Table of Contents
Introduction
In the world of optoelectronics cutting, the precision and quality of material cutting play a pivotal role in shaping the components that power devices such as lasers, optical sensors, and photovoltaic cells. Traditional cutting methods often faced limitations in achieving the level of precision required for these delicate materials.
In this article, we will explore the materials commonly cut in the optoelectronics industry, delve into the historical cutting methods employed, and examine how Ring Diamond Wire Cutting is revolutionizing this sector.
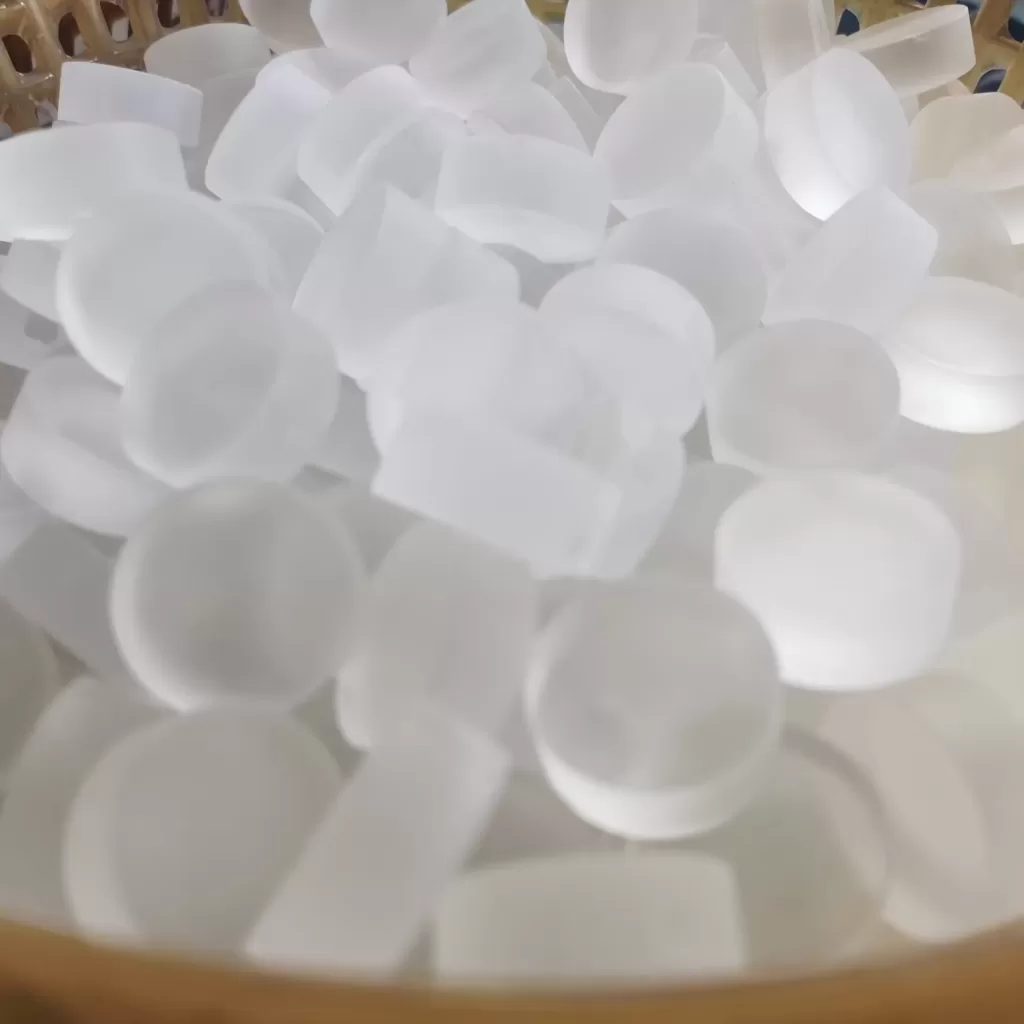
Materials in Optoelectronics Cutting
The optoelectronics industry encompasses a wide range of materials that require precise cutting:
- Crystals: Various crystals, including silicon, sapphire, and gallium arsenide, serve as the foundation for many optoelectronic devices.
- Glass: Precision cutting of glass materials is essential for creating optical lenses, prisms, and windows used in lasers and sensors.
- Semiconductor Wafers: Silicon and compound semiconductor wafers are sliced into thin, uniform pieces for manufacturing microelectronic and optoelectronic components.
