Keywords: ultrasonic cutting, ring diamond wire cutting, precision cutting technologies, material processing
Оглавление
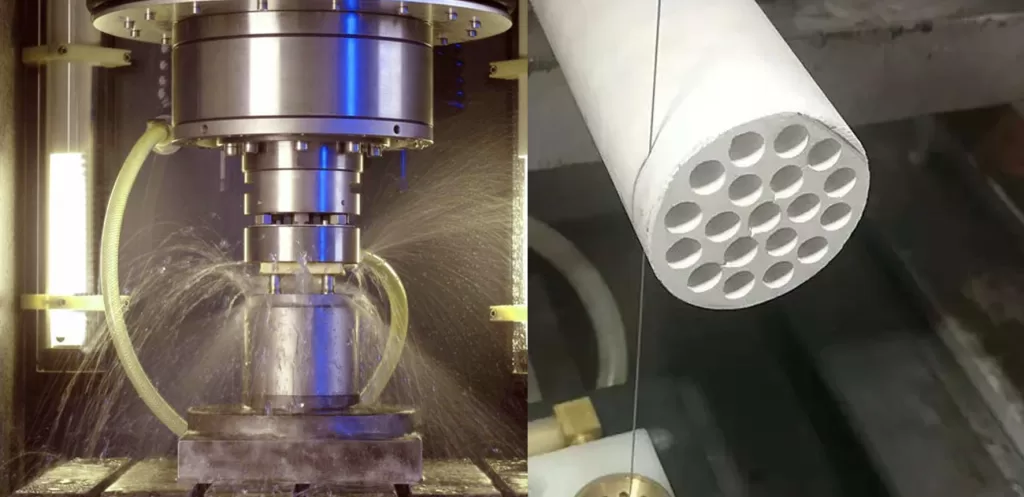
In the realm of advanced manufacturing, precision machining technologies have revolutionized the way we create intricate parts and components. Two such technologies, Electrochemical Machining (ECM) and Closed Diamond Wire Cutting, stand at the forefront of this innovation. In this article, we delve into the fundamentals of ECM, explore the intricacies of closed diamond wire cutting, discuss their respective applications, and draw distinctions between these cutting-edge techniques.
Electrochemical Machining (ECM): An Overview
ECM, an acronym for Electrochemical Machining, is an exceptional subtractive manufacturing process. It relies on controlled electrochemical reactions to remove material from a workpiece, resulting in highly precise, intricate shapes. Here’s how ECM works:
A workpiece (typically the anode) and a tool (the cathode) are immersed in an electrolyte solution. When an electric current is applied, metal ions are removed from the workpiece. This method permits ECM to craft complex geometries with micron-level precision.
Applications of ECM
ECM has proven its utility in several industries, including aerospace, medical device manufacturing, and precision tool production. It is particularly adept at creating components with intricate internal structures, such as turbine blades and fuel injector nozzles.
Electrochemical Machining (ECM) Преимущества
ECM offers several advantages, including:
- Высокая точность: ECM typically provides machining precision at the micron level, making it suitable for manufacturing parts that require a high degree of accuracy.
- Сложные геометрии: It can produce a wide range of complex shapes, including internal cavities, small holes, and intricate structures.
- No Thermal Impact: As a non-contact machining method, ECM does not induce heat-related deformations or stress, maintaining the structural integrity of the workpiece.
- Applicable to Various Materials: ECM is compatible with most conductive materials, including metals and alloys.
Electrochemical Machining (ECM) Недостатки
However, ECM has some drawbacks, such as:
- Relatively Slow Speed: ECM is generally slower compared to other machining methods, making it unsuitable for large-scale production.
- Specialized Knowledge Requirement: ECM demands highly specialized expertise for operation and monitoring, including the selection of the appropriate electrolyte and current density.
- Wastewater Treatment: The wastewater may contain hazardous substances, necessitating treatment and disposal, which increases costs and poses environmental challenges.
Closed Diamond Wire Cutting: An Introduction
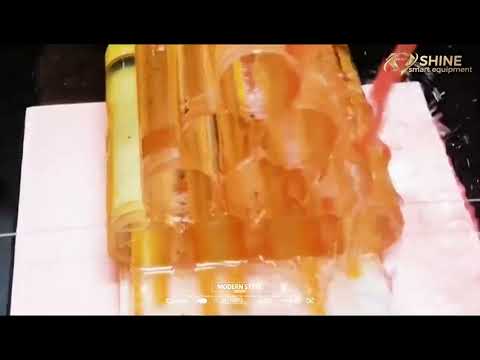
Closed алмазная резка проволоки is a novel technique that leverages a wire with embedded fine diamond particles to cut through a variety of materials. This process excels at producing smooth, straight cuts with minimal waste, thanks to the extreme hardness of diamond abrasive.
Applications of Closed Diamond Wire Cutting
Closed diamond wire cutting has found applications across a broad spectrum of industries, from semiconductor manufacturing to solar panel production. It is particularly beneficial when precise, clean cuts are required in materials like silicon wafers and оптическое стекло.
Comparing ECM and Closed Diamond Wire Cutting
While both ECM and closed diamond wire cutting are advanced machining methods, they differ in key aspects:
- Principle of Material Removal:
- ECM relies on electrochemical reactions to dissolve material.
- Закрытая алмазная проволока cutting uses abrasion from embedded diamond particles.
- Точность:
- ECM is renowned for its exceptional precision, often at the micron level.
- Closed diamond wire cutting provides high accuracy, though not typically at the same micron-level precision as ECM.
- Materials Processed:
- ECM is mainly used for conductive materials.
- Closed diamond wire cutting can process both conductive and non-conductive materials.
- Приложения:
- ECM is suitable for crafting intricate internal structures and specialized components.
- Closed diamond wire cutting is preferred for applications demanding clean, straight cuts in materials like silicon and glass.
In conclusion, ECM and closed diamond wire cutting represent two advanced approaches to precision machining. ECM, with its electrochemical magic, excels at crafting complex internal geometries, while closed diamond wire cutting is the go-to choice for clean, efficient cuts in a wide range of materials. Understanding their distinctions allows manufacturers to select the optimal technique for their specific application, ensuring the highest quality and precision in their output.