Have you ever wondered what drives the relentless progress in the technology we use every day? From the smartphones in our pockets to the solar panels powering homes, the secret lies within the heart of Silicon Crystal Cutting machines. But, what hurdles do these technological marvels face, and how do they continuously evolve to meet the ever-growing demands of the tech industry?
Enter the world of silicon crystal cutting—a realm where precision meets innovation. With technologies like Sapphire Wire Cutting and brands like SHINE leading the charge, we’re on the brink of a revolution that promises to redefine our technological capabilities. The journey of transforming a raw silicon crystal into a powerhouse of technology is nothing short of remarkable, urging you to delve deeper into this fascinating process.
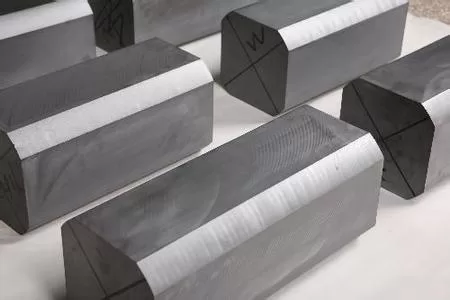
Table of Contents
Introduction
In the modern world, silicon plays a pivotal role in the technology sector, serving as the backbone for countless devices and innovations. At the heart of silicon’s journey from raw material to technological cornerstone lies the precision and ingenuity of silicon crystal cutting machines. This guide aims to provide a comprehensive overview of these machines, exploring their importance, technologies, selection criteria, applications, and the challenges they address.
SHINE, as a leading brand in the field, exemplifies the innovation and excellence in silicon crystal cutting technology. From the basics of cutting to the latest advancements and trends, this guide will navigate through the intricate world of silicon cutting, ensuring a deep understanding of its critical role in today’s technological landscape.
Part 1: The Basics of Silicon Crystal Cutting
1.1 What is Silicon Crystal Cutting?
Definition and Importance
Silicon crystal cutting is the process of slicing silicon crystals into thin wafers, which are then used in the production of semiconductors, solar cells, and various other electronic devices. The precision of the cut directly impacts the efficiency and performance of the final product, making the cutting process crucial in the semiconductor and solar energy sectors.
1.2 Types of Silicon Crystals
- Monocrystalline Silicon: Known for its purity and uniformity, resulting in high efficiency in semiconductor applications.
- Polycrystalline Silicon: Less expensive but slightly less efficient than monocrystalline silicon, often used in solar panels.
1.3 Understanding Cutting Machines
How Silicon Cutting Machines Work
Silicon cutting machines use various technologies to slice silicon crystals with precision. Key components include the cutting mechanism (blade, laser, or wire), alignment systems, and control units that ensure accuracy.
Part 2: Technologies in Silicon Crystal Cutting
2.1 Traditional vs. Modern Cutting Techniques
Comparison and Evolution
Traditional methods, such as mechanical sawing, have evolved into more sophisticated techniques like laser cutting and diamond wire cutting, offering improved precision and reduced waste.
2.2 Laser Cutting Technology
Advantages and Applications
Laser cutting provides unparalleled accuracy, minimal material loss, and flexibility in cutting patterns, making it ideal for intricate semiconductor designs.
2.3 Diamond Wire Cutting
Process and Benefits
Utilizing thin diamond-encrusted wires, this method offers fast, precise cuts with significantly less material waste compared to traditional sawing.
2.4 Photolithography in Silicon Cutting
Role and Innovations
Although not a cutting technology per se, photolithography plays a crucial role in patterning silicon wafers post-cutting, enabling the creation of complex circuits on semiconductors.
