キーワード: 多孔質金属の切断,リング・ダイヤモンド・ワイヤー 切断
目次
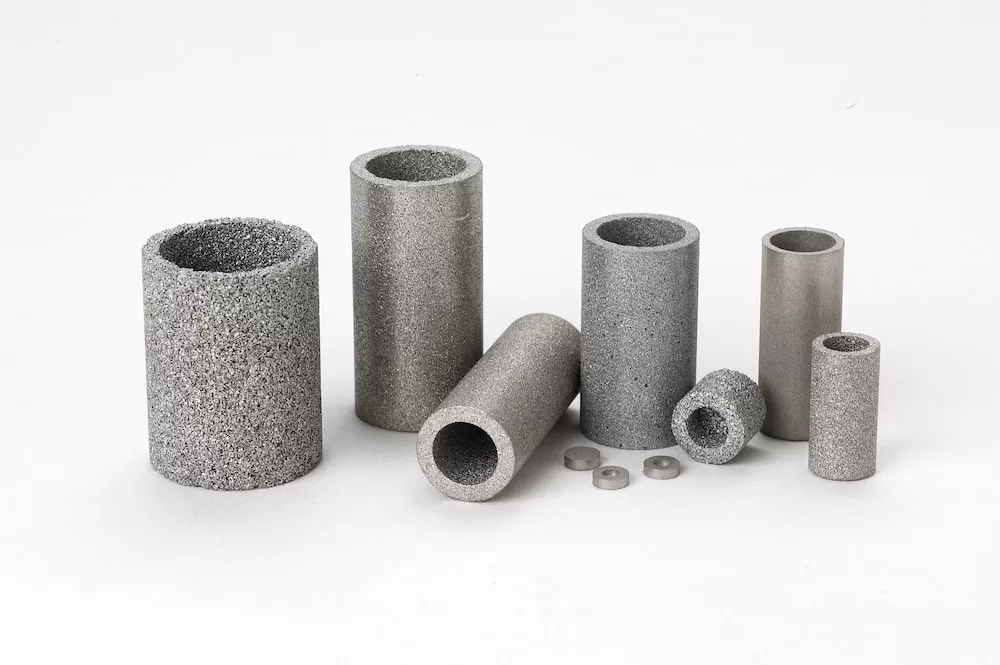
導入
相互接続された空隙を持つ複雑な内部構造を特徴とする多孔質金属は、様々な産業で応用されている。これらの材料は、水素燃料電池のような新たなクリーン・エネルギー技術に不可欠な構成要素である。しかし、多孔質金属の切断は複雑であるため、特定の要件を満たすように切断・成形するには大きな課題があります。従来の切断方法では、多孔質構造を通過するのに苦労し、しばしば損傷や非効率を引き起こす。この記事では、特に水素燃料電池の観点から、こうした課題を解決するためのリングダイヤモンドワイヤー切断の応用を探る。
ポーラス金属とは何か?
