-Single Diamond Wire Saw
Table of Contents
Brief Description
This silicon ingot cutting wire saw utilizes a cutting tool known as a circular diamond wire loop. It is a closed-loop diamond wire that can move in a single direction without the need for reversing. The circular diamond wire enables high linear speeds, reaching even up to 60 m/s. As a result, it allows for fast cutting speeds during silicon rod cutting, while maintaining superior cutting surface quality.
Unique features, performance, and advantages of silicon ingot cutting wire saw
- High precision cutting: The diamond wire cutting equipment employs precise cutting technology, enabling highly accurate silicon rod cutting. It ensures consistent diameters and smooth cutting surfaces, resulting in precise dimensions and excellent surface quality of the cut silicon rods.
- High efficiency and productivity: The diamond wire cutting equipment offers high-speed cutting capabilities, allowing for fast silicon rod cutting and increased production efficiency. Compared to traditional cutting methods, wire cutting significantly reduces cutting time, thus enhancing production line throughput.
- Low wastage and material savings: The diamond wire cutting equipment minimizes material wastage during the cutting process. With its fine and precise cutting line, it maximizes material utilization and reduces waste, contributing to efficient resource utilization.
- Flexibility and versatility: The diamond wire cutting equipment is adaptable to silicon rods of varying diameters and lengths, catering to diverse cutting requirements. It can be adjusted according to specific specifications, making it suitable for a range of silicon rod cutting applications. Furthermore, wire cutting equipment can be utilized for cutting other materials like metals, fiberglass, offering versatility across different industries.
- Automation and precise control: Equipped with advanced automation control systems, the diamond wire cutting equipment enables precise control