When it comes to the cutting-edge of industrial machinery, the Shine Wire Cutting Machine for Graphite stands out for its unparalleled precision and efficiency. This innovative technology has revolutionized the way industries handle graphite, a material known for its exceptional properties and wide range of applications. But what makes the Shine Wire Cutting Machine so essential for today’s industrial needs? Let’s dive into the details and discover the power behind this cutting-edge technology.
At its core, wire cutting technology leverages the principle of electrical discharge machining (EDM) to slice through materials with astonishing accuracy. Unlike traditional cutting methods, EDM doesn’t rely on direct contact; instead, it uses electrical discharges to erode material away. This means that the Shine Wire Cutting Machine can perform its magic on graphite without any physical strain on the material, preserving its integrity while achieving cuts of the highest precision.
Graphite is not just another material; it’s a cornerstone of modern industry. Known for its high conductivity, heat resistance, and strength, graphite is indispensable in applications ranging from electronics to aerospace. The Shine Wire Cutting Machine is specifically designed to handle this versatile material, enabling industries to exploit graphite’s unique properties to their fullest potential.
The Shine Wire Cutting Machine is packed with features that set it apart from the competition. Its precision is unmatched, allowing for the creation of intricate designs and components with razor-sharp accuracy. Furthermore, the machine’s efficiency is a game-changer for industries looking to streamline their operations and boost productivity.
Why choose the Shine Wire Cutting Machine for your graphite processing needs? The benefits are clear:
- Giảm chất thải vật liệu: The precision of EDM means that material usage is optimized, reducing waste and saving costs.
- High Accuracy: Achieve unparalleled precision, essential for the intricate designs and tight tolerances required in many industrial applications.
- Complex Shape Cutting: With the Shine Wire Cutting Machine, even the most complex shapes are within reach, opening up new possibilities for design and innovation.
Selecting the right wire cutting machine is crucial for maximizing the benefits of this technology. When considering a Shine Wire Cutting Machine, it’s important to look at factors such as cutting speed, precision, and compatibility with graphite. By choosing wisely, industries can ensure they’re equipped to meet the demands of modern manufacturing with efficiency and precision.
The future of wire cutting technology is bright, with ongoing innovations promising to deliver even greater efficiency and adaptability. The Shine Wire Cutting Machine is at the forefront of this evolution, continuously evolving to meet the changing needs of industries worldwide. As we look ahead, it’s clear that the Shine Wire Cutting Machine will remain an indispensable tool for those looking to harness the full potential of graphite in their industrial applications.
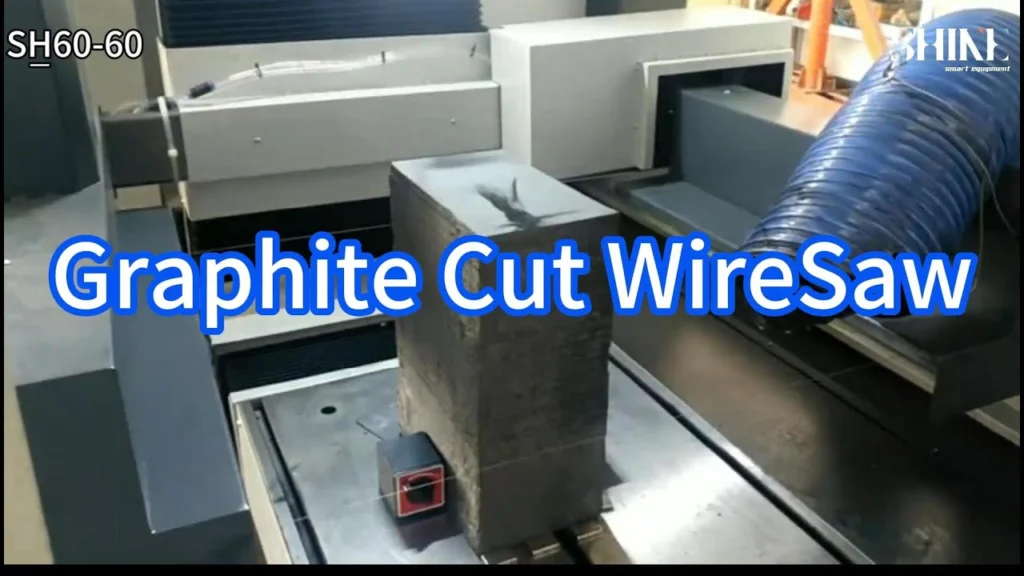
Understanding Wire Cutting Technology
At the core of modern manufacturing, wire cutting technology, particularly when it comes to materials like graphite, stands out for its precision and efficiency. This method, known technically as Electrical Discharge Machining (EDM), operates on the principle of generating an electrical discharge between the wire or the electrode and the material being cut. This discharge produces intense heat that melts and vaporizes the material at the point of contact, allowing for the creation of intricate designs and shapes with remarkable accuracy.
