In the world of semiconductor manufacturing, the process of wire sawing plays a pivotal role in shaping silicon rods into wafers. This technique is essential not just for its precision but also for its ability to maximize material usage. Wire sawing, at its core, involves using a thin wire, often coated with abrasive particles, to slice through silicon rods. The importance of this process cannot be overstated, as it directly impacts the efficiency and quality of semiconductor devices. So, how exactly does wire sawing work, and why is it so crucial? Let’s dive in.
In recent years, wire sawing technology has experienced numerous innovations, revolutionizing the industry. These advancements include the development of new wire materials and the integration of automation and precision cutting techniques. For instance, diamond wire cutting machines have become the gold standard due to their durability and cutting efficiency. Additionally, automation has introduced unparalleled precision, reducing human error and enhancing consistency. Imagine a world where every cut is perfect and every slice is uniform—these diamond wire saw machines are making that a reality.
One of the primary goals in wire sawing is to enhance yield, which means getting the maximum number of usable wafers from each silicon rod. Several strategies can be employed to achieve this. For starters, optimizing the wire tension and speed can significantly reduce material waste. Moreover, using advanced cooling techniques can prevent overheating, which often leads to cracks and defects. Here are some key methods to improve yield:
- Optimized Wire Tension: Maintaining the right tension ensures cleaner cuts and reduces the likelihood of wire breakage.
- Advanced Cooling: Proper cooling mechanisms prevent thermal damage, ensuring the integrity of the silicon rods.
- Precision Alignment: Ensuring the silicon rod is perfectly aligned with the wire can minimize material loss.
Quality is just as important as yield when it comes to wire sawing. High-quality cuts mean fewer defects and higher performance in the final semiconductor products. Techniques to enhance quality include minimizing surface damage and achieving uniform cuts. Advanced monitoring systems can detect irregularities in real-time, allowing for immediate adjustments. Additionally, using high-quality abrasive materials can result in smoother surfaces, reducing the need for post-sawing treatments. Think of it as the difference between a rough sketch and a finely detailed drawing—quality makes all the difference.
To truly understand the impact of these advanced wire sawing techniques, let’s look at some real-world examples. In one case study, a leading semiconductor manufacturer implemented diamond-coated wires and saw a 20% increase in yield. Another company integrated automated precision cutting and reported a significant reduction in defects. These case studies highlight the practical benefits of adopting advanced wire sawing technologies. They serve as a testament to the fact that innovation not only enhances efficiency but also boosts overall quality.
Introduction to Wire Sawing
Wire sawing technology has revolutionized the way we process silicon rods, making it an indispensable technique in the semiconductor industry. Imagine trying to slice through a loaf of bread with a butter knife; it’s inefficient and messy. Now, picture using a finely serrated bread knife instead—it’s precise, clean, and effective. That’s the essence of wire sawing for silicon rods. This method employs a thin wire, often embedded with abrasive particles, to slice through silicon with high precision and minimal waste.
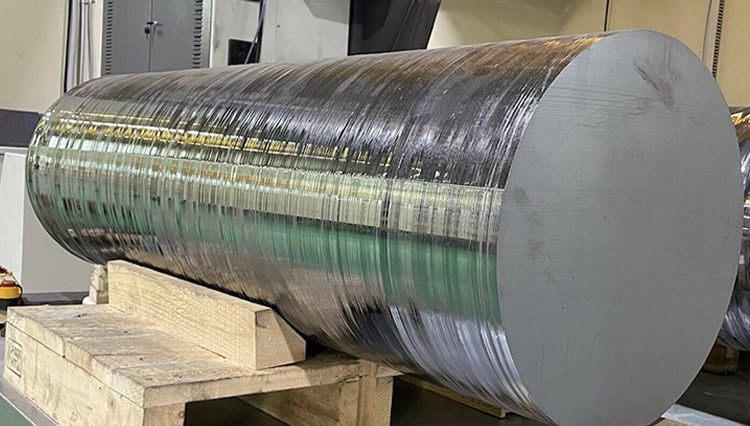
But why is wire sawing so crucial? Silicon rods are the backbone of the semiconductor industry, forming the raw material for countless electronic devices. As technology advances, the demand for high-quality silicon wafers continues to skyrocket. Traditional cutting methods simply can’t keep up with the precision and efficiency required. Enter wire sawing—a game-changer that not only meets but exceeds these demands.