of cutting speed, pressure, and position. This simplifies operations, minimizes human errors, and ensures consistent and stable cutting results for each silicon rod.
In summary, diamond wire cutting equipment offers unique characteristics and advantages such as high precision, efficiency, low wastage, flexibility, and precise control for silicon rod cutting. It provides reliable cutting solutions for silicon rod manufacturing and related industries, enhancing production efficiency and product quality.
Case Studies
Cutting Video of successful case

Pictures of successful case
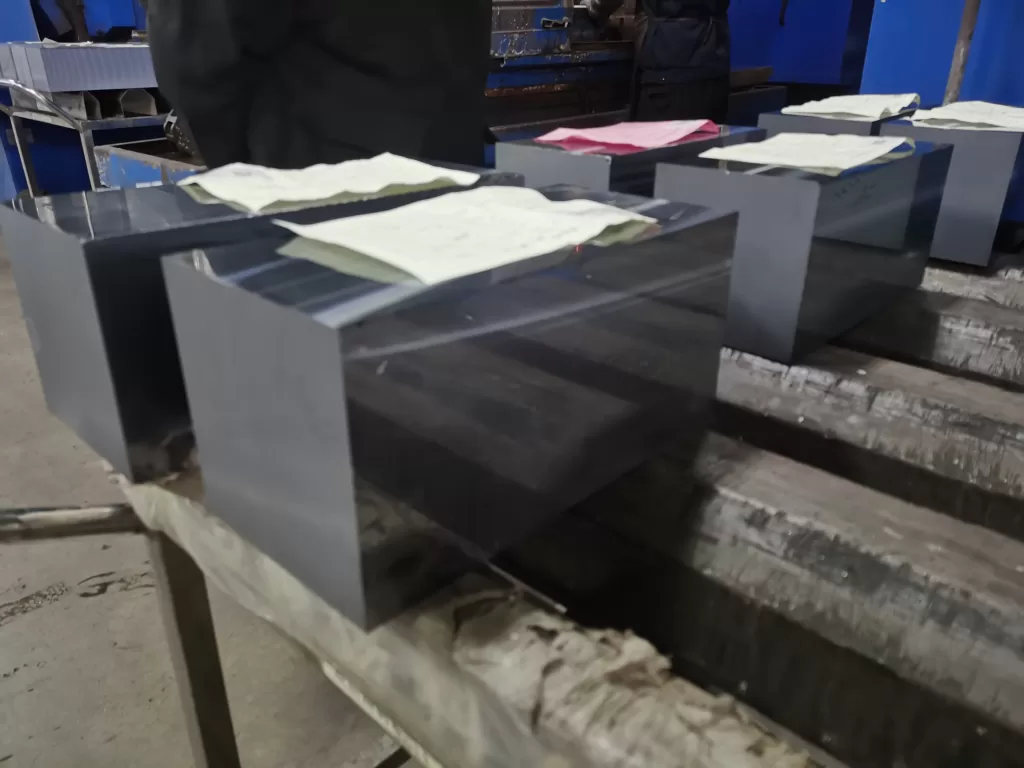
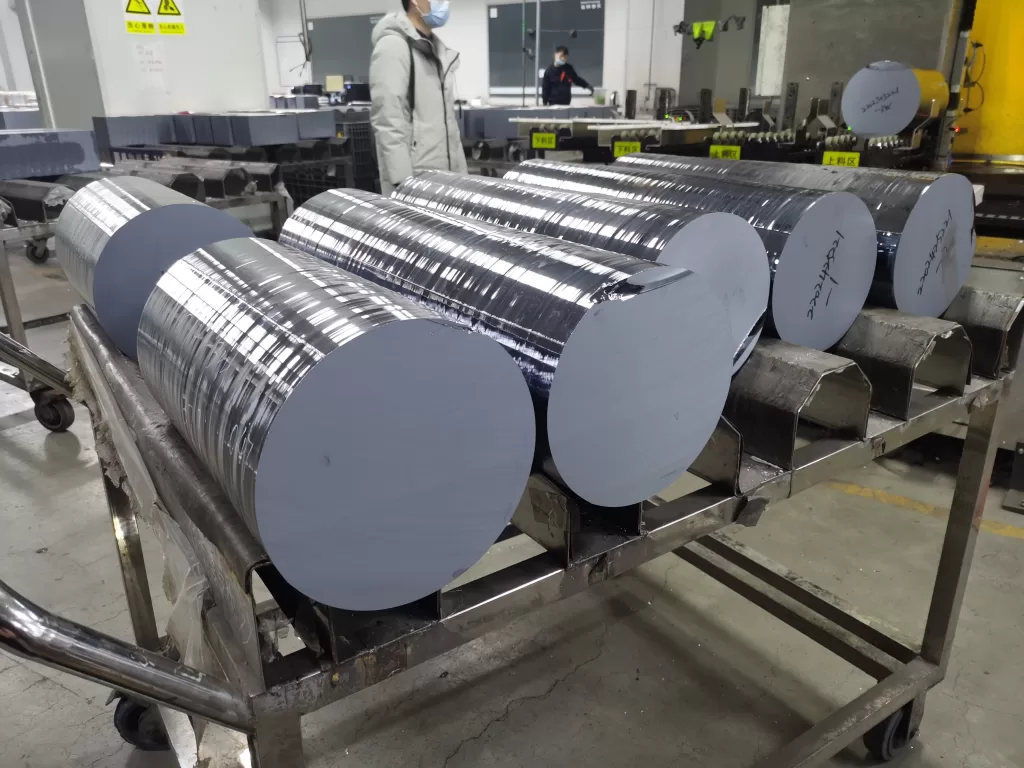