Part 3: Selecting the Right Silicon Crystal Cutting Machine
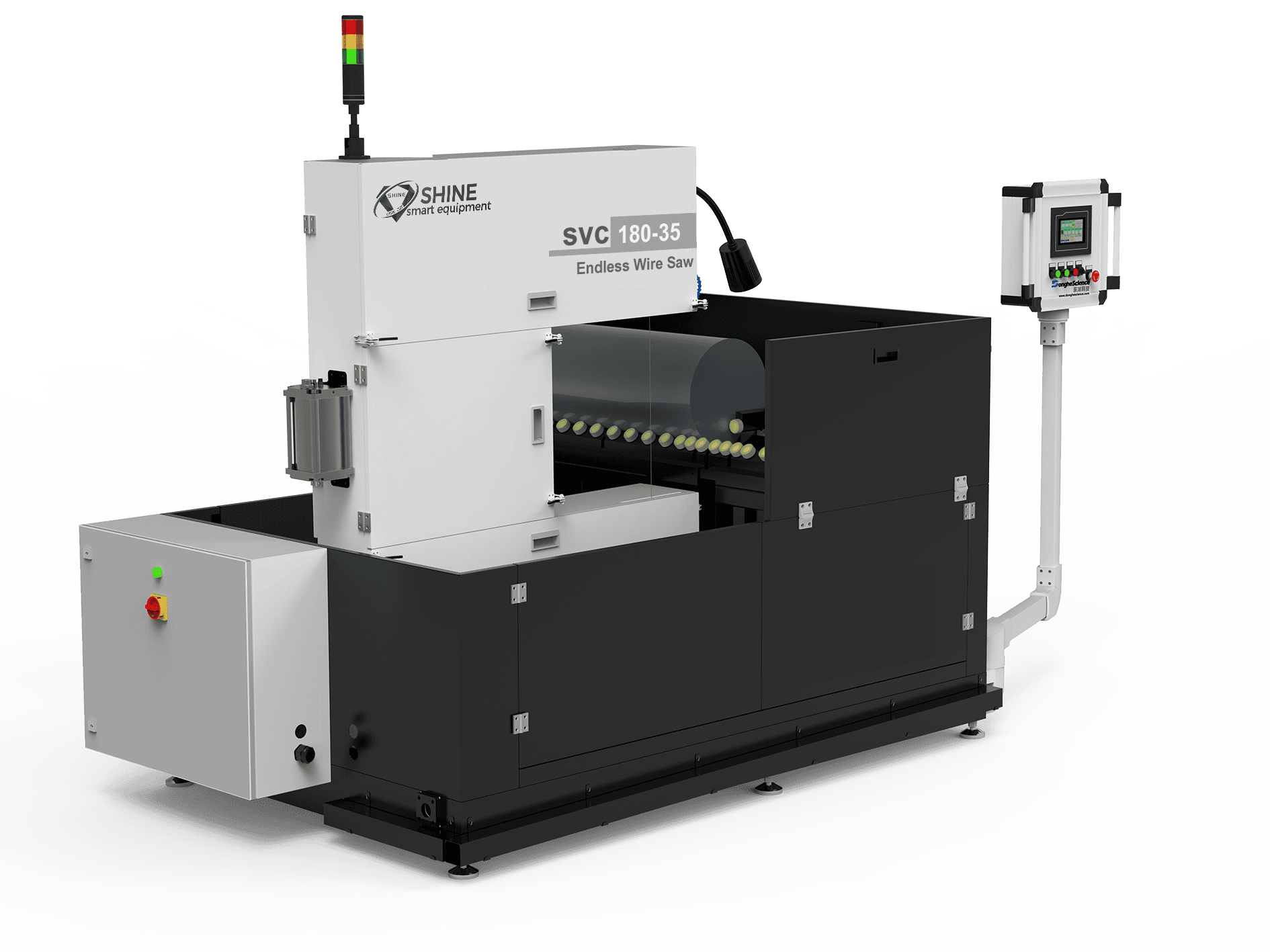
3.1 Factors to Consider
- Precision and Accuracy: Essential for meeting stringent specifications of semiconductor and solar panel manufacturing.
- Speed and Efficiency: Determines production throughput and overall cost-effectiveness.
- Durability and Maintenance: Impacts the long-term operation costs and machine uptime.
3.2 Top Manufacturers and Brands
A comparative analysis of leading manufacturers, including SHINE, reveals a commitment to innovation and quality in the realm of silicon crystal cutting.
3.3 Cost Analysis
Initial Investment vs. Operational Costs
Balancing the upfront cost of cutting machines with ongoing maintenance and operational expenses is crucial for cost-effective production.
Cost Analysis for Silicon Crystal Cutting Machines by SHINE
- Initial Investment: The upfront cost encompasses purchasing SHINE’s Silicon Crystal Cutting Machines, known for their advanced technology and reliability. This includes the price of the machine itself and any additional setup fees.
