When it comes to manufacturing and engineering, the materials and methods we choose can make all the difference. Enter graphite – a material known for its strength, versatility, and conductivity. But how do we shape this wonder material with precision and efficiency? The answer lies in the use of precision wire cutting machines. These innovative tools bring a host of benefits to the table, from enhanced accuracy to increased production efficiency. Let’s dive into the world of wire cutting graphite and discover the advantages that these machines offer.
Imagine trying to cut a complex design out of graphite with traditional methods. The room for error is vast, and the outcome might not always meet expectations. Precision wire cutting machines, however, change the game entirely. They allow for incredibly accurate cuts, down to the minutest detail, ensuring that every graphite component is exactly as it should be. This level of precision is crucial for industries where the smallest discrepancy can have significant consequences, such as in electronics or aerospace.
Time is money, as the saying goes, and in the world of manufacturing, efficiency is key. Precision wire cutting machines significantly speed up the cutting process, allowing for faster production rates without sacrificing quality. This efficiency boost not only helps meet demand more quickly but also contributes to lower operational costs, making it a win-win for businesses.
One of the standout benefits of using precision wire cutting machines for graphite is the superior surface finish they achieve. This is particularly important for components that require minimal friction or need to fit seamlessly with other parts. A smoother finish also reduces the need for additional processing, saving time and resources.
Graphite isn’t just prized for its properties; it’s also notable for its cost. Maximizing material utilization is, therefore, essential. Precision wire cutting machines excel in this area by minimizing wastage. Their accurate cutting ensures that more of the graphite can be used, reducing the amount of material that ends up as scrap. This not only makes the cutting process more cost-effective but also more sustainable.
One size does not fit all, especially in the world of custom manufacturing. The ability to cut complex shapes and sizes with precision is where wire cutting machines truly shine. Whether it’s intricate patterns or unique geometries, these machines can handle a wide range of cutting projects, offering unparalleled flexibility to manufacturers.
Last but certainly not least, the automation of wire cutting machines brings an added layer of safety to the cutting process. By reducing the need for manual handling, the risk of accidents and injuries is significantly lowered. This not only protects workers but also helps maintain a smooth, uninterrupted production flow.
In conclusion, the adoption of precision wire cutting machines for graphite cutting is a game-changer for industries relying on this versatile material. The benefits, from enhanced precision and increased efficiency to improved safety, make a compelling case for their use. As technology advances, we can only expect these machines to become even more integral to the manufacturing landscape.
Enhanced Precision and Accuracy
When it comes to manufacturing components that demand the highest standards of precision, the role of precision wire cutting machines, especially for graphite materials, cannot be overstated. The accuracy and precision these machines offer are pivotal for producing intricate graphite components used across various industries, from aerospace to electronics. But what exactly makes these machines stand out in terms of precision and accuracy?
Firstly, precision wire cutting machines are designed with state-of-the-art technology that allows for control down to the micrometer. This means that every cut, every angle, and every finish is executed with the utmost precision, eliminating human error and ensuring that each component is identical to the last. This level of accuracy is crucial for applications where even the slightest deviation can result in component failure.
Moreover, the precision of these machines is complemented by their capability to consistently produce components with complex geometries and tight tolerances. This is particularly important for graphite, a material known for its brittleness and the challenges it presents in machining. The advanced control systems of wire cutting machines can adjust parameters in real-time, ensuring that the cutting process does not compromise the integrity of the graphite.

- Uniformity in Production: The precision of wire cutting machines ensures that every piece produced is uniform, reducing the need for post-processing and quality control checks.
- Minimized Material Waste: With such high accuracy, material wastage is significantly reduced, as the cutting process can be optimized to make the most out of every graphite block.
- Adaptability to Design Changes: The digital nature of these machines means that design changes can be easily accommodated, allowing for rapid prototyping and adjustments without impacting the precision of the final product.
In conclusion, the enhanced precision and accuracy provided by precision wire cutting machines are not just about meeting the technical specifications of graphite components. It’s about pushing the boundaries of what’s possible in manufacturing, enabling the creation of components that are not only precise but also reliable and efficient. The ripple effect of this precision touches every aspect of production, from reducing waste to ensuring the safety and reliability of the final product. In the realm of graphite machining, precision wire cutting machines are indeed a game-changer.
Increased Production Efficiency
When it comes to the manufacturing world, time is as valuable as gold. This is where precision wire cutting machines step in to revolutionize the efficiency of producing graphite components. Unlike traditional cutting methods, these innovative machines cut down on production time significantly without compromising on quality. But how exactly do they manage to boost efficiency so dramatically? Let’s dive into the mechanics and benefits of using these machines for graphite cutting.
