Оглавление
Введение
Circular diamond wire is a critical component in various industrial applications, particularly in the cutting and slicing of hard and brittle materials like silicon wafers, glass, and ceramics. The precise control of tension in circular diamond wire plays a pivotal role in enhancing cutting accuracy, improving tool life, and reducing material wastage. In this article, we will explore the recent advancements in circular diamond wire tension control systems.
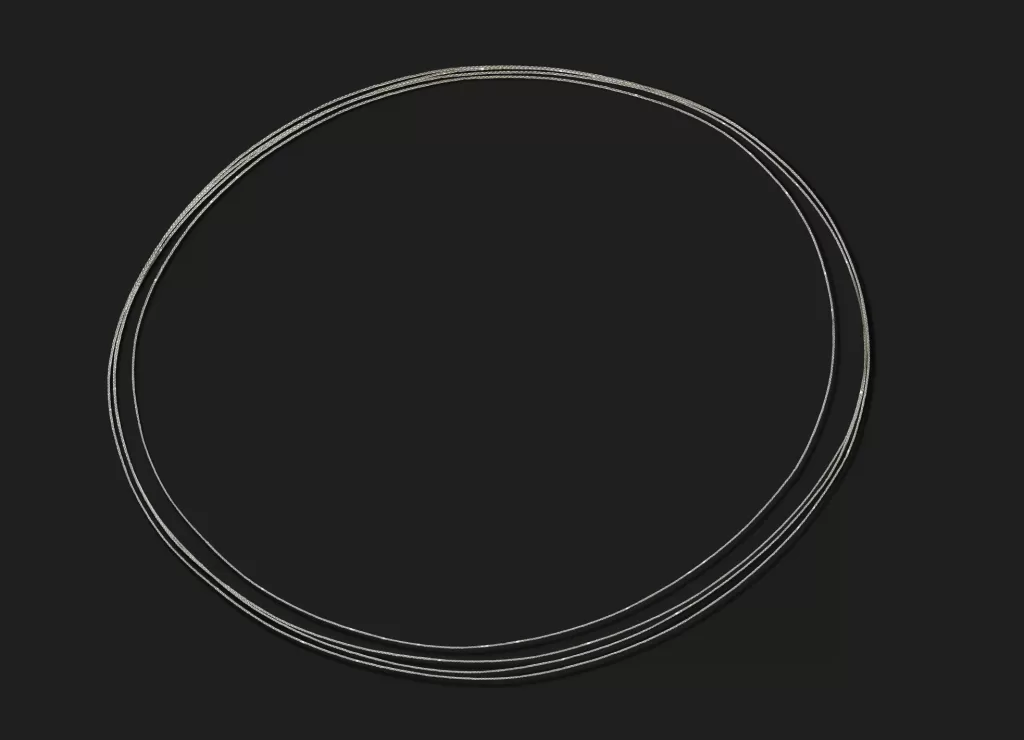
The Importance of Tension Control
Tension control is crucial in circular diamond wire cutting for several reasons:
- Cutting Precision: Maintaining consistent wire tension ensures precise cuts, reducing the likelihood of chipping or material damage.
- Tool Longevity: Proper tension control prolongs the life of the diamond wire, minimizing downtime and replacement costs.
- Material Efficiency: Accurate tension control reduces material wastage, which is particularly vital when working with expensive or limited resources.
- Process Stability: Stable tension contributes to smoother cutting operations and fewer interruptions.
Advancements in Circular Diamond Wire Tension Control
1. Real-time Monitoring and Feedback
One of the significant advancements in tension control systems is the integration of real-time monitoring and feedback mechanisms. These systems utilize sensors to continuously measure tension levels and make automatic adjustments. If the tension deviates from the preset parameters, the system can instantly make corrections, maintaining consistent wire tension throughout the cutting process.
2. Adaptive Control Algorithms
Modern tension control systems incorporate adaptive control algorithms that can adapt to changing cutting conditions. These algorithms consider factors such as wire wear, temperature fluctuations, and material variations, allowing for dynamic adjustments to maintain optimal tension levels.
3. Wireless Connectivity
Wireless technology has revolutionized tension control systems by enabling remote monitoring and control. Operators can now monitor tension levels, receive alerts, and make adjustments from a remote location, improving convenience and operational efficiency.
4. Improved Wire Materials
Advancements in the materials used for circular diamond wire have also contributed to better tension control. High-quality wires with enhanced durability and wear resistance lead to more stable tension levels over extended periods of use.
5. Data Analytics and Predictive Maintenance
The integration of data analytics and predictive maintenance techniques allows operators to analyze historical tension data. By identifying patterns and trends, maintenance schedules can be optimized, reducing downtime and ensuring peak performance.
6. Enhanced User Interfaces
User-friendly interfaces have made tension control systems more accessible to operators. These interfaces provide intuitive controls and real-time visualizations of tension levels, making it easier for operators to make informed decisions.
Applications and Benefits
These advancements in circular diamond wire tension control systems have found applications in various industries:
- Semiconductor Manufacturing: Improved tension control is critical for the precision cutting of silicon wafers used in semiconductor fabrication.
- Photovoltaics: Solar cell production relies on accurate cutting of silicon ingots, where tension control systems help optimize material usage.
- Glass and Ceramics: Tension control ensures clean and precise cuts in the production of glass panels and ceramic tiles.
- Aerospace: Circular diamond wire is used in the aerospace industry for cutting and shaping composite materials, where tension control enhances safety and accuracy.
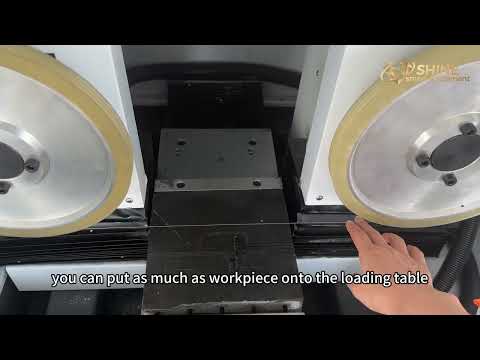
Заключение
The development of circular diamond wire tension control systems has significantly improved the efficiency, precision, and reliability of cutting processes across various industries. These advancements, ranging from real-time monitoring to adaptive control algorithms, have paved the way for more sustainable and cost-effective operations. As technology continues to evolve, we can expect further innovations that will continue to push the boundaries of what is achievable with circular diamond wire cutting.
In conclusion, the progress in circular diamond wire tension control systems is an ongoing journey driven by technological innovation and the pursuit of higher cutting precision, reduced waste, and increased productivity across diverse industries. As these systems continue to evolve, they will play an increasingly pivotal role in shaping the future of material processing and manufacturing.