Historical Cutting Methods
In the past, optoelectronics manufacturers primarily relied on traditional cutting methods:
- Sawing: Mechanical sawing using abrasive blades was a common method. However, it often resulted in rough edges, material loss, and limitations in achieving ultra-thin cuts.
- Laser Cutting: While more precise than mechanical sawing, laser cutting had limitations in terms of material compatibility and the potential for heat-affected zones.
Ring Diamond Wire Cutting: A Game-Changer
Ring Diamond Wire Cutting Machines have emerged as a transformative technology in the optoelectronics industry. Here’s how they are making a significant impact:
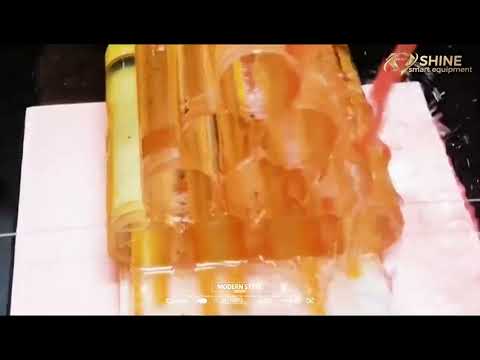
Material Versatility:
Ring Diamond Wire Cutting is highly versatile, capable of cutting a wide range of materials, including crystals, glass, and semiconductor wafers.
Precision Cuts:
These machines deliver exceptional precision, ensuring that the cut materials meet the stringent requirements of optoelectronic components.
Reduced Material Loss:
The thin, continuous wire minimizes material wastage, making the process cost-effective.
Smooth Edges:
Ring Diamond Wire Cutting produces clean and smooth edges, reducing the need for extensive post-processing.
Replacing Traditional Cutting Methods
Ring Diamond Wire Cutting has the potential to replace traditional cutting methods in several ways:
- Sawing: Mechanical sawing methods are gradually being replaced by Ring Diamond Wire Cutting for crystal and semiconductor wafer cutting due to the latter’s precision and efficiency.
- Laser Cutting: While laser cutting remains relevant for certain materials, Ring Diamond Wire Cutting is becoming the preferred choice for its versatility and material preservation.
Enhancing Optoelectronics Manufacturing with Ring Diamond Wire Cutting
Ring Diamond Wire Cutting represents a profound advancement in optoelectronics manufacturing, and its potential applications are expanding. Here, we delve deeper into how this cutting-edge technology is enhancing the optoelectronics cutting industry.
Applications Beyond Crystal Cutting
While Ring Diamond Wire Cutting initially gained prominence in the precise cutting of crystals, its applications have evolved to encompass a broader spectrum of materials in the optoelectronics realm. These applications include:
- Glass Components: The optoelectronics cutting industry relies heavily on precision glass components, such as optical lenses and windows. Ring Diamond Wire Cutting’s ability to create smooth and precise cuts in glass materials is invaluable in ensuring the optical quality of these components.
- Semiconductor Manufacturing: Silicon and compound semiconductor wafers are the heart of microelectronic and optoelectronic devices. Ring Diamond Wire Cutting’s capacity for ultra-thin, precise cuts ensures the creation of high-performance semiconductor components.
- Photovoltaic Cells: Solar energy, a critical component of sustainable power generation, relies on precise cutting of silicon wafers for photovoltaic cells. Ring Diamond Wire Cutting enables the production of solar panels with optimal energy conversion efficiency.
- LED Production: Light-emitting diodes (LEDs) are integral to displays, lighting, and optical sensors. The precision and material preservation offered by Ring Diamond Wire Cutting are essential for manufacturing high-quality LED components.
Advancing Research and Development
The impact of Ring Diamond Wire Cutting extends beyond manufacturing. In research and development (R&D) laboratories, scientists and engineers utilize this technology to create prototypes and conduct experiments. Its precision and versatility provide the ideal platform for developing cutting-edge optoelectronic devices, pushing the boundaries of innovation in the field.
Environmental Sustainability
In an era where sustainability is a global concern, Ring Diamond Wire Cutting aligns with eco-friendly practices. The reduced material wastage and minimized need for additional processing contribute to lower resource consumption and reduced environmental impact. This is particularly significant in industries like optoelectronics, where precision and efficiency must be balanced with sustainability.
Conclusion
Ring Diamond Wire Cutting is transforming the optoelectronics cutting industry by providing a versatile, precise, and efficient method for processing a wide range of materials. Its impact is felt across the sector, from crystal cutting to semiconductor wafer slicing. As technology advances, Ring Diamond Wire Cutting is poised to play an increasingly central role in shaping the components that drive innovation in the optoelectronics cutting field.