Home / Products / Diamond Wire Cutting Machine / SGOM 30
SGOM 30
A Breakthrough in Semiconductor Wafer Cutting
The SGOM 30 is a cutting-edge multi-wire diamond cutting machine tailored for semiconductor silicon wafer slicing. Utilizing a continuous 30-kilometer diamond wire, this equipment delivers unmatched precision, efficiency, and environmental benefits, making it an ideal choice for high-demand wafer processing.
Product Highlights
- Designed for Silicon Wafer Slicing: Precision-engineered to meet the stringent requirements of semiconductor manufacturing.
- Continuous Diamond Wire: Ensures uninterrupted and precise multi-slice cutting.
- Eco-Friendly Solution: Eliminates the waste and environmental hazards associated with slurry-based cutting.
- High Productivity: Multi-wire design enhances throughput for mass production.
- Surface Quality Excellence: Swinging motion ensures smooth surfaces, reducing the need for post-processing.
MULTI WIRE SAW SGOM30 TECHNICAL SPECIFICATION
Specification | Details |
Power Supply | Three-phase AC 380V, 50 Hz |
Rated Input Power | 68 kW |
Machine Weight | Approx. 7 tons |
Machine Dimensions | 2800 × 2000 × 2800 mm |
Processing Area | 300 × 300 × 490 mm |
Roller Specifications | φ180 ± 10 × 490 mm |
Diamond Wire Diameter | 0.18–0.37 mm |
Wire Storage Capacity | 30,000 m |
Max Wire Speed | 1800 m/h |
Cutting Feed Rate | 0–60 mm/h |
Max Reciprocation | 12 cycles/h |
Detailed Product Introduction
This model is specifically designed to meet customer needs for cutting efficiency and cost reduction. With a roller length of 490 mm and a maximum loading area of 300 mm × 300 mm × 490 mm, it is capable of cutting products with a thickness range of 0.5 mm to 12 mm.
SGOM 30 Four-Axis Multi-Wire Cutting Machine Features
One-Piece Casting for High Stability
The machine body is cast as a single piece and processed in one go, minimizing assembly-related cumulative errors. This ensures high-speed, stable operation and guarantees cutting quality.Independent Drive for Four Rollers
Each roller is independently driven by its own motor, making all rollers active. This reduces wire wear on the rollers, extending their lifespan. The roller bracket mounting holes are precision-machined in one step to ensure the required coaxial alignment of the main shaft.Swing Function for Surface Quality
The machine features a swinging function that improves surface smoothness during cutting, enhancing processing efficiency.Ergonomic and Compact Design
With a height of just 2700 mm, the machine is designed for ease of operation and safety, offering an efficient and user-friendly experience.Top-Positioned Worktable
Materials are fed from below and lifted upward for cutting, making loading and unloading convenient.Large Loading Area
A maximum loading area of 300 mm × 300 mm × 490 mm significantly improves cutting capacity and productivity.Double-Conical Roller Positioning
The rollers utilize double-conical positioning, ensuring stable and reliable high-speed operation with excellent precision.High Precision and Dust-Proof Design
The main shaft precision is ≤0.01 mm, featuring a dust-proof structure (patent number ZL201320681902.7) for stable operation and easy disassembly.Convenient Operation
The machine includes an automatic lifting shield, and the fully open worktable design facilitates material handling and roller replacement.High Efficiency and Low Power Consumption
The machine does not require an air source, and the total power consumption is limited to 25 kW, making it energy-efficient and cost-effective.
This design ensures that the SGOM 30 delivers exceptional performance, reliability, and ease of use for a variety of cutting applications.
Product Video: How the multi wire saw looks
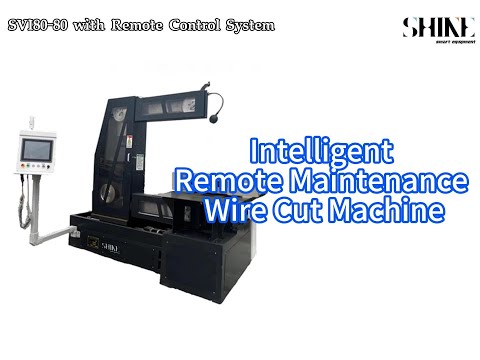
Click To Watch More Videos Showing Our Cutting Machine In Action.
