Palabras clave: Corte de cuarzo, corte circular con hilo de diamante, procesamiento de materiales, innovación tecnológica
En el siempre cambiante panorama de la tecnología, nos encontramos en la cúspide de un apasionante avance en el procesamiento de materiales: el corte circular con hilo de diamante. Esta innovadora tecnología tiene el potencial de revolucionar los procesos de corte de cuarzo y marcar el comienzo de importantes transformaciones en la industria manufacturera.
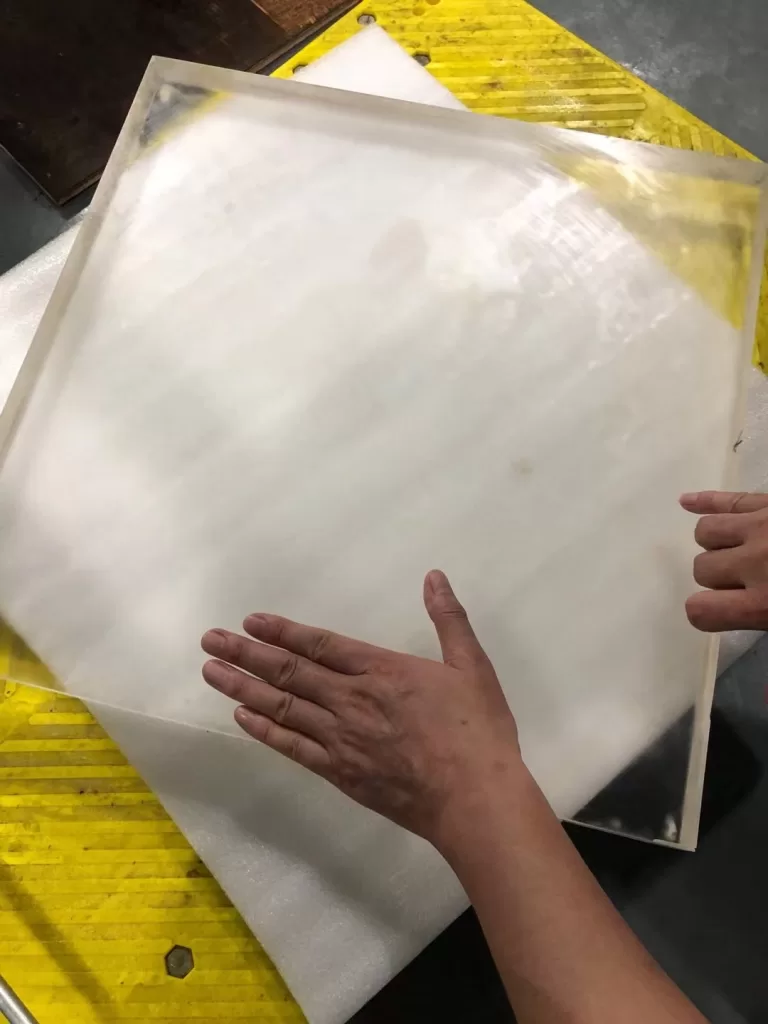
Tabla de contenido
El notable cuarzo
El cuarzo, un material extraordinario conocido por sus extraordinarias características, desempeña un papel fundamental en numerosas industrias. Su gran dureza, excepcional transparencia y resistencia a las altas temperaturas lo convierten en un activo inestimable en aplicaciones que van desde la fabricación de semiconductores hasta la optoelectrónica, las telecomunicaciones y la energía solar. Sin embargo, los métodos de corte tradicionales suelen fallar cuando se enfrentan a materiales de tan alto rendimiento.
Las limitaciones del corte tradicional
Las técnicas de corte tradicionales adolecen de varias limitaciones, sobre todo cortes imprecisos, desperdicio excesivo de material y falta de eficacia. Estos problemas se acentúan aún más cuando se trata de materiales de alto coste y alto rendimiento, como el cuarzo. En consecuencia, la búsqueda de una solución superior ha llevado a científicos e ingenieros a explorar alternativas innovadoras.