ポーラス金属は、その名が示すように、構造内に空隙または細孔を持つ金属である。これらの空隙は、低密度、高表面積、浸透性の向上など、材料にユニークな特性を与えます。これらの特性により、多孔質金属は様々な用途に適している。ポーラス金属は次のような用途に使用される:
- 水素燃料電池 多孔質金属構造は、水素燃料電池の製造に一般的に採用されている。このような燃料電池には、構造的完全性を維持しながら効率的な化学反応を促進できる材料が必要である。多孔質金属は、触媒の堆積と反応物の流れに理想的なフレームワークを提供します。
- ろ過システム: 多孔質金属材料は濾過システムに使用され、その多孔質構造によって気体や液体から汚染物質を効果的に捕捉・除去することができる。
- 熱交換器: 多孔質金属の高い表面積は、熱伝達を促進するため、熱交換器用途に適している。
- バイオメディカル・デバイス 骨インプラントのような一部の生物医学的器具は、天然組織の成長を促進する多孔性金属材料を利用している。
多様な用途があるにもかかわらず、多孔質金属の切断と成形は困難な作業である。
多孔質金属への挑戦 カッティング
ポーラス金属の複雑な構造は、切断や成形に際して独特の難題をもたらす。レーザー切断や研磨法のような従来の切断方法では、以下のような困難が生じる可能性がある:
- 物的損害: 微細な多孔質構造は、切断工程で容易に損傷し、材料の特性や構造的完全性に影響を与える。
- 非効率的なカッティング: 複雑な内部構造は切断工程を遅らせ、非効率、コスト増、生産遅延を招く。
- ダストジェネレーション: 多孔質金属 切削加工では大量の粉塵や廃棄物が発生するため、時間のかかる清掃作業が必要になる。
- 精度の欠如: 多孔質材料の凹凸のため、高精度のカットを実現するのは難しい。
水素燃料電池のように、電極構造が性能を左右する用途では、こうした課題はさらに顕著になる。そこで、リングダイヤモンドワイヤー切断が活躍するのです。
リングダイヤモンドワイヤー切断:精度と効率
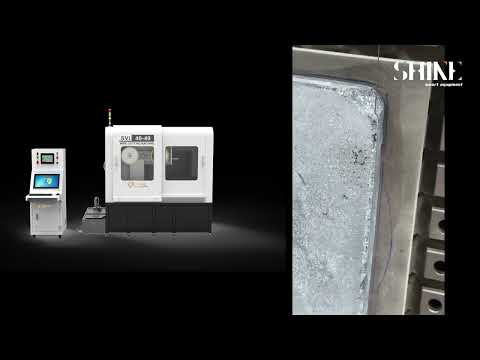
リングダイヤモンドワイヤーカッティングは、次のような課題を解決します。 多孔質金属の切断.この方法はクローズド・ループ・システムを中心に展開され、細いダイヤモンド・ワイヤーがクローズド・ループに形成される。このワイヤーは驚異的なスピードで回転し、毎秒80メートル以上に達する。この高速回転の結果、非常に鋭利なダイヤモンド粒子が生まれ、さまざまな素材を素早く切断することができる。
さらに、リングダイヤモンドワイヤーの方向性のある動きにより、従来の切断方法で一般的な問題であった頻繁な工具交換が不要になります。これにより、作業効率が向上するだけでなく、切断面を滑らかでバリのない状態に保つことができます。
環境への影響と持続可能性の点で、リングダイヤモンドワイヤー切断は際立っています。廃棄物や粉塵の発生を最小限に抑えることができるため、従来の方法と比べて環境に優しい選択肢となります。粉塵の低減は、水素燃料電池のような繊細な用途で特に有利です。
イノベーションと将来展望
リングダイヤモンドワイヤーカッティングは、様々なカッティングニーズに対応するために進化し続けています。厚みや孔の大きさが異なる多孔質金属の切断など、さまざまな材料を扱うことができるため、汎用性の高いソリューションとして位置づけられています。継続的な技術の進歩は、精度、スピード、総合的な切断効率の向上を目指しています。
水素燃料電池のようなクリーンエネルギー技術の需要が高まり続ける中、切断方法の革新はますます不可欠になっています。リングダイヤモンドワイヤー切断の可能性は、これらの技術の主要部品の生産に革命をもたらし、持続可能で環境に優しい未来へのエキサイティングな可能性を提供します。
結論
リングダイヤモンドワイヤカッティングは、水素燃料電池から多様な産業用途に至るまで、多孔質金属切断の常識を変えるソリューションです。その精度、効率、環境への影響の少なさ、適応性から、クリーンエネルギー生産において重要な役割を担っています。技術が進歩し続ける中、リングダイヤモンドワイヤー切断の見通しは依然として明るく、多孔質金属の切断・加工方法をさらに改善することが期待されています。