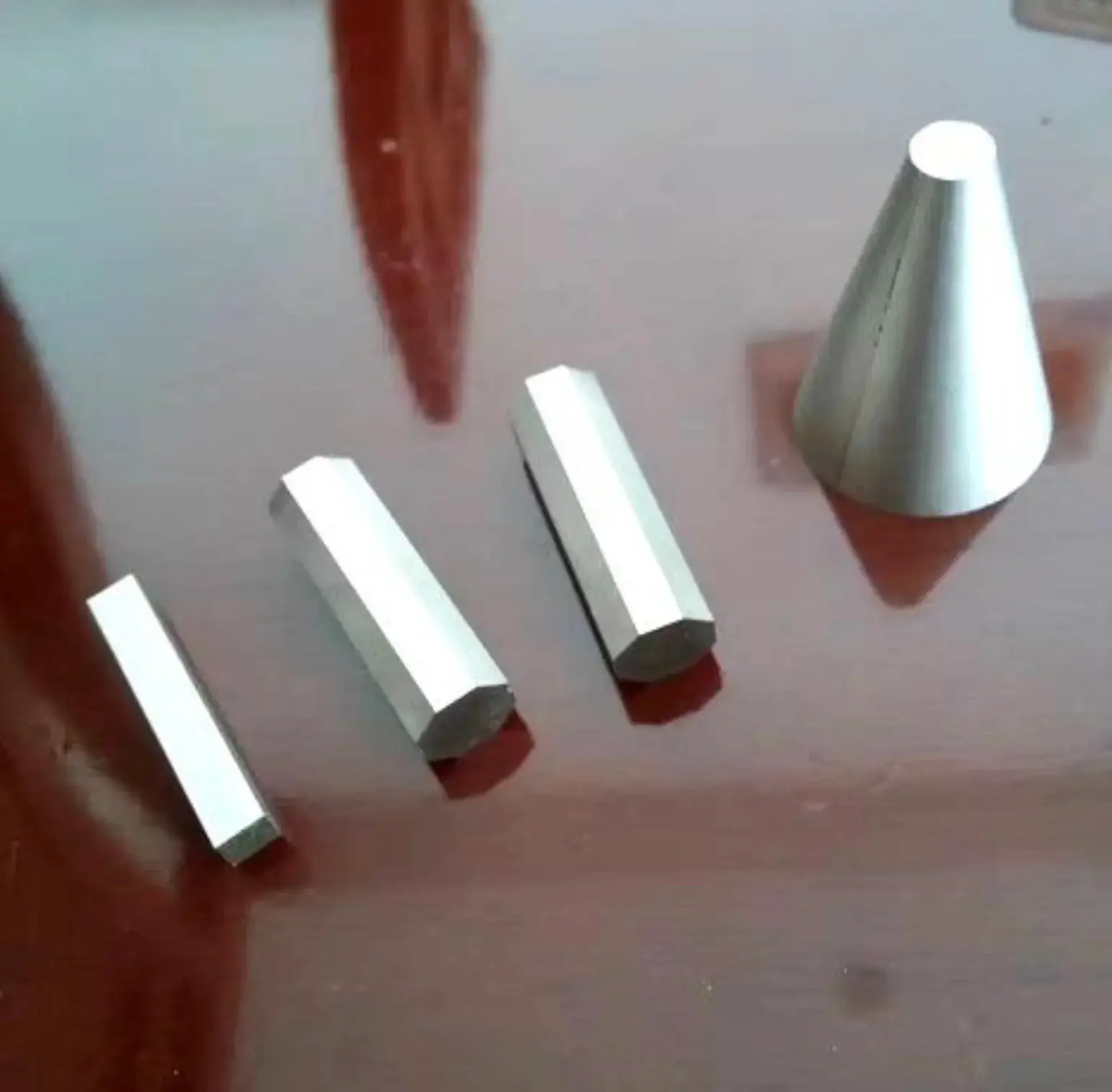

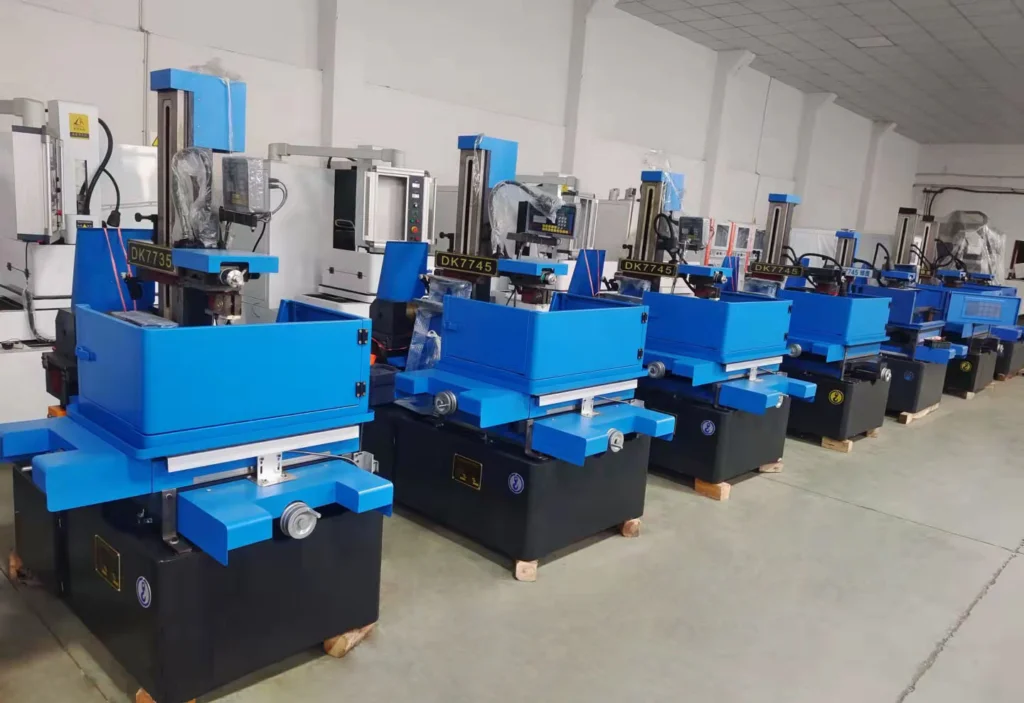
Support and Services
Maintenance and Servicing:
We provide comprehensive maintenance and servicing services to ensure the long-term reliable operation of the silicon rod cutting equipment. Our dedicated maintenance team possesses extensive experience and technical knowledge to promptly respond to and resolve equipment issues. We made check list to conduct regular preventive maintenance, inspecting and adjusting critical components to ensure optimal performance and accuracy. Whether it’s routine maintenance or emergency repairs, we are committed to delivering fast and efficient servicing to minimize equipment downtime.
Training:
We offer comprehensive training programs designed to empower customers with in-depth knowledge and proficiency in operating and maintaining the silicon ingot cutting machine. Our training courses cover basic equipment operation, safe usage practices, maintenance procedures, and troubleshooting. Customized training content and flexible training methods, including on-site training, remote training, and provision of training materials, are provided based on