- Operational Costs: Monthly operational expenses cover electricity, consumables like cutting wires (diamond or sapphire), and routine maintenance materials. SHINE machines are designed for energy efficiency and minimal consumable waste to manage costs effectively.
- Maintenance and Upgrades: Regular maintenance ensures the longevity and optimal performance of SHINE Silicon Crystal Cutting Machines. Budgeting for periodic upgrades and parts replacement is essential for keeping the technology up-to-date.
- Training and Support: Investing in comprehensive training for operators maximizes the efficiency and productivity of SHINE’s cutting machines. Support contracts offer ongoing assistance and software updates.
- Cost-Benefit Analysis: Evaluating the total cost against the productivity gains, reduced material wastage, and enhanced precision of SHINE Silicon Crystal Cutting Machines illustrates the long-term financial benefits, positioning these machines as a wise investment for future-proofing manufacturing processes.
Part 4: Applications of Silicon Crystal Cutting Machines
4.1 In the Semiconductor Industry
Chips and Microprocessors Production
The precision cutting of silicon wafers is foundational in the manufacturing of chips and microprocessors, dictating their performance and efficiency.
4.2 Solar Energy Sector
Manufacturing of Photovoltaic Cells
Silicon cutting machines play a vital role in the production of solar panels, influencing their efficiency and cost.
4.3 Research and Development
Experimental Applications
Innovations in silicon cutting techniques often stem from R&D efforts, leading to breakthroughs in semiconductor technology and solar energy solutions.
Part 5: Challenges and Solutions
5.1 Technical Challenges
Dealing with Material Wastage
Innovative cutting techniques, like diamond wire cutting, aim to minimize material loss, enhancing overall sustainability and efficiency.
Ensuring Precision in Cutting
Advancements in control systems and cutting technologies continue to push the boundaries of precision in silicon crystal cutting.
5.2 Environmental Concerns
Sustainability Practices
The industry is increasingly adopting practices that reduce environmental impact, from waste reduction to energy-efficient operations.
5.3 Future Trends
AI and Automation in Silicon Cutting
Artificial intelligence and automation are set to revolutionize silicon cutting, improving precision, efficiency, and reducing human error.
Part 6: Maintenance and Safety
6.1 Routine Maintenance Tips
Routine maintenance is pivotal for ensuring the longevity, efficiency, and reliability of your SHINE Silicon Crystal Cutting Machine. By adhering to a regular maintenance schedule, you can minimize downtime, optimize performance, and extend the lifespan of your equipment. Here are detailed tips to help you maintain your SHINE machine in top condition.
Daily Checks
- Cleanliness: Start each day by cleaning the machine’s exterior and work area. Remove any silicon debris, dust, or residues that could affect the machine’s operation or precision.
- Visual Inspection: Examine the cutting tools, wires, and laser systems for signs of wear or damage. Early detection of issues can prevent more significant problems down the line.
Weekly Maintenance
- Lubrication: Check and lubricate moving parts and bearings weekly to ensure smooth operation. Use the recommended lubricants by SHINE to avoid compatibility issues.
- Cooling System Check: Verify that the cooling system is functioning correctly to prevent overheating. Clean any filters and check coolant levels, topping up or replacing fluids as necessary.
Monthly Inspections
- Alignment Checks: Ensure that all cutting components are correctly aligned. Misalignment can lead to inaccurate cuts and increased wear on parts.
- Wire and Blade Examination: Inspect diamond or sapphire cutting wires and blades for wear or damage. Replace them as needed to maintain cutting precision and efficiency.
- Software Updates: Check for any software updates from SHINE and install them to benefit from the latest improvements and features.
Quarterly Servicing
- Professional Inspection: Schedule a professional inspection with a SHINE technician every quarter. They can identify issues that may not be apparent during routine checks and perform calibrations.
- Deep Cleaning: Conduct a thorough cleaning of the machine’s interior, focusing on areas that are difficult to reach during daily or weekly cleaning routines.
Annual Maintenance
- Comprehensive Overhaul: Once a year, perform a comprehensive maintenance check, including replacing any worn-out parts, thoroughly testing the machine’s functionality, and making any necessary adjustments.