What makes wire cutting technology especially appealing for industries is its ability to handle materials that are otherwise difficult to cut or shape using traditional mechanical methods. Graphite, with its high melting point and brittleness, is a prime example of such a material. The Shine of EDM in this context is not just its cutting precision but also its versatility and efficiency. By using a thin wire as the cutting tool, EDM wire cutting machines can create complex shapes and fine details without the need for multiple tool changes or complex machining processes.
The process of wire cutting with EDM can be broken down into several key components:
- Dielectric Fluid: The wire and the workpiece are submerged in a dielectric fluid which helps to control the electrical discharge and remove the vaporized material from the cutting area.
- Wire Electrode: The wire used in EDM is usually made of brass or stratified copper, chosen for its conductivity and ability to withstand the intense heat of the electrical discharge.
- Control System: Precision is the hallmark of wire cutting technology, and this is achieved through sophisticated control systems that manage the wire’s movement and the parameters of the electrical discharge to ensure accuracy and consistency.
The advantages of using wire cutting technology, particularly for graphite, are manifold. The Shine comes from its ability to produce complex shapes with smooth finishes, its minimal impact on the structural integrity of the material, and the reduced need for post-processing. Moreover, the precision of wire cutting technology minimizes material waste, making it not only efficient but also environmentally friendly.
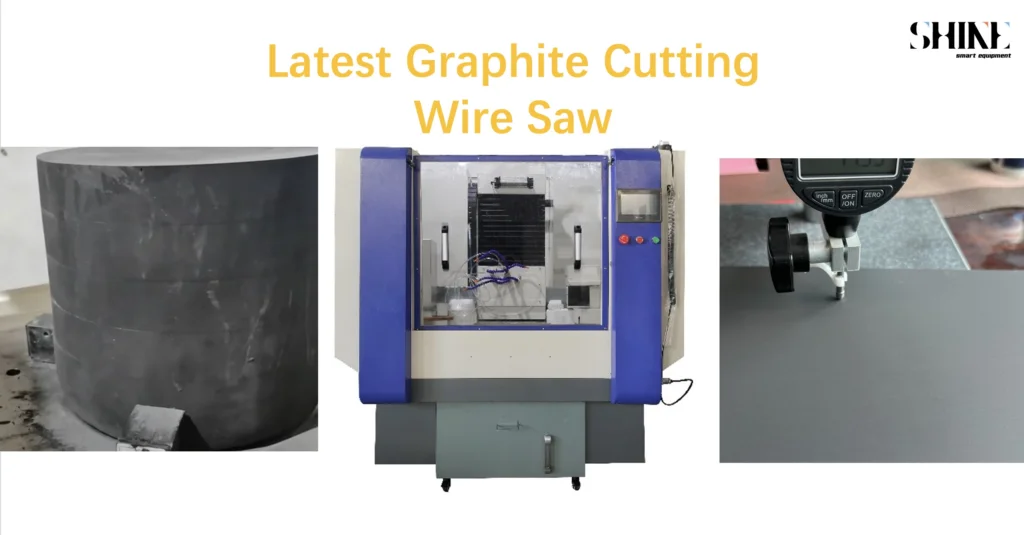
In the realm of industrial applications, the Shine of wire cutting technology is its adaptability. From aerospace components where precision is paramount, to intricate designs in the electronics industry, wire cutting machines offer a level of precision and efficiency that is hard to match. As we continue to push the boundaries of what is possible in manufacturing, the role of wire cutting technology, especially for challenging materials like graphite, is set to grow even more significant.