Comparison: SGOM 30 vs. Slurry-Based Wire Cutting
Feature | SGOM 30 (Diamond Wire) | Slurry-Based Wire Cutting |
---|---|---|
Environmental Impact | Eco-friendly, no slurry waste | Generates significant slurry waste |
Cutting Efficiency | same | same |
Material Loss | Minimal kerf loss | Higher material wastage |
Surface Quality | There are wire marks sometimes | Excellent, minimal roughness |
Maintenance Costs | Lower maintenance needs | High maintenance due to slurry and wear |
Operational Costs | Reduced energy and consumables | Higher due to slurry consumption |
THE CUT EFFECT


CUTTING APPLICATIONS
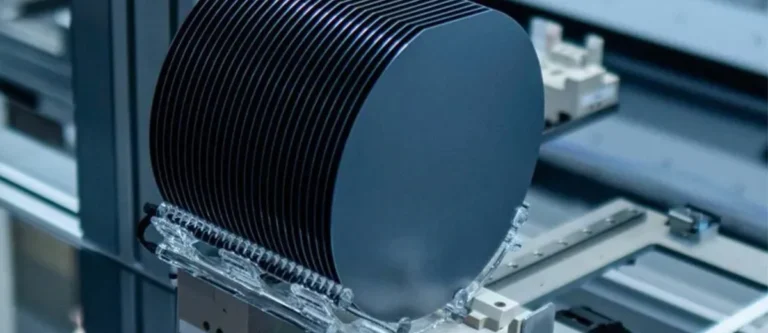
Semiconductor Wafer Cutting
Efficiently slices silicon wafers for semiconductor devices.
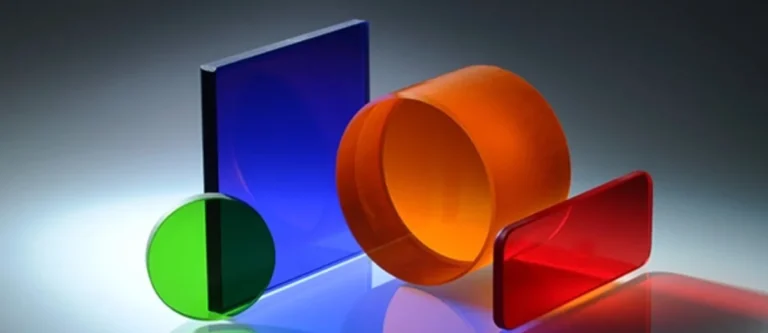
Optoelectronics
Ideal for slicing optical materials like quartz and sapphire.
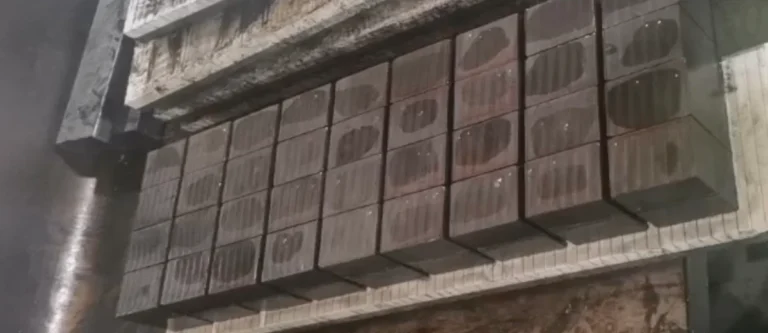
Magnetic Material Processing
Efficiently slices magnetic materials used in industrial and electronic applications.

Alumina Ceramics Cutting
Processes alumina ceramic components with tight tolerances and smooth finishes.
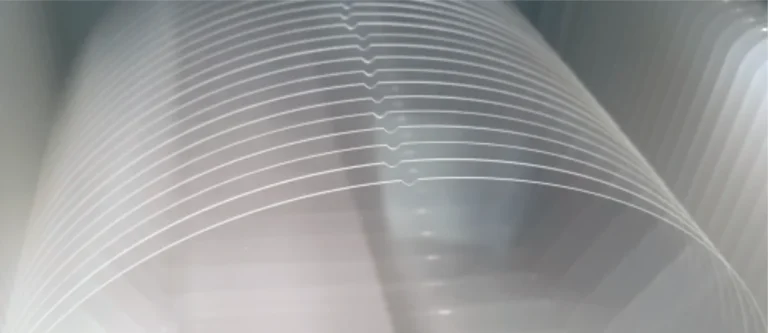
Sapphire wafer cutting
Precisely cuts sapphire, ensuring minimal material loss and high-quality surface finishes.