- Performance Review: Evaluate the machine’s performance over the past year to identify any potential improvements or adjustments needed for optimal operation.
Documentation and Records
- Maintenance Log: Keep a detailed maintenance log for your SHINE Silicon Crystal Cutting Machine. Record all inspections, replacements, and services to track the machine’s maintenance history and plan future actions.
- Feedback to SHINE: Provide feedback on your machine’s performance and any maintenance issues to SHINE. This can help improve future models and maintenance protocols.
By following these routine maintenance tips, you can ensure that your SHINE Silicon Crystal Cutting Machine operates at its best, supporting your production needs with unmatched precision and reliability. Regular maintenance not only extends the life of your equipment but also ensures that it continues to meet the high standards of quality and efficiency that SHINE is known for.
6.2 Safety Protocols
Ensuring safety during the operation of Silicon Crystal Cutting Machines is paramount. Adhering to the following protocols can help prevent accidents and ensure a safe working environment:
- Personal Protective Equipment (PPE): Operators must wear appropriate PPE, including safety goggles, gloves, and ear protection, to guard against potential hazards such as flying debris and high noise levels.
- Emergency Stop Features: Familiarize all users with the machine’s emergency stop mechanisms. Regularly check these features for proper functionality to ensure they can halt operations immediately if needed.
- Training and Certification: Ensure that operators are thoroughly trained and certified to use the Silicon Crystal Cutting Machine. This includes understanding the operation manual, safety features, and emergency procedures.
- Regular Maintenance Checks: Conduct routine maintenance checks to identify and rectify potential hazards like loose components, frayed wires, or malfunctioning safety guards.
- Clear Work Area: Maintain a clean and uncluttered work area around the Silicon Crystal Cutting Machine. Remove any unnecessary tools or materials that could pose tripping hazards or interfere with safe operation.
- Ventilation Systems: Use adequate ventilation systems to remove harmful dust and fumes generated during cutting processes. Regularly inspect and maintain these systems to ensure their efficiency.
- Fire Safety Measures: Equip the work area with fire extinguishers and other fire safety equipment. Ensure materials that could ignite or exacerbate a fire are stored safely away from the cutting area.