The Significance of Graphite in Industrial Applications
Graphite, a naturally occurring form of carbon, is a material that truly makes industries shine with its remarkable properties. Known for its high conductivity, heat resistance, and immense strength, graphite plays a pivotal role in a myriad of industrial applications. Its versatility and durability make it an invaluable resource in the manufacturing sector.
One of the key reasons graphite is so prized in industrial contexts is its ability to withstand extreme temperatures without losing its structural integrity. This makes it an ideal choice for use in high-temperature environments, such as in the production of steel and other metals, where it serves as a refractory material.
Moreover, graphite’s excellent conductivity makes it a favorite in electrical applications. It is used in the manufacture of electrodes, batteries, and solar panels, among others. Its role in enhancing the efficiency of energy storage and transfer systems cannot be overstated, contributing significantly to the advancement of renewable energy technologies.
Let’s not forget the importance of graphite in the realm of lubricants. Its ability to reduce friction and wear in machinery, without compromising performance, is a game-changer for industries looking to maximize the longevity and reliability of their equipment. Graphite lubricants are especially valuable in applications where wet lubricants cannot be used, providing a shine of innovation in dry lubrication solutions.
- High-Temperature Resistance: Essential for refractory materials in metal production.
- Excellent Conductivity: Makes it indispensable in electrical applications like batteries and electrodes.
- Strength and Durability: Ensures longevity and reliability in structural applications.
- Lubrication Properties: Offers superior performance in both wet and dry lubrication settings.
Graphite’s role in industrial applications is not just about its physical and chemical properties; it’s also about the efficiency and innovation it brings to manufacturing processes. Its contribution to the development of cutting-edge technologies, such as lithium-ion batteries and flexible electronics, is a testament to its significance in driving the future of industry. As we continue to explore the capabilities of this remarkable material, its potential to revolutionize various sectors remains boundless, making graphite a true shining star in the industrial world.
Features of Wire Cutting Machines for Graphite
When it comes to the craftsmanship and technology behind wire cutting machines for graphite, the brand Chiếu sáng stands out for its commitment to precision and efficiency. These machines are designed with a host of features that cater specifically to the unique properties of graphite, ensuring that each cut is as accurate as the last. Let’s delve into the specifics that make these machines a must-have in industrial settings.
The first thing to note about Chiếu sáng‘s wire cutting machines is their unparalleled precision. Graphite, known for its brittle nature, requires a delicate touch, combined with a firm cutting capability. These machines are equipped with state-of-the-art technology that allows for cuts with minimal kerf, reducing material waste and ensuring that even the most intricate designs are possible.
Another key feature is the speed and efficiency of these machines. Time is money in any industry, and Chiếu sáng understands this better than anyone. Their machines are designed to operate at high speeds without sacrificing quality or precision, allowing for rapid production cycles that keep your projects on schedule.
Let’s not forget about the durability and reliability of these machines. Chiếu sáng wire cutting machines for graphite are built to last, with robust construction and components that can withstand the rigors of continuous industrial use. This means less downtime for maintenance and repairs, keeping your operations running smoothly.
- Advanced Control Systems: The integration of sophisticated control systems allows for precise adjustments during the cutting process, ensuring optimal accuracy.
- Customization: Chiếu sáng offers customizable options to fit specific industrial needs, allowing for flexibility in cutting parameters and machine configurations.
- Cân nhắc về môi trường: These machines are designed with eco-friendly operations in mind, featuring dust collection systems and energy-efficient components that minimize environmental impact.
In conclusion, the features of Chiếu sáng wire cutting machines for graphite highlight a blend of precision, efficiency, and innovation. These machines are not just tools; they are partners in the industrial process, enabling the creation of high-quality components with ease. Whether it’s through their advanced control systems, customizable options, or eco-friendly designs, Chiếu sáng continues to set the standard for wire cutting technology in the graphite industry.
