Palabras clave: Corte de hilo por descarga eléctrica, hilo diamantado sin fin
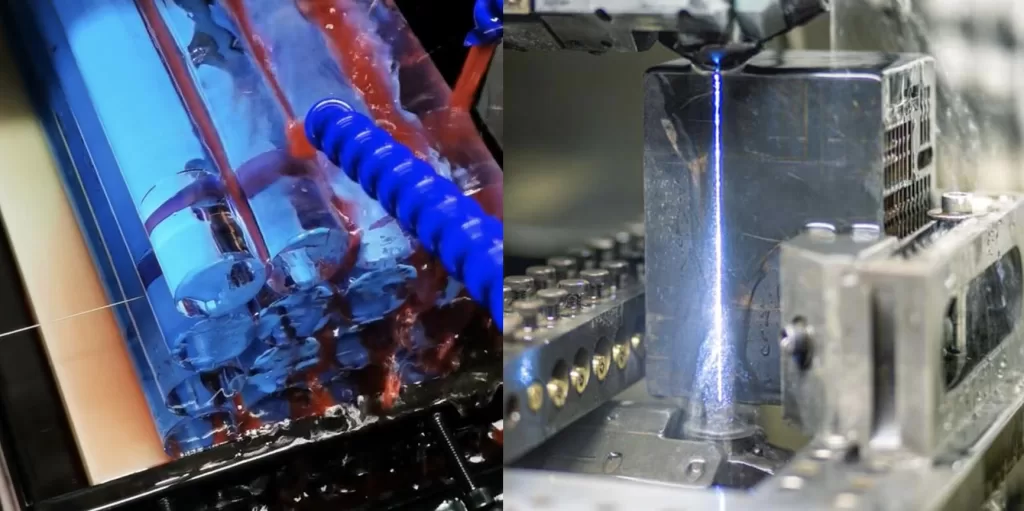
Tabla de contenido
En la fabricación moderna, el corte de materiales es un proceso crucial que influye significativamente en la calidad y el rendimiento del producto final. Dos técnicas de corte de alta precisión ampliamente utilizadas son el corte por hilo de descarga eléctrica (corte por hilo EDM) y el corte por hilo de diamante sin fin. Este artículo profundiza en las diferencias y similitudes entre estos dos métodos de corte, arrojando luz sobre sus respectivas aplicaciones y puntos fuertes.
Corte de hilo por descarga eléctrica: Corte de precisión por erosión de chispa
Empecemos por entender el corte por hilo con descarga eléctrica, una tecnología de corte basada en el principio de la erosión por chispas eléctricas. Emplea un alambre fino como electrodo, utilizando chispas eléctricas entre el alambre y la pieza para eliminar material. El corte por hilo EDM destaca en la fabricación de piezas intrincadas y moldes, gracias a su capacidad para lograr cortes muy precisos, ya sea en metales u otros materiales conductores.
Principales características y ventajas del corte por hilo EDM:
- Alta precisión: El corte por hilo EDM puede alcanzar una precisión micrométrica, lo que lo convierte en la opción ideal para la fabricación de componentes de precisión.
- Formas complejas: Debido a su naturaleza de corte no mecánico, el corte por hilo EDM puede manipular sin esfuerzo geometrías de piezas complejas.
- Poco estrés: En comparación con el corte mecánico tradicional, el corte por hilo EDM impone una tensión mínima a la pieza, lo que reduce el riesgo de deformación.
Limitaciones del corte por hilo EDM:
- Requisito de conductividad: El corte por hilo EDM depende de la conductividad de la pieza, por lo que no es adecuado para cortar materiales no conductores como la cerámica y el vidrio.
- Acabado superficial: Aunque el corte por hilo EDM puede lograr una gran precisión, puede dar lugar a un acabado superficial más rugoso en comparación con otros métodos de corte, lo que requiere un postprocesado adicional.
Corte de hilo diamantado sin fin: Corte innovador de alta eficacia
Centrémonos ahora en Corte de hilo diamantado sin finuna tecnología de corte relativamente nueva que utiliza un hilo incrustado con partículas de diamante para cortar diversos materiales, ya sean conductores o no conductores. Esta innovadora técnica ha encontrado amplias aplicaciones en industrias como la fabricación de semiconductores, la producción de células solares y el procesamiento de vidrio óptico.
Principales características y ventajas del corte con hilo de diamante sin fin:
- Corte multimaterial: El corte con hilo de diamante sin fin puede utilizarse para cortar una amplia gama de materiales, tanto conductores como no conductores, lo que le confiere versatilidad en todos los sectores.
- Alta eficacia: El corte con hilo de diamante sin fin suele ofrecer mayores velocidades de corte en comparación con los métodos tradicionales, lo que aumenta la eficacia de la producción.
- Precisión: La precisión de corte del hilo de diamante es excepcionalmente alta, lo que garantiza la fabricación de componentes de alta calidad.
Comparación entre el corte con hilo de descarga eléctrica y el corte con hilo de diamante sin fin:
- Idoneidad del material: El corte con hilo de descarga eléctrica es adecuado principalmente para materiales conductores, mientras que el corte con hilo de diamante sin fin puede cortar casi cualquier material, independientemente de su conductividad.
- Velocidad de corte: El corte con hilo de diamante sin fin suele tener una mayor velocidad de corte, lo que es crucial para la producción a granel.
- Precisión: Cuando se trata de precisión, el corte por hilo con descarga eléctrica sigue teniendo ventaja, especialmente para la fabricación de piezas complejas.
Conclusión
El corte con hilo de descarga eléctrica y el corte con hilo de diamante sin fin son dos tecnologías de corte que desempeñan un papel fundamental en la fabricación moderna. Ofrecen distintas ventajas y limitaciones en el corte de materiales conductores y no conductores. Los fabricantes suelen elegir el método de corte adecuado en función de sus necesidades específicas. Independientemente del método elegido, ambas técnicas garantizan unos resultados de corte de alta calidad, abordando diversos retos de fabricación.