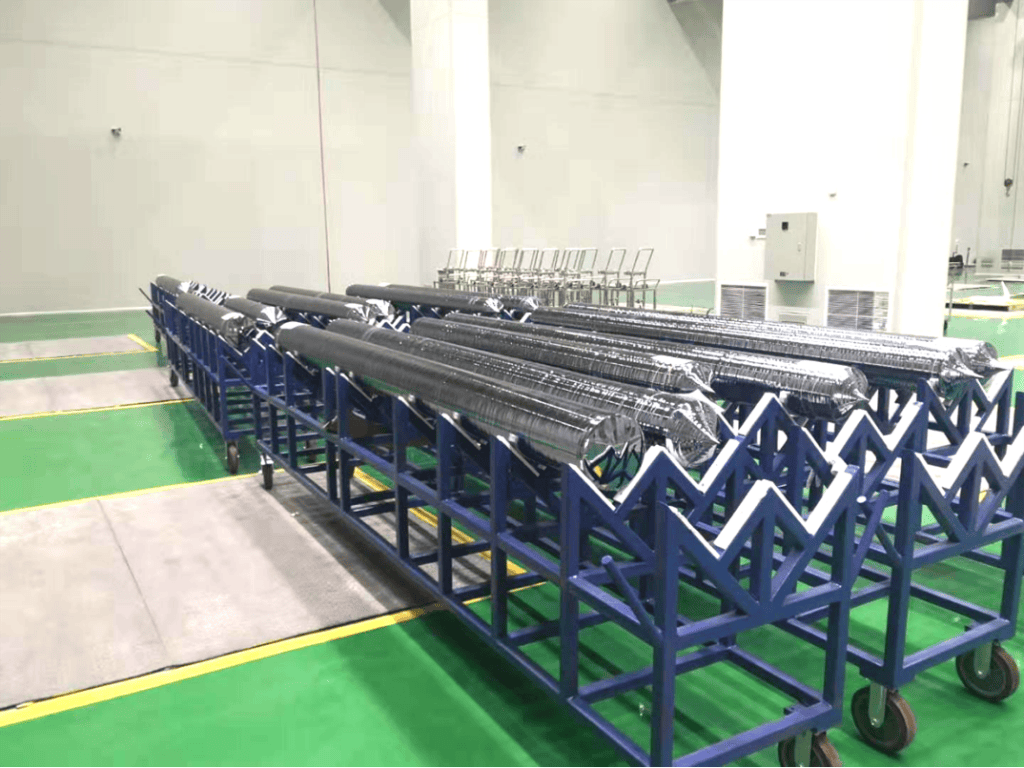
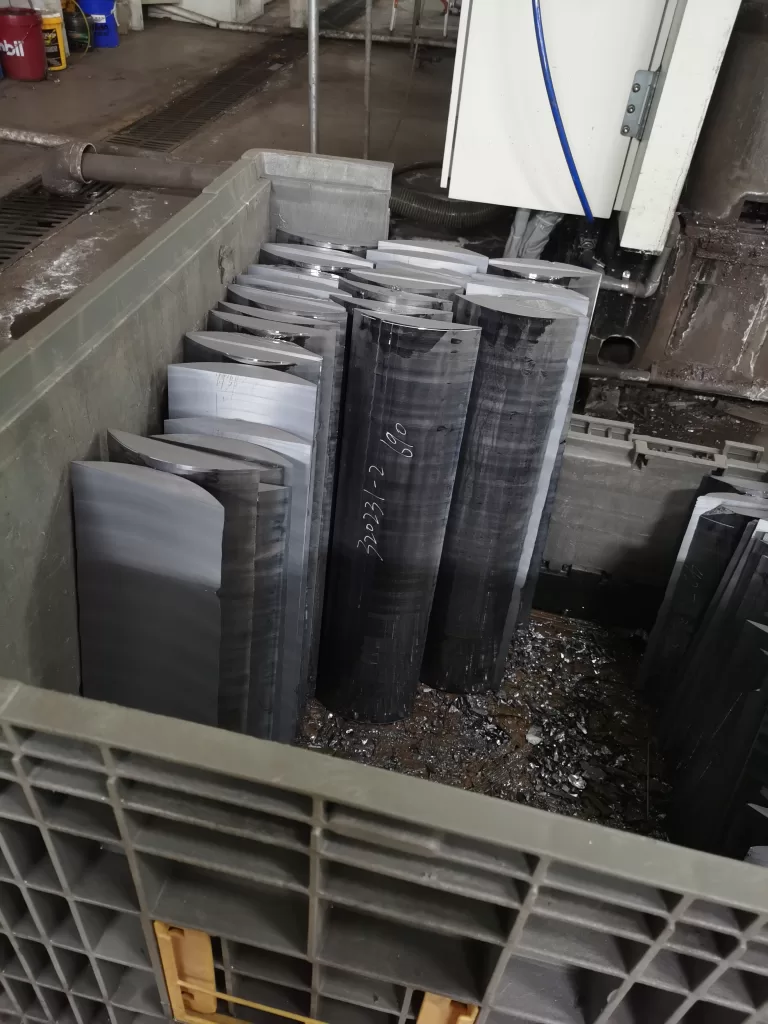
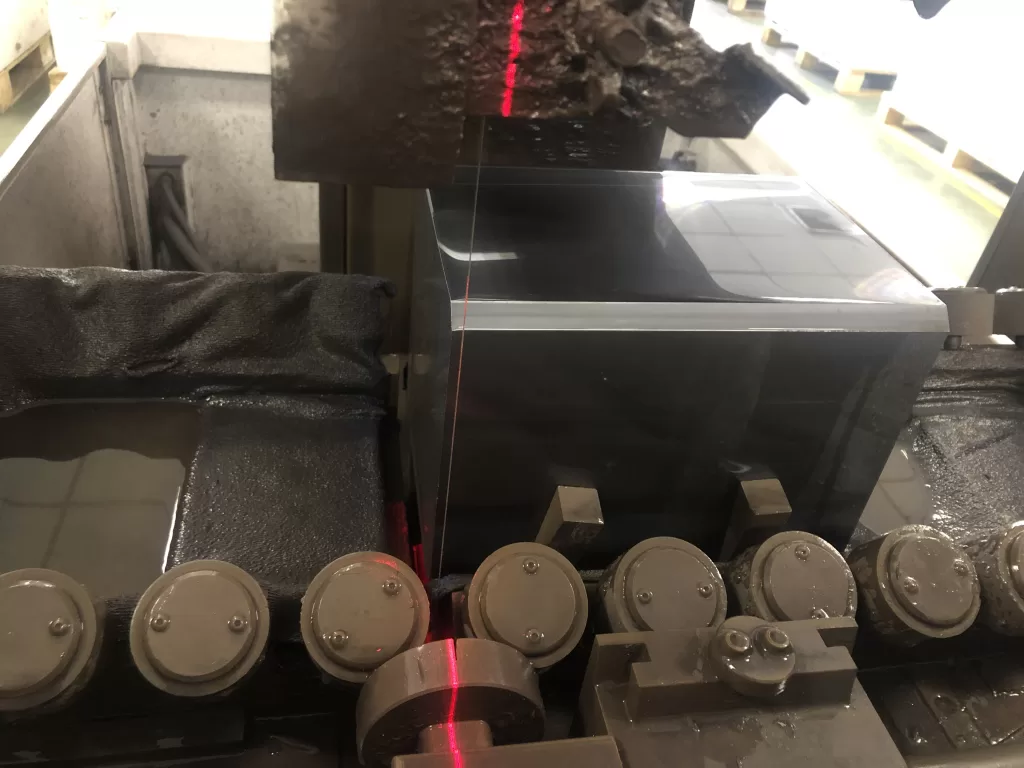
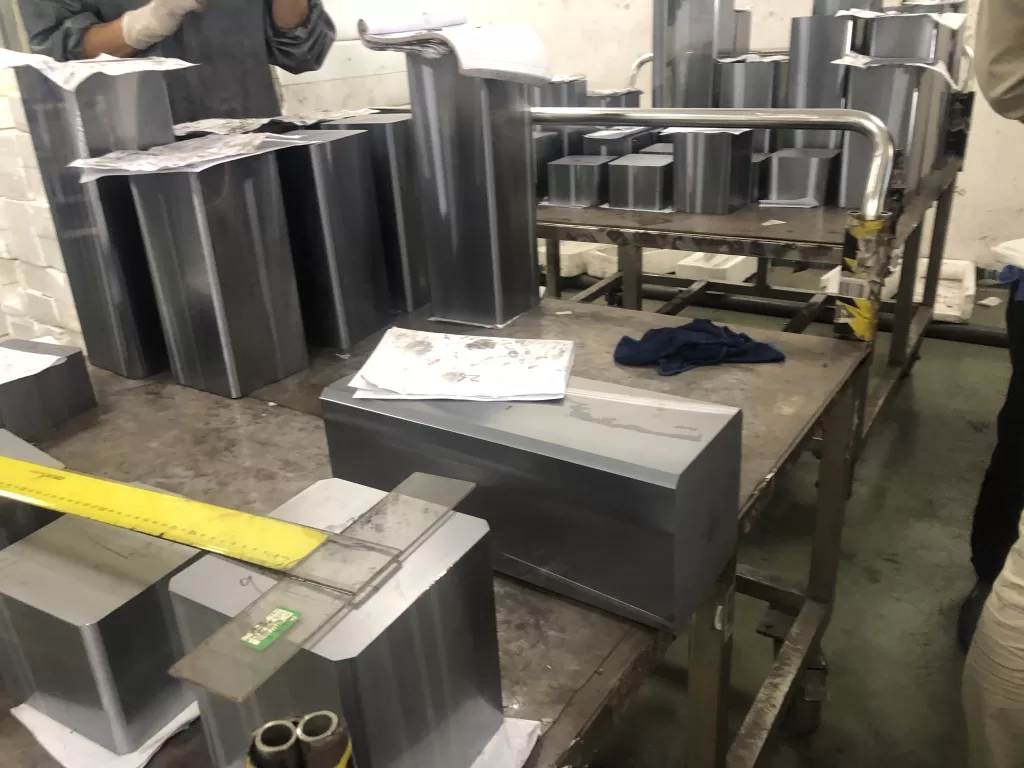
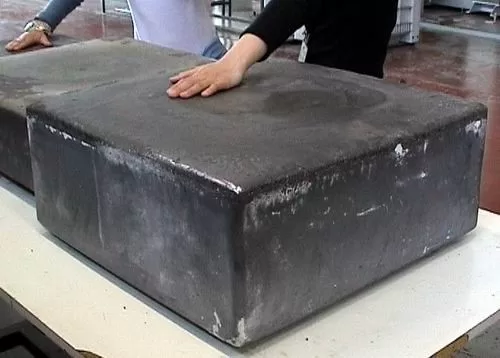
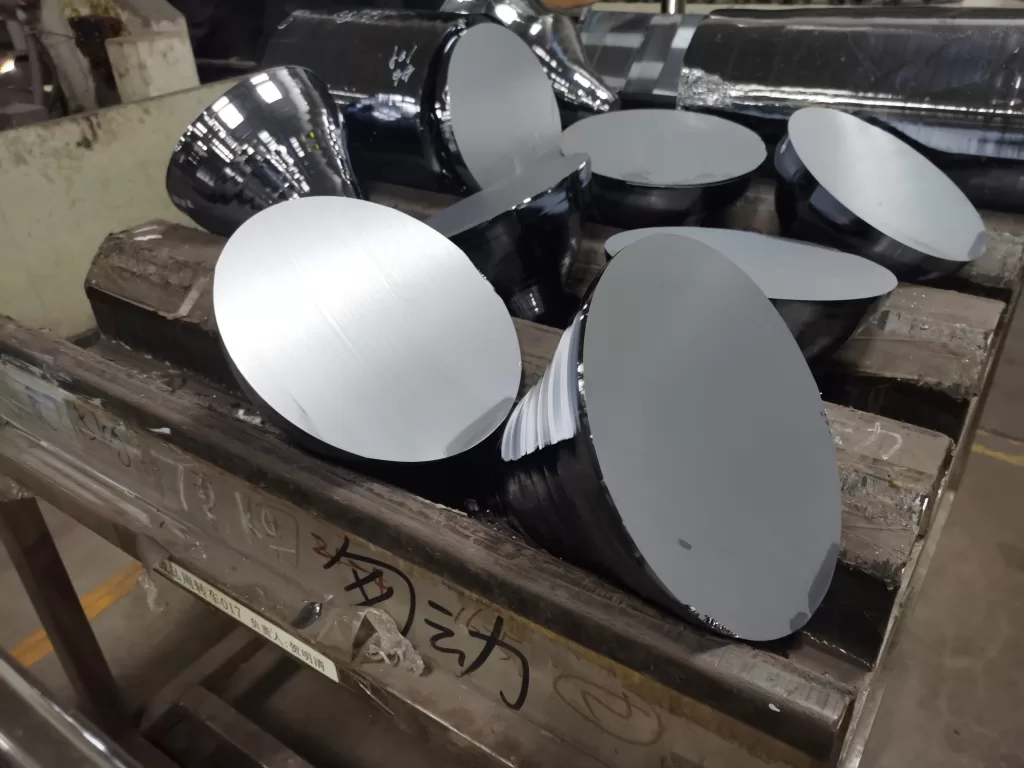
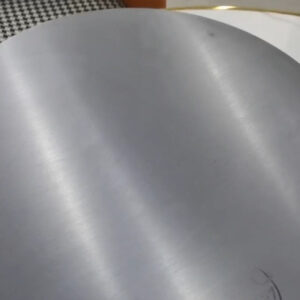
Successful application examples of silicon Ingot cutting wire saw in different industries and projects:
1,Semiconductor Industry:
Silicon rods are critical materials in semiconductor chip manufacturing, making them widely used in the semiconductor industry.
2,Photovoltaic Industry:
Silicon rods are used to produce solar cell wafers, playing a crucial role in the solar photovoltaic industry.