customer needs and backgrounds. Through our training programs, customers can enhance their operational skills, improve equipment efficiency, and ensure long-term reliable performance.
Consulting:
We provide professional consulting services to meet customer needs regarding silicon ingot cutting machine and related areas. Our team of experts offers tailored advice and solutions based on specific requirements. Whether it’s equipment selection, process optimization, production line layout, or quality control, we collaborate with customers, providing professional guidance and technical support. We strive to establish long-term partnerships with customers, working together to address various technical and engineering challenges, meet their needs, and achieve mutual success.
Perfectly Solve Your Cutting Problems
Vertical wirecutting machine can be adapted to all cutting scene with an satisfying performance
We accept sample cutting service, leave your information and enjoy our free cutting test service →
-1536x1024.jpg)
-1-1536x886.jpg)
.jpg)
-1024x683.jpg)
-1536x1024.jpg)
-1-1536x861.jpg)
-1024x683.jpg)
-1536x1024.jpg)
-1536x1024.jpg)
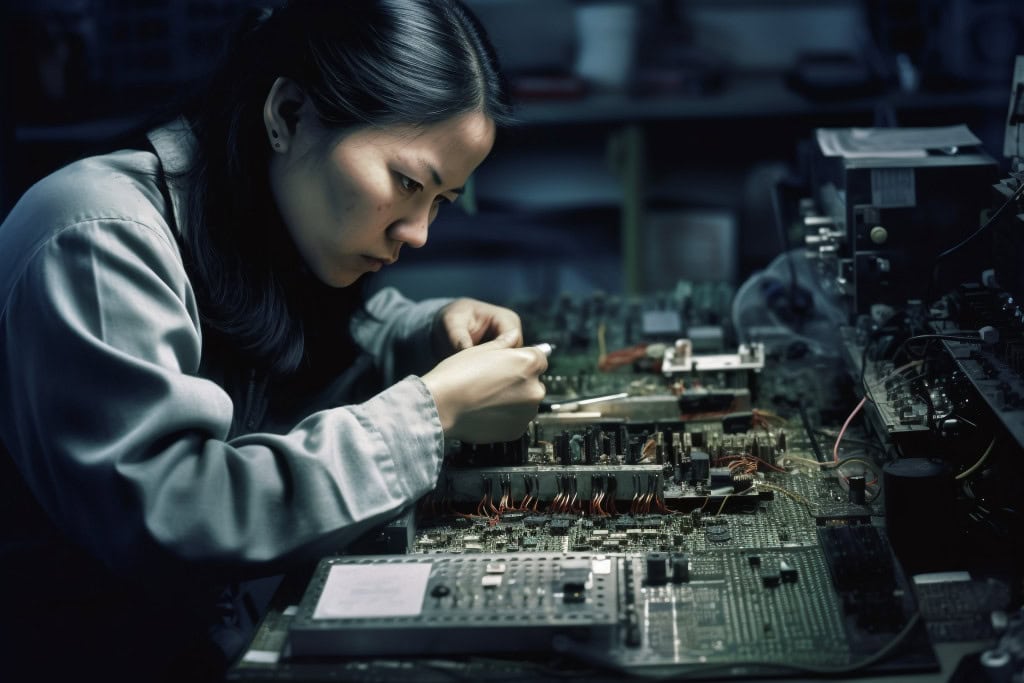