At its core, wire sawing involves a wire moving back and forth, guided by a series of pulleys and tensioners. The wire is coated with abrasive materials like diamond particles, which grind away at the silicon rod as the wire moves. This process can be likened to a high-tech cheese slicer, where the wire is the cutting blade, and the silicon rod is the cheese. The result? Thin, uniform slices of silicon with minimal material loss.
Let’s break down the key components of wire sawing technology:
- Wire: Typically made of steel or other durable materials, the wire is coated with abrasive particles to facilitate cutting.
- Abrasive Particles: Often diamond, these particles are embedded in the wire to enhance cutting efficiency.
- Pulleys and Tensioners: These components guide the wire and maintain the necessary tension for precise cutting.
- Coolant: A liquid coolant is often used to reduce heat and friction during the sawing process, ensuring smooth and efficient cuts.
In summary, wire sawing is a sophisticated technique that combines precision, efficiency, and innovation. It’s the bread knife to the semiconductor industry’s loaf of bread, making it possible to produce high-quality silicon wafers with minimal waste and maximum yield. As we delve deeper into this article, we’ll explore the latest technological advancements, strategies for improving yield, and techniques for enhancing the quality of cut silicon rods.
Technological Innovations in Wire Sawing
Wire sawing technology has come a long way since its inception, and the latest advancements are nothing short of revolutionary. These innovations are not just incremental improvements; they are game-changers that significantly enhance both the yield and quality of silicon rods. So, what are these cutting-edge technologies that are making waves in the industry? Let’s dive in!
First and foremost, new materials for wire saws have been developed, which offer greater durability and precision. Traditional steel wires are being replaced by diamond-coated wires, which are far more resilient and capable of making cleaner cuts. This not only extends the lifespan of the wire but also reduces the frequency of wire replacement, thereby minimizing downtime.
Another groundbreaking innovation is the advent of precision cutting techniques. Modern wire saws are now equipped with advanced sensors and control systems that allow for micrometer-level adjustments. This ensures that each cut is as precise as possible, reducing waste and improving the overall quality of the silicon rods. Imagine being able to slice through a silicon rod with the finesse of a surgeon’s scalpel; that’s the level of precision we’re talking about!
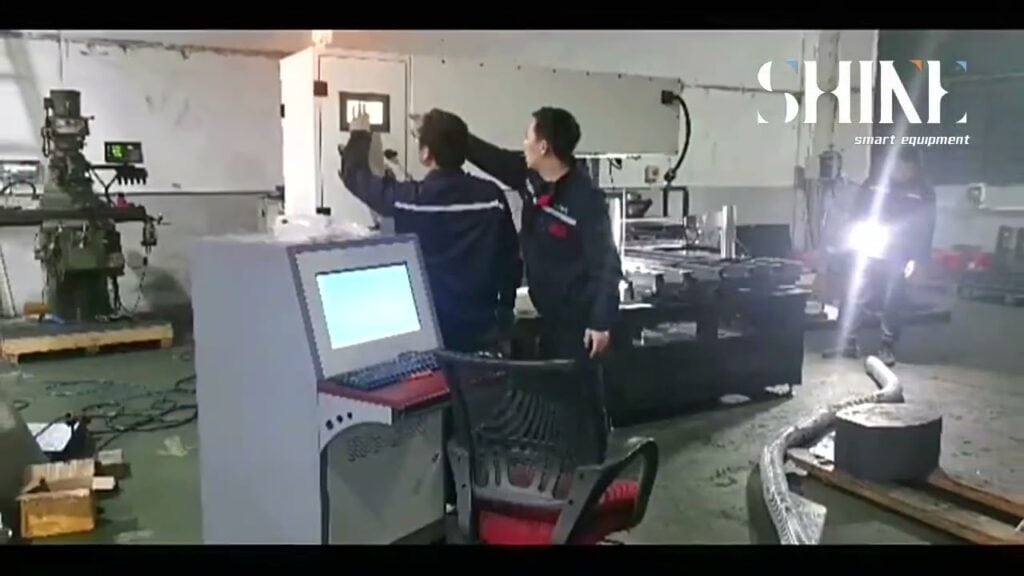
Automation is another area where wire sawing technology has seen significant advancements. Today’s wire saws are often integrated with automated systems that can handle everything from loading and unloading the rods to adjusting the cutting parameters in real-time. This not only speeds up the process but also reduces the margin for human error. Picture a factory floor where robots are seamlessly working alongside humans, each performing their tasks with impeccable accuracy.