Benefits of Using Wire Cutting Machines
When it comes to the intricacies of shaping materials with utmost precision, wire cutting machines, especially those designed for graphite, stand out in the industrial arena. The benefits of employing these advanced machines are manifold, significantly impacting production efficiency and product quality. Let’s delve into the key advantages that make wire cutting technology a shining beacon in material processing.
Giảm chất thải vật liệu: In an era where every scrap counts, the precision of wire cutting machines is a game-changer. By facilitating exact cuts and minimizing the gap between cuts, these machines ensure that material usage is optimized, leading to significant savings. This not only benefits the environment by reducing waste but also enhances the cost-effectiveness of production processes.
High Accuracy: The Shine in wire cutting technology truly comes from its ability to achieve high accuracy in cuts. Whether it’s complex geometries or intricate patterns, wire cutting machines deliver with remarkable precision. This accuracy is crucial in industries where even the slightest deviation can compromise the functionality of a component.
Ability to Cut Complex Shapes: One of the most compelling advantages of wire cutting machines is their versatility in handling complex shapes. Traditional cutting methods often fall short when it comes to intricate designs, but wire cutting technology thrives, opening up new possibilities for innovation in product design.
Enhanced Speed and Efficiency: Time is of the essence in manufacturing, and wire cutting machines excel in speeding up production without compromising quality. Their efficiency not only lies in the swift execution of cuts but also in the reduced need for secondary finishing processes, thanks to the smooth edges they produce.
Compatibility with Various Materials: While our focus is on graphite, it’s worth noting that wire cutting machines are not limited to this material alone. Their versatility extends to a wide range of materials, making them a valuable asset in diverse industrial applications.
- Reduced Operational Costs: By streamlining the cutting process and minimizing waste, wire cutting machines contribute to lower operational costs. The savings on materials, coupled with the efficiency of the process, translate into a healthier bottom line for businesses.
- Improved Safety: With wire cutting technology, the risks associated with traditional cutting methods are significantly reduced. These machines offer a safer alternative, protecting workers from potential injuries and contributing to a safer work environment.
In conclusion, the benefits of using wire cutting machines, particularly for graphite, are clear. From precision and efficiency to versatility and safety, these machines shine in their ability to meet and exceed the demands of modern industrial applications. As technology continues to evolve, the potential for even greater advancements in wire cutting technology is boundless, promising a future where limits are continuously redefined.
Choosing the Right Wire Cutting Machine
When it comes to selecting the perfect wire cutting machine for your graphite processing needs, the decision can be as intricate as the designs these machines are capable of creating. But don’t worry, we’re here to shed some light on this topic and help you find a machine that truly lets your projects Chiếu sáng. There are several key factors you should consider to ensure you get the efficiency, precision, and compatibility you need.