Firstly, the speed at which these machines operate is nothing short of impressive. Precision wire cutting machines are designed to cut through graphite with such finesse and speed that what used to take hours can now be accomplished in minutes. This rapid cutting capability allows manufacturers to increase their output exponentially. Imagine the surge in productivity when tasks that previously bottlenecked production schedules are now completed in a fraction of the time.
Moreover, the precision of these machines means that the first cut is often the only one needed. The accuracy eliminates the need for multiple cuts or corrections, further speeding up the production process. This is particularly important in industries where the dimensions of graphite components must be exact, leaving no room for error.
Another factor contributing to increased production efficiency is the reduction in material wastage. Precision wire cutting machines are so accurate that the amount of graphite wasted during the cutting process is minimized. This not only makes the process more cost-effective but also more sustainable. Less waste means more efficient use of materials, which in turn leads to a smoother, uninterrupted production flow.
- Tốc độ: Drastically reduces cutting time, allowing for faster production cycles.
- Accuracy: Ensures that cuts are precise, reducing the need for rework and further processing.
- Material Conservation: Minimizes waste, promoting cost savings and environmental sustainability.
- Output Increase: With faster and more accurate cuts, overall production output is significantly increased.
In conclusion, the use of precision wire cutting machines in the production of graphite components is a game-changer. The speed, accuracy, and efficiency these machines bring to the table not only enhance production capacity but also contribute to cost savings and material conservation. It’s a win-win situation for manufacturers looking to stay competitive in fast-paced industries. So, if you’re in the business of graphite manufacturing, investing in a precision wire cutting machine could very well be the explosion of efficiency your production line needs.
Improved Surface Finish Quality
One of the standout benefits of using precision wire cutting machines for graphite materials is the significantly improved surface finish quality. Unlike traditional cutting methods that may leave rough edges or require additional finishing processes, precision wire cutting machines achieve a smooth, high-quality surface right off the machine. This not only enhances the aesthetic appeal of the graphite components but also plays a crucial role in their performance, especially in applications where surface smoothness is paramount.
But why does surface finish matter so much, you ask? Well, in the world of manufacturing and engineering, the surface finish can affect everything from friction and wear to corrosion resistance. For graphite components used in electrical discharge machining (EDM), semiconductors, and even aerospace applications, a superior surface finish can mean the difference between a part that performs flawlessly and one that fails prematurely.
Let’s break down how precision wire cutting machines accomplish this feat:
- Controlled Cutting Process: These machines utilize advanced technology to control the cutting process with extreme precision, ensuring that the graphite is cut smoothly without any unnecessary damage to the material.
- Minimized Mechanical Stress: Unlike more aggressive cutting methods, wire cutting exerts minimal mechanical stress on the graphite, preserving its integrity and resulting in a better finish.
- Customizable Settings: Operators can adjust settings such as wire tension, cutting speed, and water flush pressure to suit the specific type of graphite being cut, optimizing the surface finish for each project.
In conclusion, the improved surface finish quality offered by precision wire cutting machines not only makes graphite components more visually appealing but also enhances their functional performance. This leap in quality is a game-changer for industries that rely on the exceptional characteristics of graphite, ensuring that they can achieve the best possible outcomes in their products and applications.
Cost-Effective Material Utilization
When it comes to the cutting and shaping of graphite for industrial applications, precision wire cutting machines stand out for their ability to ensure . Unlike traditional cutting methods, which often result in significant material wastage due to their lack of precision, wire cutting machines are designed to make the most out of every piece of graphite. This not only saves material but also reduces the overall cost of production, making the manufacturing process more sustainable and economically viable.
One of the key features of these machines is their high level of accuracy, which allows for the cutting of graphite into intricate shapes and sizes without the excess offcuts that are common with less precise methods. This accuracy is achieved through the use of advanced technology that controls the wire’s movement to a fraction of a millimeter, ensuring that each cut is exactly as intended. As a result, manufacturers can reduce the amount of graphite that is wasted, which is not only good for the bottom line but also for the environment.
Moreover, the ability to precisely control the cutting process means that less finishing work is required on the final product. This further contributes to material savings, as less graphite is removed during the finishing process. In addition, this level of precision can lead to a reduction in the need for additional materials, such as fillers or coatings, that might otherwise be needed to correct imperfections caused by less accurate cutting methods.
To illustrate the difference precision wire cutting machines can make in terms of material utilization, consider the following comparison:
- Traditional Cutting Methods – Higher material wastage due to less accurate cuts, leading to more offcuts.
- Precision Wire Cutting Machines – Minimized material wastage thanks to highly accurate cuts, resulting in fewer offcuts and a more efficient use of graphite.
In summary, the adoption of precision wire cutting machines for the processing of graphite materials represents a significant step forward in terms of . By reducing wastage, improving accuracy, and minimizing the need for additional finishing work, these machines offer a way to make the production of graphite components both more economical and more environmentally friendly. It’s a win-win situation that benefits manufacturers, consumers, and the planet alike.