Let’s not forget about software innovations. Modern wire saws are often controlled by sophisticated software that can optimize cutting patterns based on the specific requirements of the silicon rods. This software can analyze data in real-time and make adjustments on the fly, ensuring that each cut is optimized for both yield and quality. It’s like having a master craftsman guiding the saw at every step of the process.
To summarize, the latest technological innovations in wire sawing include:
- Diamond-coated wires for enhanced durability and precision.
- Advanced sensors and control systems for micrometer-level precision.
- Automated systems for increased efficiency and reduced human error.
- Sophisticated software for real-time optimization of cutting patterns.
These innovations are transforming the wire sawing industry, making it possible to achieve higher yields and superior quality silicon rods than ever before. As technology continues to evolve, we can only expect these advancements to become even more refined, pushing the boundaries of what’s possible in silicon rod processing.
Improving Yield in Silicon Rod Sawing
When it comes to wire sawing silicon rods, maximizing yield is a top priority. The process can be quite intricate, but with the right strategies, you can significantly reduce waste and boost output. Let’s dive into some effective methods that can help you achieve higher yields during the wire sawing process.
First and foremost, optimizing the wire tension is crucial. Too much tension can cause the wire to break, while too little tension can lead to inaccurate cuts. Finding the perfect balance ensures that the wire remains stable and cuts through the silicon rod efficiently. Regularly monitoring and adjusting the wire tension can make a world of difference.
Another key factor is the selection of the right abrasive slurry. The slurry acts as a lubricant and helps in the cutting process. Using a high-quality slurry with the appropriate particle size can enhance the cutting speed and reduce the amount of silicon wasted. Additionally, maintaining the slurry’s consistency and cleanliness is vital for achieving optimal results.
Implementing advanced automation techniques can also play a significant role in improving yield. Automated systems can precisely control various parameters such as wire speed, feed rate, and tension. This level of control minimizes human error and ensures consistent performance, leading to higher yields.
Here are some practical strategies to improve yield:
- Regular Maintenance: Keeping the wire saw equipment in top-notch condition prevents unexpected breakdowns and ensures smooth operation.
- Precision Alignment: Ensuring that the silicon rods are perfectly aligned with the wire saw can prevent uneven cuts and reduce material loss.
- Optimized Cutting Parameters: Fine-tuning the cutting parameters such as wire speed, feed rate, and slurry flow can lead to more efficient cutting and higher yields.
- Real-time Monitoring: Implementing sensors and monitoring systems to track the cutting process in real-time can help identify and rectify issues promptly.
Moreover, adopting multi-wire sawing technology can significantly enhance yield. This technique involves using multiple wires simultaneously to cut several silicon rods at once. It not only increases the cutting speed but also reduces the overall material waste, leading to a higher yield.