La innovación: Corte circular con hilo de diamante
Entre en Tecnología de corte con hilo de diamante circularun cambio de juego en el ámbito de la fabricación. Esta tecnología destaca por su precisión y eficacia. Profundicemos en sus principales ventajas:
Precisión sin igual: El corte con hilo de diamante circular es famoso por su excepcional precisión. Puede crear cortes muy precisos en materiales como el cuarzo, garantizando la producción de componentes de primer nivel.
Mínimo desperdicio de material: Esta tecnología emplea un contorno de alambre fino, lo que reduce drásticamente el desperdicio de material. Este aspecto es especialmente crítico cuando se trabaja con materiales de alto coste y alto rendimiento, ya que ayuda a conservar los recursos y a reducir los costes de producción.
Mayor eficacia: Las máquinas de corte de hilo de diamante circular aumentan significativamente la velocidad de producción, reduciendo eficazmente los ciclos de fabricación. Esto permite ahorrar costes y acelerar los plazos de producción.
Superficies de material sin juntas: Otra ventaja reside en la capacidad de generar superficies excepcionalmente lisas. Esto minimiza la necesidad de un intrincado postprocesado, agilizando el proceso de fabricación y mejorando aún más la rentabilidad.
Aplicaciones en todos los sectores
La versatilidad de la tecnología de corte con hilo de diamante circular va mucho más allá de corte de cuarzoque se aplican a una gran variedad de materiales en diversos sectores. Estos sectores abarcan la optoelectrónica, la fabricación de semiconductores y la producción de células solares, entre otros.
Por ejemplo, en el campo de la optoelectrónica, el corte preciso del cuarzo es indispensable para fabricar componentes ópticos de alta precisión como lentes, prismas y ventanas. Del mismo modo, en la fabricación de semiconductores, el corte preciso del cuarzo es primordial para garantizar la producción de sustratos de dispositivos electrónicos de la máxima calidad. Además, la producción de células solares depende del corte preciso de barras o bloques de cuarzo para crear sustratos, lo que contribuye significativamente a la eficacia y durabilidad de los paneles solares.
Perspectivas de futuro e innovación en el corte del cuarzo
A medida que la tecnología continúa su implacable marcha hacia adelante, podemos anticipar nuevos avances en la tecnología de corte con hilo de diamante circular para satisfacer las necesidades cada vez mayores de la industria manufacturera. Las innovaciones previstas pueden abarcar velocidades de corte aún más altas, mayores niveles de precisión y un espectro más amplio de materiales aptos para este método de corte. Estos avances servirán para mejorar aún más la eficiencia y la sostenibilidad de los procesos de fabricación.
El ángulo de la sostenibilidad
En una era en la que la sostenibilidad es primordial, la tecnología de corte con hilo de diamante circular aporta importantes ventajas. Su reducido desperdicio de material no sólo conserva los recursos, sino que también contribuye a la preservación del medio ambiente. Los cortes de precisión producidos por esta tecnología a menudo anulan la necesidad de procesos de acabado excesivos, reduciendo el consumo de energía y las emisiones. Por consiguiente, la adopción de la tecnología de corte circular con hilo de diamante se alinea con los objetivos más amplios de la fabricación sostenible.
En conclusión
La tecnología de corte con hilo de diamante circular no sólo ha redefinido el procesamiento de materiales, sino que también ha proporcionado un nivel de precisión y eficacia que los métodos tradicionales simplemente no pueden igualar. En un panorama industrial en el que la demanda de materiales de alto rendimiento no deja de aumentar, esta tecnología se erige como un faro de eficiencia y sostenibilidad. A medida que la tecnología siga evolucionando inexorablemente, esta tecnología revolucionaria seguirá estando a la vanguardia, impulsando la innovación y el progreso en la industria manufacturera.