Flexibility in Graphite Cutting
The world of graphite manufacturing is one that demands not just precision, but also a high degree of flexibility. This is where precision wire cutting machines truly shine, offering capabilities that can dramatically change the way graphite is cut and used across various applications. Imagine the ability to effortlessly switch from cutting simple flat sheets to intricate 3D shapes without breaking a sweat. That’s the level of flexibility we’re talking about!
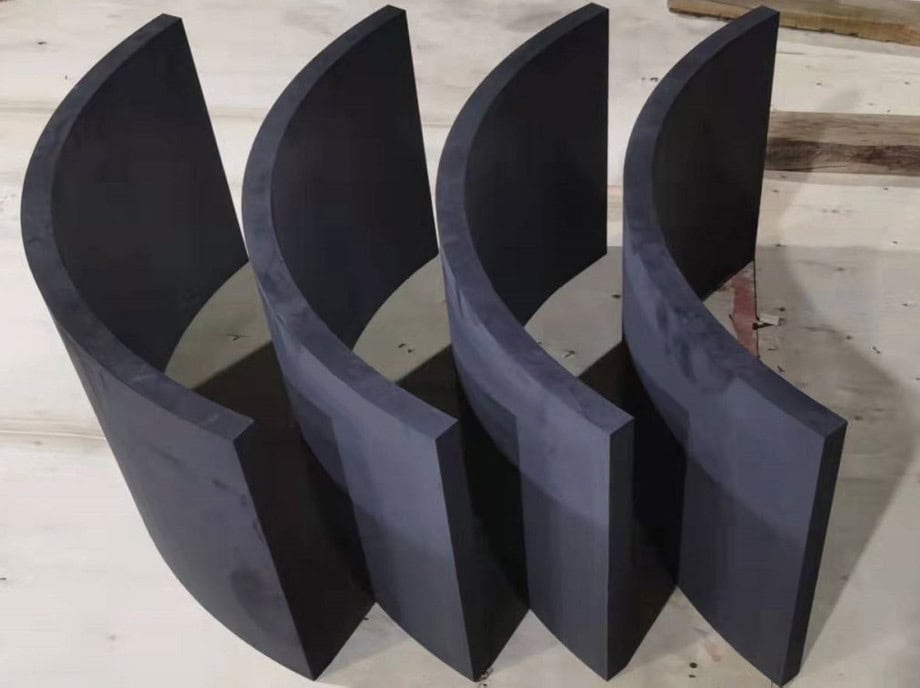
One of the standout features of these machines is their ability to handle complex shapes and sizes with ease. Whether you’re working on small, delicate components for electronic devices or larger parts for industrial applications, precision wire cutting machines can do it all. This adaptability not only expands the range of products that can be manufactured but also opens up new avenues for innovation and design in graphite use.
Moreover, the flexibility of these machines extends to the thickness of the graphite sheets they can cut. From ultra-thin films to thicker blocks, the precision with which these machines operate ensures that each cut is clean, accurate, and exactly what the project requires. This versatility is crucial for meeting the diverse needs of industries relying on graphite for its exceptional properties, such as high temperature resistance, electrical conductivity, and lubricity.
- Hình học phức tạp: The ability to cut intricate designs with precision.
- Variable Sheet Thickness: Accommodates a wide range of graphite sheet thicknesses, from very thin to quite thick.
- Material Efficiency: Reduces waste by maximizing the use of each graphite sheet through precise cutting.
- Quick Setup and Changeover: Fast adjustment settings allow for easy transition between different cutting projects.
In summary, the flexibility offered by precision wire cutting machines in the realm of graphite cutting cannot be overstated. It not only enhances the efficiency and quality of the cutting process but also pushes the boundaries of what can be achieved with graphite materials. By enabling the production of complex shapes and sizes while minimizing waste, these machines play a pivotal role in the advancement of industries that depend on high-quality graphite components.
Enhancing Safety in Operations
When it comes to the cutting of graphite, the traditional methods often involve a significant amount of manual handling, which not only increases the risk of physical injury but also exposes workers to graphite dust, which can be harmful if inhaled over prolonged periods. However, the advent of precision wire cutting machines has been a game-changer in enhancing safety in operations. These high-tech machines automate much of the process, drastically reducing the need for direct contact between the worker and the materials being cut.
One of the key safety features of these machines is their enclosed cutting area. This design minimizes the escape of graphite dust into the surrounding environment, protecting workers from potential respiratory issues. Moreover, the precise control offered by these machines means that the risk of accidental cuts or injuries is significantly lowered. The automation of the cutting process also reduces the physical strain on workers, further enhancing safety.
But how exactly do these machines contribute to a safer working environment? Here’s a closer look:
- Reduced Direct Contact: Automation minimizes the need for manual handling of graphite, reducing the risk of cuts and injuries.