Lastly, training and skill development of the operators cannot be overlooked. Skilled operators who understand the intricacies of the wire sawing process can make informed decisions and adjustments, resulting in better yield outcomes.
By implementing these strategies and continuously refining the process, you can achieve substantial improvements in yield during the wire sawing of silicon rods. Remember, the key lies in paying attention to the finer details and making data-driven decisions.
Enhancing Quality of Cut Silicon Rods
When it comes to achieving the highest quality in cut silicon rods, precision and meticulous attention to detail are paramount. The goal is to ensure that each silicon rod is not only cut to the desired specifications but also maintains its structural integrity and surface quality. So, how do we achieve this? Let’s dive into the techniques and methods that can significantly enhance the quality of cut silicon rods.
First and foremost, minimizing surface damage during the cutting process is crucial. Surface damage can lead to micro-cracks, which can compromise the rod’s performance and longevity. One effective approach to mitigate this is by using diamond-coated wire. Diamond-coated wire provides a smoother cut, reducing the likelihood of surface abrasions and ensuring a more uniform finish.
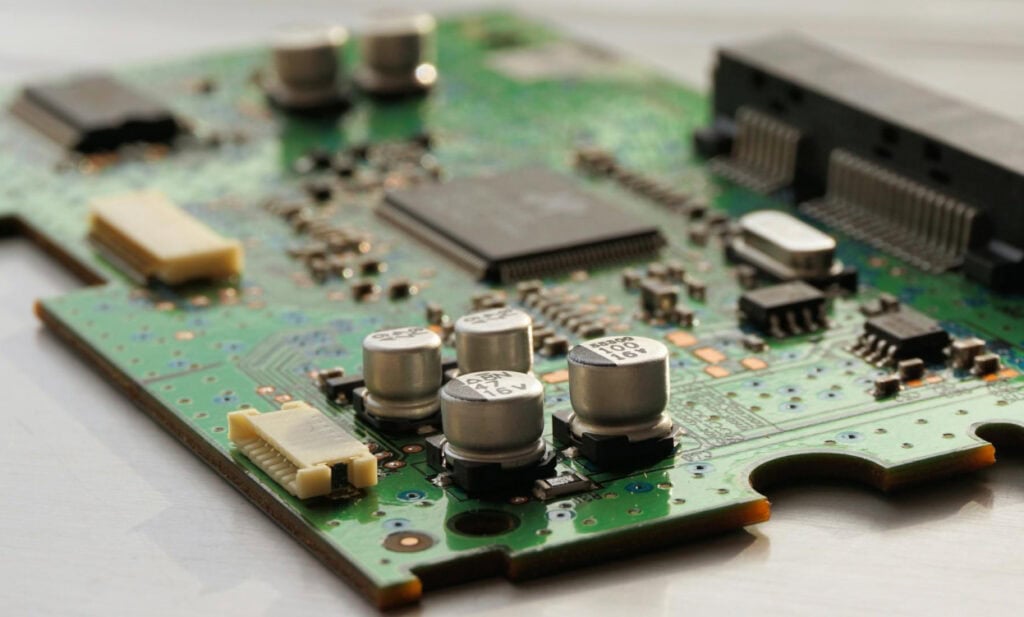
Another key factor in enhancing quality is achieving uniform cuts. Consistency in the cutting process can be maintained through precision control systems. These systems utilize advanced sensors and real-time monitoring to adjust the cutting parameters dynamically. By doing so, they ensure that each cut is as precise as possible, reducing variations and maintaining uniformity.
Moreover, the implementation of cooling and lubrication techniques can play a significant role in improving the quality of the cuts. During the wire sawing process, friction generates heat, which can lead to thermal damage. By employing efficient cooling systems and appropriate lubricants, the temperature can be controlled, minimizing heat-induced damage and ensuring a cleaner cut.