OUR ADVANTAGE
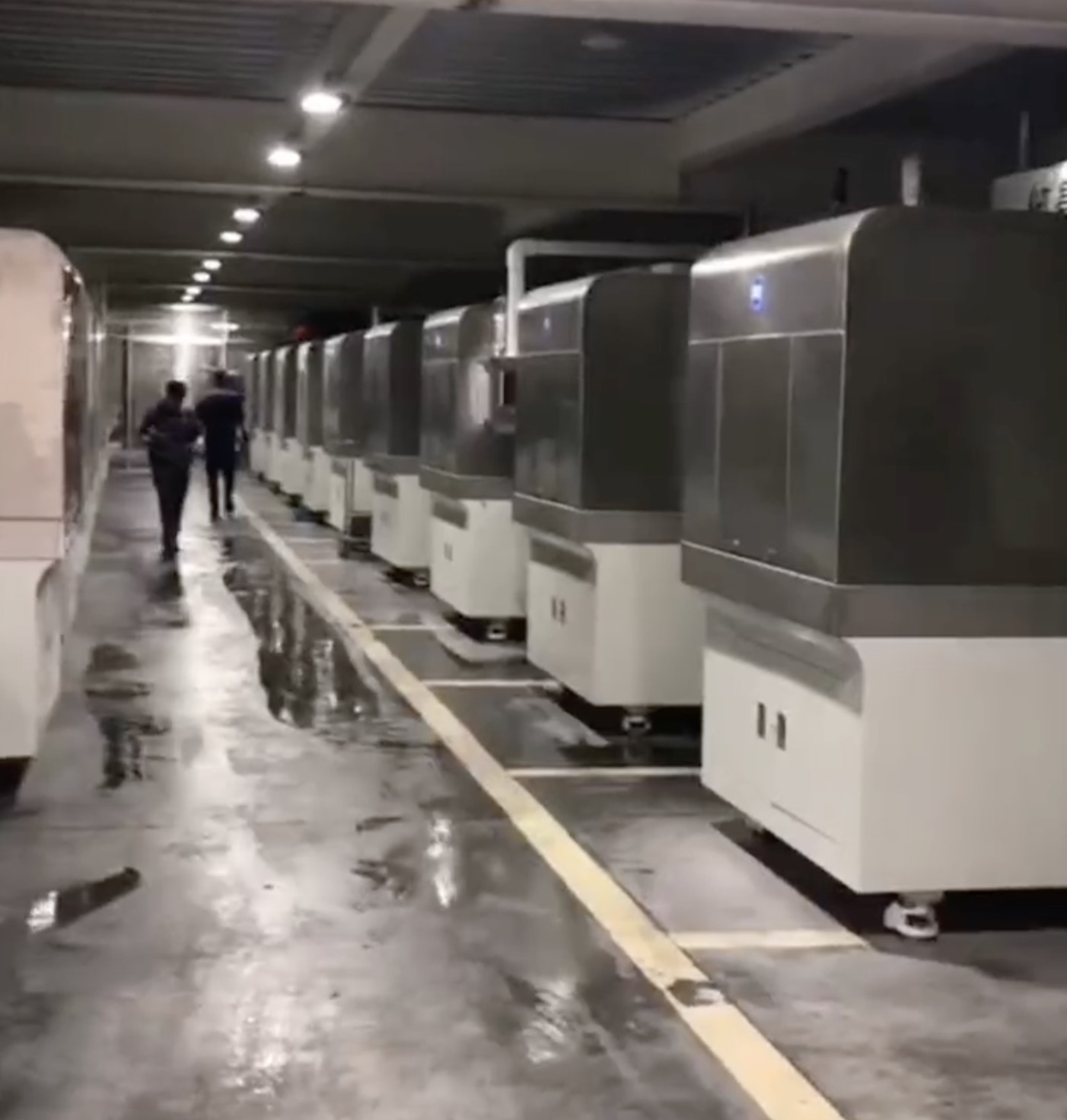
Comprehensive Support
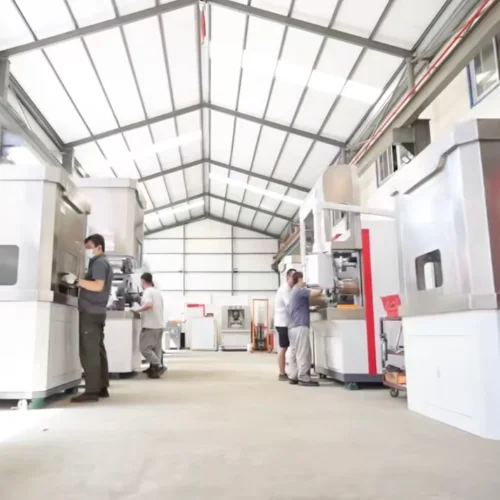
24 Years of Expertise
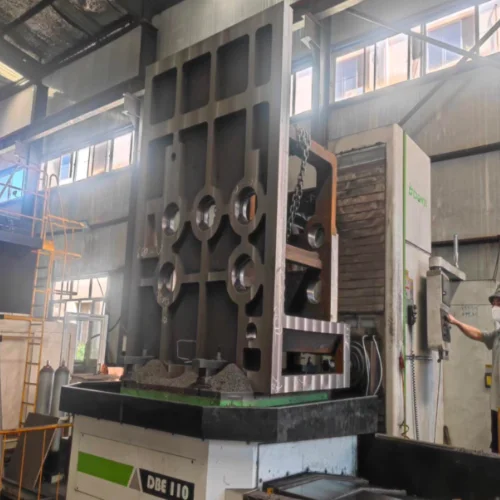
One-Piece Casting
Ergonomic and Efficient Design
Super Simple System
Comprehensive System Protection
The system features cutting adaptive control, automatic tracking of machining trajectories, real-time display of cutting processes, and convenient operation functions