Introduction
Ring-shaped diamond wire cutting equipment represents a significant advancement over traditional cutting methods. Unlike conventional wire saws, which often use long, open-loop wires, ring-shaped diamond wire saws employ a continuous, closed-loop wire that offers several advantages. These include faster cutting speeds, superior surface finish with minimal wire marks, and enhanced precision in cutting various hard materials such as graphite, silicon, and optical glass. This article will delve into the mechanics of diamond wire cutting, optimal tension settings, recommended cutting parameters for different materials, and practical tips for achieving the best performance from your equipment.
Understanding Cutting Mechanics
When using ring-shaped diamond wire cutting equipment, the cutting wire must exert a force on the workpiece to achieve an effective cut. This force causes the flexible wire to bend, creating a “wire arc.” The presence of this arc is essential because it indicates that the wire is applying the necessary cutting force. If the wire remains perfectly straight, it suggests that no cutting force is being applied to the workpiece, resulting in ineffective cutting.
The normal cutting state involves the wire forming a controlled arc that exerts a consistent pulling force on the workpiece until the cut is complete. As cutting progresses, the wire arc adjusts dynamically, maintaining optimal pressure and ensuring a smooth cut. At the moment the cutting is finished, a noticeable distance, typically around 2 to 3 cm, appears between the wire and the workpiece, signaling the sudden disappearance of the wire arc. This is a key indicator that the cut is complete and that the equipment has functioned correctly.

Figure 1: Illustration of the Cutting Mechanics and Wire Arc Formation.
Optimal Tension Settings for Efficient Cutting
The tension of the cutting wire is a critical factor that directly influences both the speed and quality of the cut. Two clear signs indicate when the tension is too low:
- Wire Oscillation During Idle Runs: If the cutting wire oscillates up and down when the machine is idling, it suggests that the tension is insufficient. Under normal conditions, the wire should remain stable and its movement should be imperceptible when the machine is not actively cutting.
- Increasing Wire Arc with Higher Cutting Speeds: When the cutting speed is increased, and the cutting wire does not move forward quickly but instead forms a larger arc, this is a clear sign that the tension is too low (except when cutting extremely hard materials). Adequate tension helps maintain wire stability, preventing excessive arc formation and ensuring a consistent cutting path.
A well-tensioned wire not only improves cutting speed but also enhances the quality of the cut surface, resulting in fewer defects and a smoother finish. The cutting wire used in ring-shaped diamond wire cutting equipment is designed to withstand tensions between 220 and 350 N, which is sufficient to prevent breakage under normal operating conditions. It is important to note that a slight arc of 2-3 mm during cutting is normal and indicates that the wire is applying the correct cutting force.

Figure 2: Effects of Wire Tension on Cutting Speed and Surface Quality.
Recommended Cutting Parameters for Graphite
Graphite, being a relatively hard and brittle material, requires specific cutting parameters to achieve optimal results. Based on our experience, the following settings are recommended:
- Wire Speed: 1800 to 2000 rpm
- Скорость резки: 50 to 100 mm/min
Operators are encouraged to experiment with these parameters, starting with a lower wire speed of 1500 rpm and gradually increasing to 2000 rpm. Simultaneously, the cutting speed can be adjusted to find the best balance between speed and surface quality. The goal is to achieve a clean, smooth cut with minimal defects.
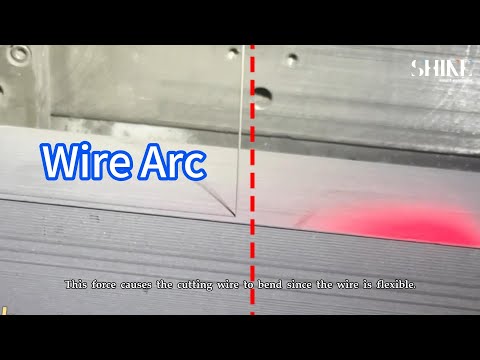
Figure 3: Recommended Wire and Cutting Speeds for Graphite.
Practical Tips for Operators
To maximize the performance of ring-shaped diamond wire cutting equipment, consider the following tips:
- Maintain Proper Tension: Regularly check and adjust the wire tension to ensure it is within the recommended range of 220-350 N. This helps prevent wire breakage and maintains cutting efficiency.
- Monitor Wire Arc: A consistent wire arc of 2-3 mm during cutting is normal. If the arc becomes too large, consider increasing the tension or reducing the cutting speed.
- Experiment with Parameters: Especially during the initial setup, experiment with different wire speeds and tensions to find the optimal settings for your specific application. This can help identify the best balance between speed, quality, and wire life.
Заключение
In summary, achieving optimal performance with ring-shaped diamond wire cutting equipment involves understanding the mechanics of the cutting process, maintaining proper tension, and setting appropriate cutting parameters for different materials. By carefully monitoring the wire arc, adjusting tension as needed, and experimenting with different settings, operators can achieve high-quality cuts with minimal defects and maximum efficiency. We encourage operators to make bold adjustments during the initial setup phase to find the optimal configuration for their specific needs.