Оглавление
Introduction:
Endless diamond wire saws are indispensable tools in the semiconductor manufacturing industry. This article explores the significant role of endless diamond wire saws in various aspects of semiconductor production, including silicon ingot cropping, silicon top tail cut, and other critical processes,such as sapphire and silicon carbide cutting which are used in a variety of applications.
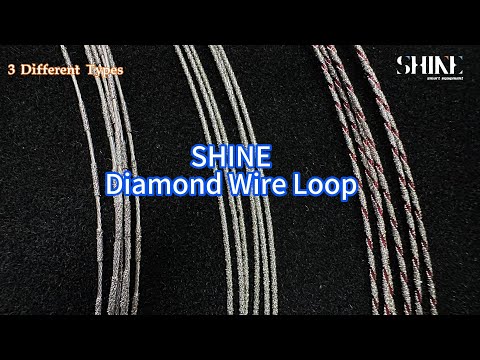
Silicon Top & Tail Cut:
What is silicon top-tail cut?
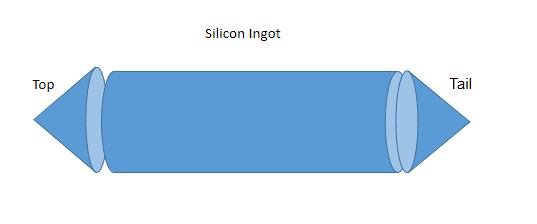
After a silicon ingot is grown, it looks like a long, cylindrical rod. The ingot is typically about 10 to 12 inches in diameter and 12 to 18 inches long. The ingot is made of pure silicon and it is very hard and brittle. The ingot is used to make semiconductor wafers, which are the foundation of all semiconductor devices.
In semiconductor manufacturing, a silicon top-tail cut is a type of cut made to the top and bottom of a silicon ingot,it’s also called silicon ingot cropping. This cut is made to remove the damaged or contaminated regions of the ingot, which can improve the quality of the wafers that are produced from the ingot.slicing wafering cutting cropping
Some of the challenges in silicon top-tail cut:
- The silicon ingot is a very hard material. This makes it difficult to cut through the ingot without damaging it.
- The silicon ingot is a very brittle material. This makes it easy for the ingot to crack during the cutting process.
- The silicon ingot is a very expensive material. This makes it important to minimize the amount of waste material produced during the cutting process.
The challenges of silicon top-tail cut are overcome by using a variety of techniques, including:
- Water cooling: The ingot is cooled with water to prevent it from overheating.
- Saw type: Endless diamond wire saw can carefully prevent the ingot from cracking.since the diamond cutting wire loop is very thin compare to diamond band. the flexible cutting method made it largely reduced the edge break.
Silicon Ingot bridge cutting :
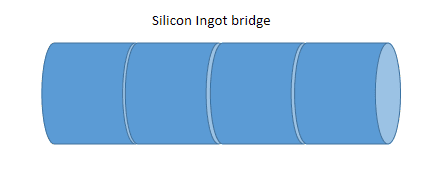
After top-tail cut/silicon cropping , silicon ingot bridge cutting is a process used to remove the central portion of a silicon ingot, leaving two cylindrical sections that can be sliced into semiconductor wafers. The bridge is removed because it is typically of lower quality than the rest of the ingot, due to impurities and defects that can form during the growth process.wafering cutting cropping and bricking
The bridge cutting process is typically carried out using a diamond wire saw, which is a thin wire coated with diamond particles. The wire saw is fed through the ingot at a very slow speed, and the bridge is removed by a series of cuts. The saw is also cooled with water to prevent it from overheating.
The bridge cutting process is a critical step in the production of semiconductor wafers. By removing the bridge, semiconductor manufacturers can ensure that the wafers they produce are of the highest quality.
Advantages of endless diamond wire loop saw in bridge cutting:
- High precision: Endless diamond wire loop saws can cut with high precision, resulting in smooth and burr-free cuts. This is important in bridge cutting, as any defects in the cut can weaken the wafers and lead to failures.
- High speed: Endless diamond wire saws can cut at high speeds comparing to conventional diamond wire on spool, which can help to improve productivity. This is important in the semiconductor industry, where demand for wafers is high.
- Long service life: Endless diamond wire loop saws have a long service life, which can help to reduce costs. This is important in the semiconductor industry, where the cost of manufacturing wafers is high.
- Less kerf loss : Endless diamond wire loop can minimize the amount of waste material produced during the cutting process.It’s cutting kerf is 0.45 MM.diamond wire of mm dia
Other Semiconductor Manufacturing Applications
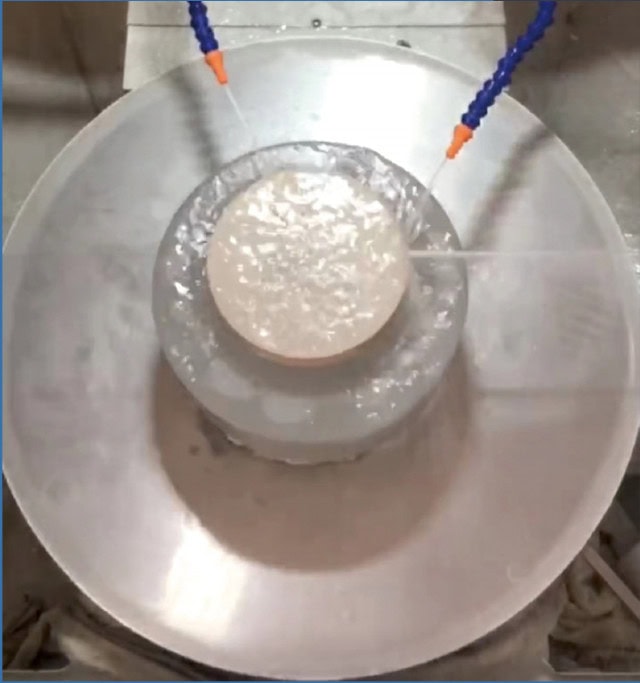
Endless diamond wire saws find additional applications in semiconductor manufacturing. They are used to cut materials like sapphire, silicon carbide, and gallium nitride, which are crucial for the production of LEDs, power electronics, and other advanced semiconductor devices. The saws enable precise shaping and cutting of these materials, ensuring optimal performance and reliability of the final products.
Furthermore, endless diamond wire saws assist in the singulation of packaged semiconductor devices, separating individual chips from a wafer or substrate. This process is crucial for packaging and assembly, allowing for efficient production of integrated circuits and electronic components.
Conclusion :
Endless diamond wire saws are key tools in semiconductor manufacturing, playing a crucial role in silicon ingot cropping, wafer slicing, and other important processes. Their precise cutting capabilities, minimal material loss, and ability to work with various semiconductor materials make them indispensable for producing high-quality wafers and semiconductor devices. The continuous advancement of endless diamond wire saw technology will drive innovation and progress in the semiconductor industry.