such as machining preview. At the same time, it also has an automatic memory protection function for power failure.
Customer Testimonials

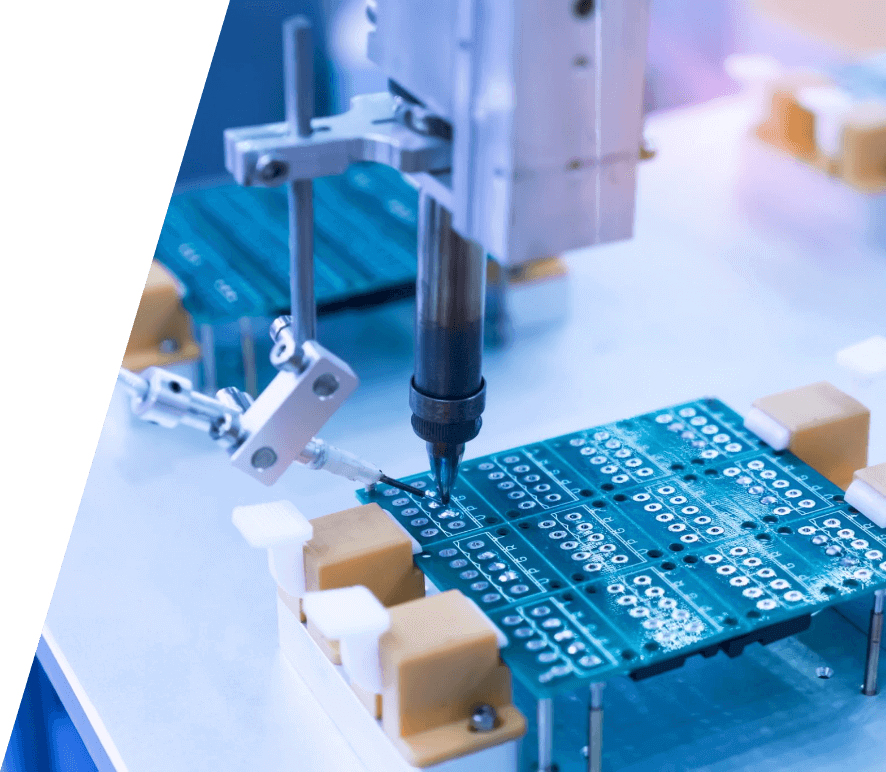
Frequently Asked Questions
What is the maximum thickness the machine can handle for cutting?
What is the difference between this wire saw and BAND SAW?
The cutting speed would be similar, but wire saw’s cut surface quality is far more better. and the kerf loss is smaller.