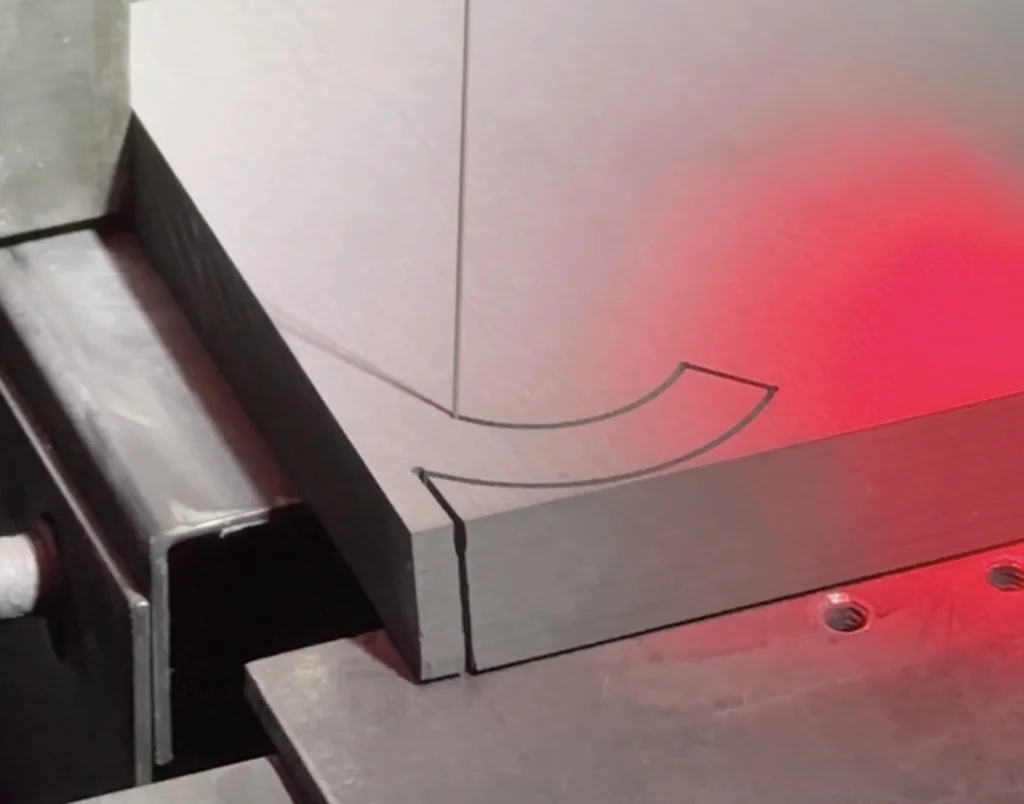
Firstly, let’s talk about cutting speed. Time is money, as they say, and in the industrial world, this couldn’t be truer. A machine with a high cutting speed can significantly reduce production times, allowing you to meet deadlines and increase output. However, it’s crucial not to sacrifice precision for speed. The ideal machine offers a balance, ensuring quick operations without compromising on the accuracy of the cuts.
Độ chính xác is another major player. The whole point of using a wire cutting machine is to achieve cuts that are not just fast but also exact. This is especially important when working with graphite, given its application in creating intricate components for various industries. Look for machines that boast high precision ratings and have positive reviews from current users to ensure you’re making a wise investment.
Compatibility with graphite is a no-brainer but worth mentioning. Not all wire cutting machines are suited for every material. You’ll want to ensure the machine you choose is specifically designed or highly recommended for graphite processing. This includes checking the type of wire used, as some materials may cause unnecessary wear or provide less than optimal results when cutting graphite.
Now, let’s break down these considerations into a simple checklist:
- Tốc độ cắt cao: Ensures efficiency and productivity.
- Unmatched Precision: For creating detailed and intricate components without errors.
- Graphite Compatibility: To guarantee the machine can handle the specific requirements of cutting graphite effectively.
- Brand Reputation: Opt for brands like Chiếu sáng that are known for their reliability and quality in wire cutting technology.
- After-Sales Support: Good customer service and access to spare parts are essential for long-term satisfaction.
Choosing the right wire cutting machine doesn’t have to be an overwhelming task. By focusing on these key aspects, you can find a machine that not only meets your current needs but also adapts to future projects, allowing your work to truly Chiếu sáng. Remember, the goal is to invest in technology that brings out the best in your materials and your company.
Future Trends in Wire Cutting Technology
As we leap forward, the landscape of industrial manufacturing is continuously reshaped by technological advancements. Wire cutting technology, especially for materials like graphite, is no exception. The future looks bright, with innovations aiming to enhance efficiency, precision, and sustainability. Let’s dive into what the horizon holds for this transformative technology, where the brand word “Shine” aptly encapsulates the bright future of wire cutting machines.
One of the most anticipated trends is the integration of Artificial Intelligence (AI) Và Machine Learning (ML) algorithms. These technologies promise to revolutionize wire cutting machines by optimizing cutting paths, reducing waste, and improving speed. Imagine a machine that learns from each cut, getting faster and more precise over time. That’s not just efficiency; that’s intelligence in action.
