Table of Contents
Introduction-Unidirectional Cutting and Bidirectional Cutting
Diamond wire cutting machines have revolutionized the field of stone and material processing, offering efficient and precise cutting methods. Within this realm, there are two primary cutting techniques: unidirectional and bidirectional cutting. In this article, we will delve into the concepts of unidirectional and bidirectional cutting in the context of diamond wire cutting machines.
Recent advancements in diamond wire cutting technology have expanded the capabilities of both unidirectional and bidirectional cutting. These advancements include innovations in wire composition, machine design, and control algorithms. These developments have addressed some of the historical limitations of each method, enhancing their performance across various applications.
Unidirectional Cutting
Unidirectional cutting, as the name suggests, involves the movement of the diamond wire in a single direction during the cutting process. In this method, the wire travels in a linear path, engaging with the material to create a clean and precise cut. Unidirectional cutting is often preferred when working with delicate materials or when achieving a specific type of cut is crucial.
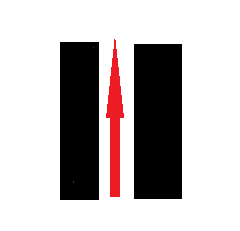
Advantages of Unidirectional Cutting:
- Reduced Wire Wear: Unidirectional cutting tends to cause less wear on the diamond wire since the movement is consistent and linear. This can result in longer-lasting wires and reduced operational costs.
- Precise Control: This cutting method offers precise control over the cutting process. It is suitable for intricate designs, detailed shapes, and when the cut’s accuracy is paramount.
- Smooth Surface Finish: Unidirectional cutting generally provides a smoother surface finish on the cut material due to the consistent wire movement.
- Minimized Chipping: Delicate materials, like brittle stones, are less likely to chip or crack during unidirectional cutting, as the movement is predictable and steady.
Bidirectional Cutting
Bidirectional cutting involves the movement of the diamond wire in both forward and backward directions alternately during the cutting process. This technique is often chosen for its efficiency and faster cutting speeds. While bidirectional cutting may result in slightly less precision compared to unidirectional cutting, it is favored when time is a critical factor and a certain level of precision can still be maintained.
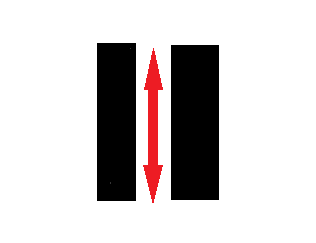
Advantages of Bidirectional Cutting:
- Faster Cutting Speeds: Bidirectional cutting can be faster than unidirectional cutting, as the wire engages with the material during both forward and backward movements.
- Higher Productivity: The increased cutting speed directly contributes to higher productivity, making this method ideal for large-scale projects where time is of the essence.
- Efficient Material Removal: Bidirectional cutting can be particularly effective in removing larger volumes of material quickly.
- Cost-Effective: While the wire wear might be slightly higher due to the back-and-forth motion, the increased efficiency often makes bidirectional cutting a cost-effective choice for certain applications.
Choosing the Right Method
The choice between unidirectional and bidirectional cutting depends on the specific requirements of the project and the characteristics of the material being cut. For projects where precision, smooth finishes, and intricate designs are essential, unidirectional cutting might be the preferred method. On the other hand, when speed, productivity, and efficient material removal are the main priorities, bidirectional cutting can be more suitable.
It’s important to note that advancements in diamond wire technology and machine controls have led to improved performance in both cutting methods. Many modern diamond wire cutting machines allow operators to switch between unidirectional and bidirectional cutting modes based on the project’s needs, offering a higher degree of flexibility and adaptability.
Conclusion-Unidirectional Cutting and Bidirectional Cutting
Unidirectional cutting, while offering meticulous precision, has benefited from improvements in wire durability. This has extended the lifespan of the diamond wire, allowing for longer periods of uninterrupted cutting. Additionally, modern machine controls have introduced more sophisticated ways to adjust the cutting parameters during unidirectional cutting, optimizing the process for different materials and shapes.
On the other hand, bidirectional cutting has seen enhancements in terms of accuracy. While it was traditionally associated with slightly lower precision due to the alternating wire movements, modern systems have minimized this gap through advanced control mechanisms. These mechanisms ensure that the wire’s path during the backward movement aligns closely with the forward path, resulting in improved overall accuracy.
In conclusion, the choice between unidirectional and bidirectional cutting in diamond wire cutting machines is no longer a strict trade-off between precision and efficiency. Advancements in technology have bridged the gaps, allowing both methods to excel in their respective strengths while minimizing their weaknesses. The decision on which method to use now depends on a careful evaluation of the project’s requirements and the available technology, ensuring that the optimal cutting approach is chosen for each unique scenario.