3,Fiber Optics Communication:
Silicon rods are employed in the production of preforms for optical fibers, contributing to the fiber optics communication field.
4,Medical Devices:
Silicon rods can be utilized in the manufacturing of medical devices such as artificial joints and orthopedic implants.
Video of this silicon cutting machine
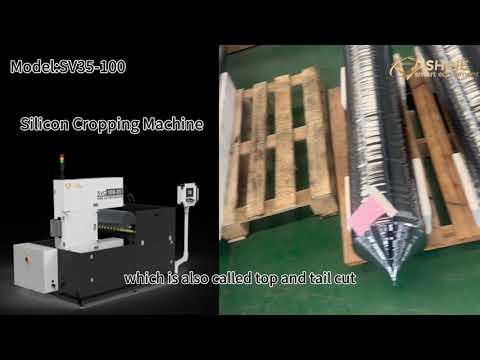
The working principle of a single-wire silicon ingot cutting machine
Product Detail
1,Cutting Line Orientation:
The cutting wire is positioned perpendicular to the ground, while the silicon rod is horizontally placed on the loading platform.
2,High-Speed Cutting Wire Motion:
The cutting wire moves at high speed along its circular path, maintaining constant tension and maintaining its sharpness during the cutting process.
3,Vertical Cutting:
As the cutting wire moves, the loading platform moves horizontally, allowing for vertical cutting of the silicon rod. This vertical cutting method, known as vertical wire cutting, enables precise and efficient cuts.
4,Control and Precision:
The cutting machine is equipped with a control system that ensures precise movement of the cutting wire and the loading platform. The control system allows for accurate positioning and motion control, resulting in consistent and high-quality cuts.
Typical specifications for a single-wire silicon rod cutting machine:
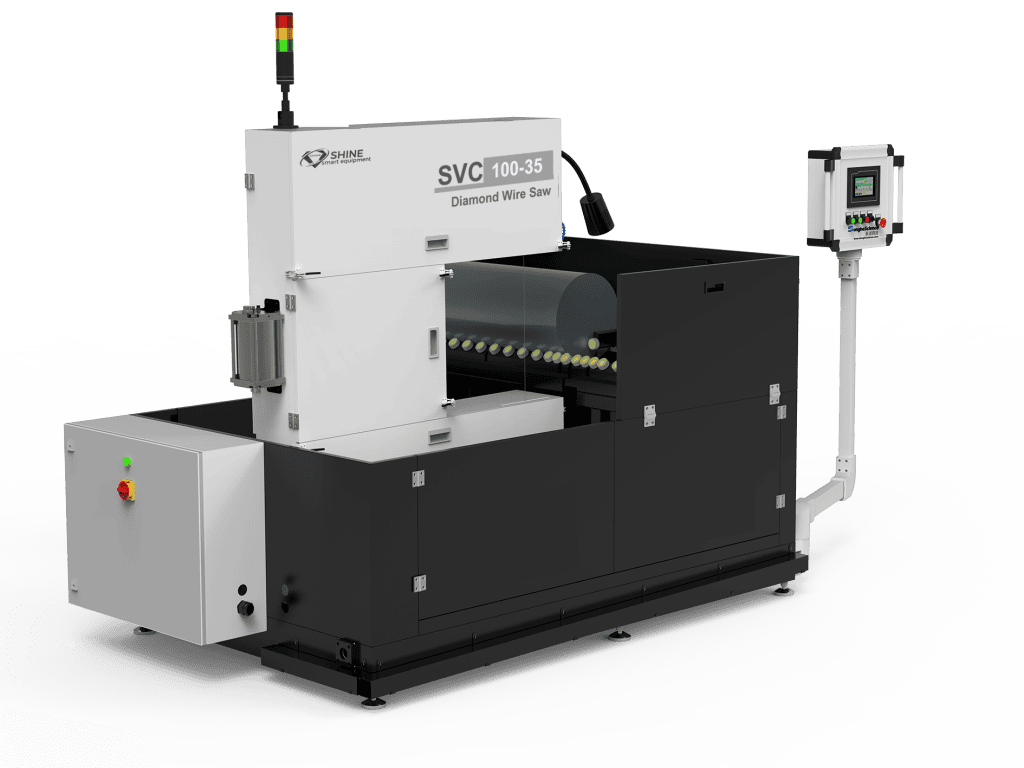
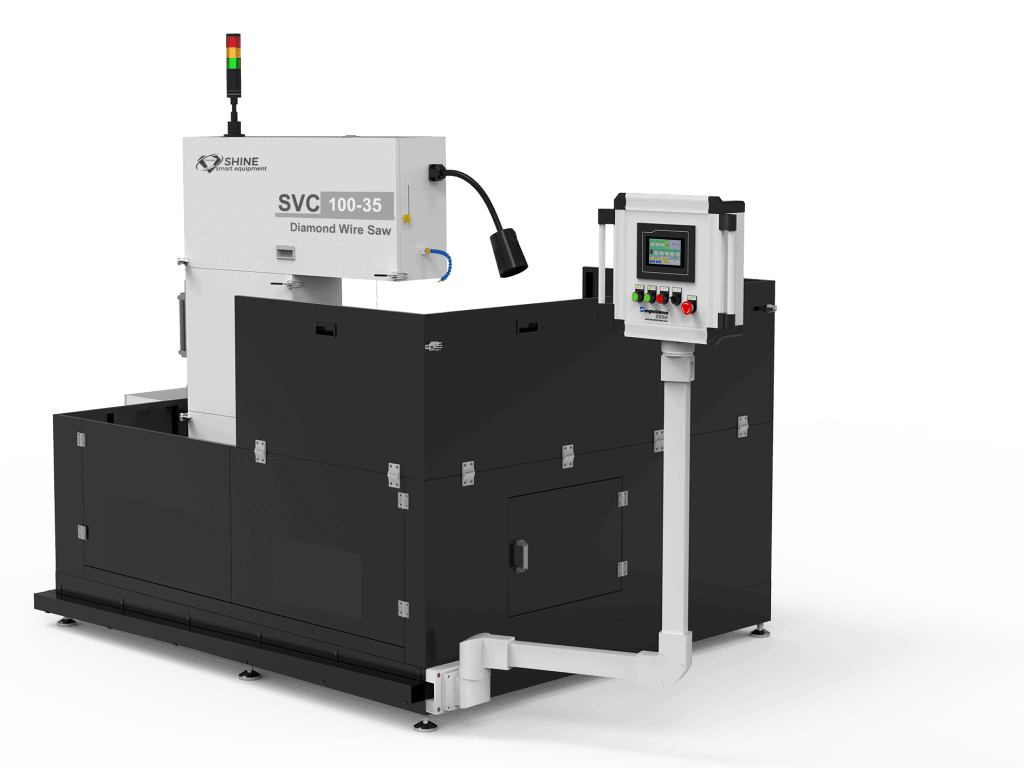
Machine Spec
1,Machine Dimension: L3000mm*W1800mm*H1500mm
2 Spindle Motor:3.5 kw
3 Motor speed:2800 RMP
4 Total Weight:2500 KG
5 loading capacity:800 KG
6 Max linear speed:84 m/s
Material Dimension
Material dimension : smaller than L1000mm*W350mm*H350mm
Support and Services
Maintenance and Servicing:
We provide comprehensive maintenance and servicing services to ensure the long-term reliable operation of the silicon rod cutting equipment. Our dedicated maintenance team possesses extensive experience and technical knowledge to promptly respond to and resolve equipment issues. We made check list to conduct regular preventive maintenance, inspecting and adjusting critical components to ensure optimal performance and accuracy. Whether it’s routine maintenance or emergency repairs, we are committed to delivering fast and efficient servicing to minimize equipment downtime.
and we have local service available in US and Canada.
Training:
We offer comprehensive training programs designed to empower customers with in-depth knowledge and proficiency in operating and maintaining the silicon ingot cutting machine. Our training courses cover basic equipment operation, safe usage practices, maintenance procedures, and troubleshooting. Customized training content and flexible training methods, including on-site training, remote training, and provision of training materials, are provided based on customer needs and backgrounds. Through our training programs, customers can enhance their operational skills, improve equipment efficiency, and ensure long-term reliable performance.
Consulting:
We provide professional consulting services to meet customer needs regarding silicon ingot cutting machine and related areas. Our team of experts offers tailored advice and solutions based on specific requirements. Whether it’s equipment selection, process optimization, production line layout, or quality control, we collaborate with customers, providing professional guidance and technical support. We strive to establish long-term partnerships with customers, working together to address various technical and engineering challenges, meet their needs, and achieve mutual success.