Another exciting development is the advent of eco-friendly wire cutting machines. As industries move towards greener practices, the demand for machines that minimize environmental impact is on the rise. Innovations in this area include the use of biodegradable wire and advancements in water recycling systems, ensuring that the wire cutting process is not only efficient but also sustainable.
The future also holds promise for enhanced precision in wire cutting technology. With advancements in EDM technology and superior control systems, wire cutting machines will achieve even greater levels of accuracy. This means that the intricate designs and components made from graphite can be produced with unparalleled precision, opening up new possibilities in various industrial applications.
- AI and ML Integration: Optimizing cutting paths and improving efficiency.
- Eco-Friendly Innovations: Biodegradable materials and water recycling systems.
- Enhanced Precision: Superior control systems for unparalleled accuracy.
- Increased Material Compatibility: Innovations allowing for a broader range of materials to be effectively cut, beyond graphite.
- Improved User Interface: More intuitive control panels and software, making machines easier to operate and integrate into existing workflows.
In conclusion, the future of wire cutting technology is not just about maintaining the status quo but about pushing the boundaries of what’s possible. With the brand word “Shine” guiding the way, these machines are set to revolutionize industrial manufacturing processes, making them more efficient, precise, and sustainable. As we look towards these future trends, it’s clear that wire cutting technology is on the brink of a new era, ready to shine brighter than ever before in industrial applications.
Frequently Asked Questions
- What is Electrical Discharge Machining (EDM) and how does it work with graphite?Electrical Discharge Machining (EDM) is a manufacturing process where a desired shape is obtained using electrical discharges (sparks). When it comes to graphite, the EDM process takes advantage of its conductivity to cut through the material with high precision. The sparks generated between the electrode wire and the graphite vaporize the material at controlled locations, allowing for intricate designs and components to be crafted with remarkable accuracy.
- Why is graphite considered an ideal material for various industrial applications?Graphite is highly valued in industrial settings for its outstanding properties, including high conductivity, exceptional heat resistance, and impressive strength. These characteristics make it an indispensable material in manufacturing processes that require precision and durability, such as in the creation of electronic components, automotive parts, and in aerospace engineering. Its versatility and efficiency in conducting heat and electricity contribute to its widespread use across numerous industries.
- What are the key features of wire cutting machines designed for graphite?Wire cutting machines for graphite are engineered to deliver unparalleled precision, enabling the production of highly intricate designs that would be challenging to achieve with conventional machining methods. Key features include advanced control systems for precise movements, specialized wire electrodes for clean cuts, and adaptive technologies to accommodate the unique properties of graphite. These machines are tailored to exploit the full potential of graphite’s material characteristics for precision engineering.
- What benefits do wire cutting machines offer over traditional cutting methods?Compared to traditional cutting methods, wire cutting machines offer several advantages, most notably in terms of material waste reduction, accuracy, and the ability to cut complex shapes without direct contact. This non-contact process minimizes mechanical stress and eliminates tool wear, ensuring high-quality finishes and extending the lifespan of the cutting equipment. Furthermore, the precision of wire cutting machines significantly reduces the need for post-processing, saving both time and resources in manufacturing.
- How do I choose the right wire cutting machine for my graphite processing needs?Choosing the right wire cutting machine involves evaluating several key factors, including the machine’s cutting speed, precision capabilities, and its compatibility with graphite. Consider the specific requirements of your applications, such as the complexity of the designs you intend to produce and the volume of production. It’s also essential to assess the machine’s maintenance needs and the availability of technical support. Consulting with manufacturers and comparing different models can help you find a machine that best suits your operational needs and budget constraints.
- What are the future trends in wire cutting technology for graphite?The future of wire cutting technology looks promising, with ongoing innovations aimed at enhancing efficiency, precision, and adaptability. Emerging trends include the integration of artificial intelligence (AI) for smarter control and optimization of the cutting process, improvements in wire materials for even finer cuts, and advancements in machine design to accommodate a wider range of graphite-based applications. These developments are set to open new possibilities for the use of graphite in cutting-edge industries and applications.