- Dust Control: Enclosed cutting areas help contain graphite dust, protecting workers from respiratory issues.
- Cắt chính xác: High accuracy reduces the chance of accidents caused by the material slipping or being improperly cut.
- Lower Physical Strain: Automated processes decrease the physical demands on workers, reducing the risk of strain injuries.
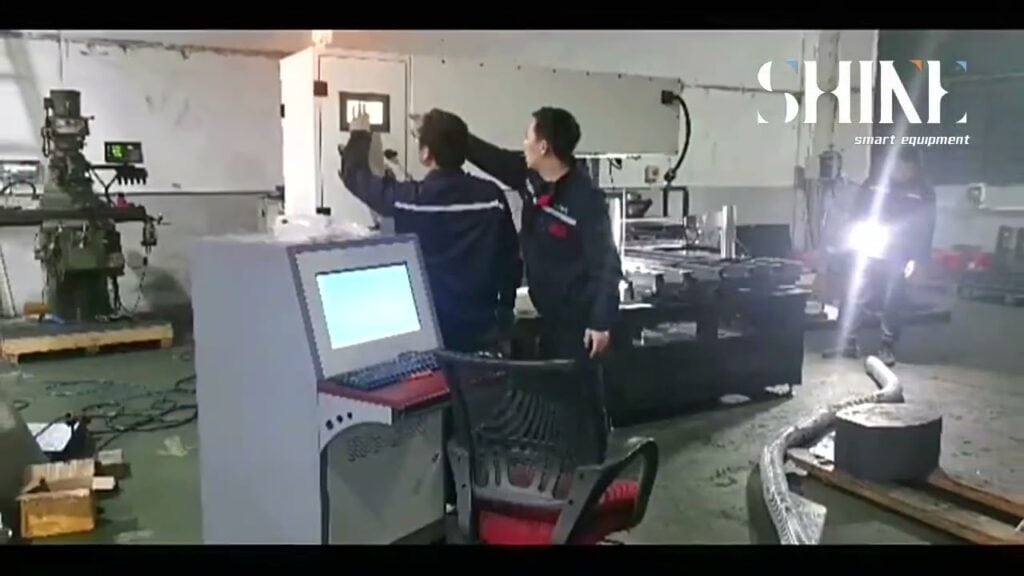
In summary, the use of precision wire cutting machines in the cutting of graphite not only boosts efficiency and quality but also significantly enhances the safety of operations. By reducing direct contact with materials, controlling exposure to graphite dust, and minimizing the physical strain on workers, these machines are instrumental in creating a safer and healthier workplace. As technology continues to advance, we can expect even greater improvements in safety measures, further protecting those who work with graphite on a daily basis.
Frequently Asked Questions
- Why is precision important in wire cutting graphite?Precision is the backbone of wire cutting graphite because it ensures that the intricate components required in various industries like aerospace, electronics, and automotive are cut to exact specifications. This level of accuracy prevents material wastage, ensures the components fit perfectly in their designated places, and maintains the integrity of the design. Imagine trying to fit a square peg in a round hole; that’s what it’s like when precision is off the mark!
- How does using precision wire cutting machines increase production efficiency?Think of precision wire cutting machines as the superheroes of the manufacturing world. They work faster than a speeding bullet, with the ability to make quick, accurate cuts that reduce the time spent on each piece of graphite. This means more products can be manufactured in less time, skyrocketing production efficiency through the roof! Plus, with less material being wasted, you’re not only saving time but also money. It’s a win-win situation.
- Can precision wire cutting machines improve the surface finish of graphite parts?Absolutely! These machines are like skilled artists, carefully sculpting each piece of graphite with the utmost care. The result? A masterpiece with a superior surface finish that enhances the performance of the graphite parts. This smoother finish reduces the need for additional processing, making it ready for use in high-performance applications where every detail matters.
- Why is cost-effective material utilization important in graphite cutting?In the world of manufacturing, every penny counts. By minimizing material wastage, precision wire cutting machines ensure that every bit of graphite is used efficiently. This not only reduces the cost of materials but also supports sustainability efforts. Imagine squeezing every last drop out of a lemon; that’s how these machines treat graphite, ensuring nothing goes to waste.
- How do precision wire cutting machines offer flexibility in cutting graphite?These machines are like the contortionists of the manufacturing world, offering unparalleled flexibility to handle complex shapes and sizes with ease. Whether you need a component that’s as intricate as a spider’s web or as simple as a straight line, these machines can do it all, ensuring your graphite cutting project meets all its specifications with agility and precision.
- How do automated wire cutting machines enhance safety in operations?By taking the manual handling out of the equation, automated wire cutting machines significantly reduce the risk of injuries on the shop floor. It’s like having a guardian angel watching over the workers, ensuring they can focus on their tasks without worrying about the dangers associated with manual graphite cutting. Safety first, always!