Here are some additional techniques to consider for enhancing the quality of cut silicon rods:
- Optimized Wire Tension: Maintaining the correct tension in the wire is essential for achieving a clean cut. Too much tension can cause the wire to snap, while too little can lead to uneven cuts.
- Advanced Wire Materials: Utilizing high-quality wire materials that are resistant to wear and tear can improve the longevity and effectiveness of the wire sawing process.
- Post-Cut Treatments: Implementing post-cut treatments, such as chemical polishing or annealing, can further enhance the surface quality and structural integrity of the silicon rods.
Incorporating these techniques not only improves the quality of the cut silicon rods but also contributes to the overall efficiency and cost-effectiveness of the wire sawing process. By focusing on precision, uniformity, and surface integrity, manufacturers can ensure that their silicon rods meet the highest standards of quality, ultimately leading to better performance in their applications.
In conclusion, enhancing the quality of cut silicon rods requires a combination of advanced materials, precision control systems, and effective cooling and lubrication techniques. By implementing these strategies, manufacturers can achieve superior cuts, minimize surface damage, and ensure uniformity, ultimately resulting in high-quality silicon rods that meet the stringent demands of modern applications.
Case Studies and Practical Applications
When it comes to wire sawing technology, nothing speaks louder than real-world success stories. Let’s dive into some fascinating case studies and practical applications that showcase the remarkable advancements in this field. These examples not only highlight the effectiveness of advanced wire sawing techniques but also provide valuable insights into their implementation in industrial settings.
Case Study 1: High-Precision Cutting in Solar Panel Manufacturing
In the solar panel industry, precision and efficiency are paramount. A leading solar panel manufacturer recently adopted advanced wire sawing techniques to enhance their production process. By integrating diamond-coated wires and utilizing automated cutting systems, they achieved significant improvements in both yield and quality. The results were astounding:
- Yield Improvement: The new wire sawing technology reduced material waste by 20%, allowing the company to produce more solar wafers from the same amount of silicon rods.
- Quality Enhancement: The precision of the diamond-coated wires minimized surface damage, resulting in smoother and more uniform cuts. This led to higher efficiency and longer lifespan for the solar panels.
This case study demonstrates how advanced wire sawing techniques can revolutionize the solar panel manufacturing process, making it more sustainable and cost-effective.
Case Study 2: Semiconductor Industry Breakthrough
The semiconductor industry relies heavily on high-quality silicon wafers for the production of microchips. A renowned semiconductor manufacturer sought to enhance their wire sawing process to meet the ever-growing demand for smaller and more powerful microchips. By incorporating laser-guided wire sawing technology, they achieved remarkable results:
- Increased Precision: The laser-guided system ensured precise alignment of the wire, resulting in thinner and more uniform cuts. This enabled the production of microchips with higher performance and reduced power consumption.
- Reduced Kerf Loss: The advanced wire sawing technique minimized kerf loss, allowing the manufacturer to maximize the number of wafers obtained from each silicon rod.
This breakthrough not only improved the efficiency of the manufacturing process but also contributed to the development of cutting-edge microchips that power our modern devices.
Practical Application: Medical Device Manufacturing
In the medical device industry, precision and quality are of utmost importance. A leading manufacturer of medical devices, such as pacemakers and implants, implemented advanced wire sawing techniques to enhance their production process. By utilizing ultrasonic-assisted wire sawing, they achieved remarkable outcomes:
- Enhanced Surface Finish: The ultrasonic vibrations reduced surface roughness, resulting in smoother and more biocompatible medical devices.
- Improved Yield: The advanced wire sawing technique minimized material waste, allowing the manufacturer to produce more devices from the same amount of raw material.
This practical application highlights how advanced wire sawing techniques can contribute to the production of high-quality medical devices that improve patient outcomes and quality of life.
Phần kết luận
These case studies and practical applications highlight the transformative potential of advanced diamond wire saw machines across various industries. From solar panel manufacturing and semiconductor production to medical device fabrication, the benefits of precision, efficiency, and quality are undeniable. By adopting these advanced techniques, companies can achieve significant improvements in yield and quality, driving innovation and success in their respective fields.