By implementing these safety protocols, operators of Silicon Crystal Cutting Machines can minimize risks and create a safer working environment. It’s essential to review and update these protocols regularly to adapt to new safety standards and technological advancements.
Conclusion
As we’ve ventured through the intricate landscape of Silicon Crystal Cutting machines, it’s clear that they are the unsung heroes of the tech world. With each slice, they pave the way for advancements that seem straight out of science fiction. However, the road is fraught with challenges, from minimizing material wastage to enhancing precision. Yet, with innovations from SHINE and breakthroughs in Sapphire and Diamond Wire Cutting, the future is luminous.
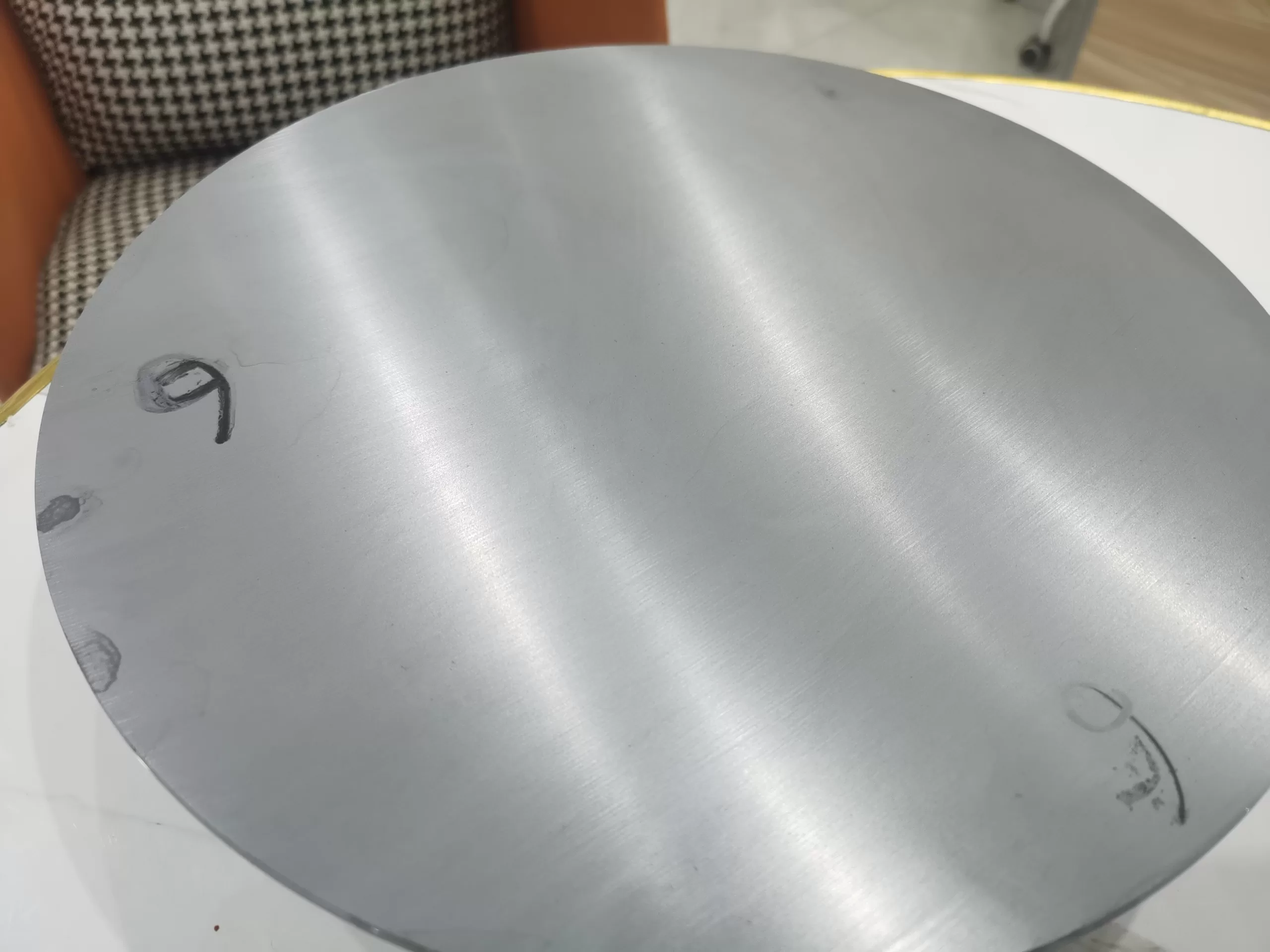
Are you ready to be a part of this exciting journey? Embrace the cutting edge of technology and discover how Silicon Crystal Cutting machines can unlock new horizons for your projects. Click here to explore our selection and take the first step towards the future, today.
For an authoritative insight into the advancements and applications of Silicon Crystal Cutting Machines, especially in semiconductor and solar panel manufacturing, visit IEEE Xplore Digital Library. This platform offers a wealth of research and articles on the latest technological innovations and trends in the field.
FAQs
Q: What is Silicon Crystal Cutting?
A: Silicon Crystal Cutting involves slicing silicon crystals into thin wafers, essential for semiconductor and solar panel production, utilizing precise machines for optimal results.
Q: Why choose SHINE for Silicon Crystal Cutting machines?
A: SHINE stands at the forefront of innovation, offering cutting-edge machines that provide unmatched precision, efficiency, and reliability in silicon slicing.
Q: How does Diamond Wire Cutting enhance silicon processing?
A: Diamond Wire Cutting offers a precise, efficient method for slicing silicon, reducing material wastage and enhancing the quality of the wafers for semiconductor use.
Q: Can Silicon Crystal Cutting machines be used for solar panel manufacturing?
A: Absolutely. These machines are pivotal in producing the silicon wafers that form the core of photovoltaic cells in solar panels, ensuring efficiency and performance.
Q: What factors should be considered when selecting a Silicon Crystal Cutting machine?
A: Key considerations include precision, speed, maintenance requirements, and overall durability to ensure the machine meets your production needs.
Q: What are the future trends in Silicon Crystal Cutting technology?
A: Future trends point towards greater automation, AI integration for enhanced precision, and sustainability practices to minimize environmental impact.