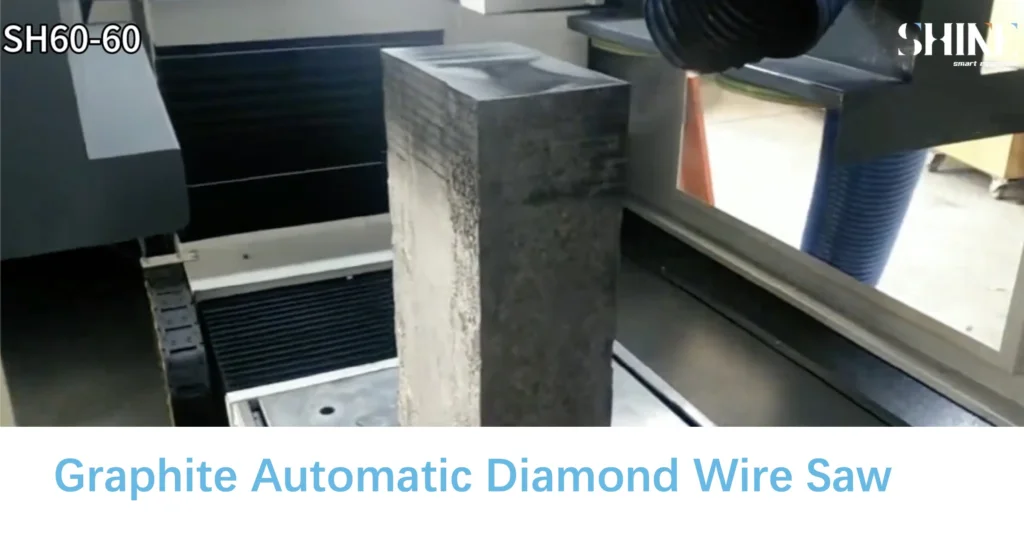
Frequently Asked Questions
- What is wire sawing technology?Wire sawing technology is a method used to cut materials, especially silicon rods, using a wire embedded with abrasive particles. This technique is crucial in the semiconductor industry for producing wafers from silicon rods.
- Why is wire sawing important in silicon rod processing?Wire sawing is important because it allows for precise cuts, minimizes material waste, and ensures high-quality surfaces on the silicon rods. This precision is vital for the production of efficient and effective semiconductor devices.
- What are the latest technological advancements in wire sawing?Recent advancements include the use of new abrasive materials, improvements in wire tension control, and the integration of automation and precision cutting techniques. These innovations enhance both the yield and quality of the silicon rods.
- How can yield be improved during wire sawing of silicon rods?Yield can be improved by optimizing the sawing parameters, such as wire speed and tension, using high-quality abrasive materials, and implementing advanced monitoring systems to reduce errors and waste.
- What techniques are used to enhance the quality of cut silicon rods?Techniques to enhance quality include minimizing surface damage through controlled cutting environments, achieving uniform cuts by using precision-guided wires, and employing post-sawing treatments to smoothen the rod surfaces.
- Can you provide examples of successful implementations of advanced wire sawing techniques?Yes, there are several case studies where companies have successfully implemented advanced wire sawing techniques. These include the use of automated wire saws in semiconductor manufacturing plants, leading to significant improvements in both yield and quality of silicon wafers.
- What are the benefits of using automation in wire sawing?Automation in wire sawing offers numerous benefits such as increased precision, reduced human error, consistent quality, and higher throughput. It also allows for real-time monitoring and adjustments, leading to optimized performance and efficiency.
- How does wire tension affect the sawing process?Wire tension is critical in the sawing process as it influences the cutting accuracy and surface quality. Proper tension ensures a straight cut, reduces wire breakage, and prevents damage to the silicon rod, thereby enhancing overall yield and quality.