Keywords: High-pressure water-abrasive cutting, ASWJ, material cutting, precision technology
Table of Contents
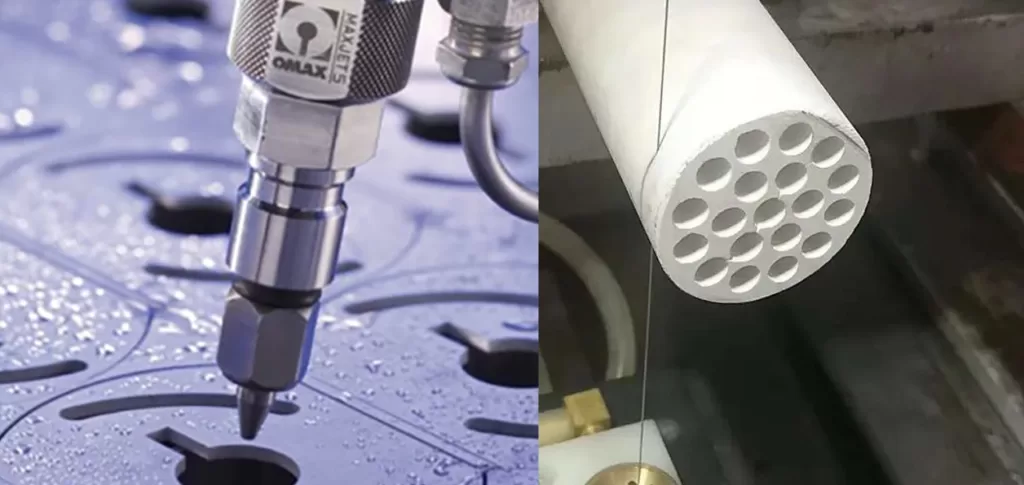
Introduction
In modern manufacturing and engineering, efficient material cutting technology is crucial for producing high-quality products. High-Pressure Water-Abrasive Cutting (ASWJ) is an increasingly prominent precision cutting technique that demonstrates excellence in various fields. This article delves into the working principles, advantages, and a comparative analysis of ASWJ against other cutting technologies.
Working Principles of High-Pressure Water-Abrasive Cutting
High-pressure water-abrasive cutting utilizes a mixture of fluids to cut materials. In this process, high-pressure water is mixed with hydrogen and abrasive material to create a high-velocity jet stream. This jet stream contains substantial energy and is capable of cutting various materials, including metals, ceramics, and plastics. The addition of abrasive material enhances cutting efficiency, resulting in faster cutting speeds.
Advantages of High-Pressure Water-Abrasive Cutting
ASWJ offers several notable advantages, including:
- Precision Cutting: ASWJ achieves cutting precision at the micron level, making it ideal for applications that demand a high degree of accuracy, such as microelectronics manufacturing.
- Material Versatility: This technology can cut a wide range of materials, from soft rubber to hard ceramics, proving its versatility.
- Cold Cutting: Unlike traditional hot cutting methods, ASWJ is a cold-cutting process, reducing the risk of material distortion due to thermal stress.
- Eco-Friendly: ASWJ is relatively environmentally friendly, as it does not require chemical additives and does not produce harmful waste materials.
- High Speed and Efficiency: The high-velocity jet stream, combined with the abrasive material, makes ASWJ more efficient in certain scenarios compared to other cutting techniques.
Disadvantages of High-Pressure Water-Abrasive Cutting (ASWJ)
Despite its advantages, ASWJ is not without its limitations, including:
- Complex Setup: Implementing ASWJ technology can be intricate, requiring specialized equipment and a well-controlled environment. This complexity can make it challenging to set up for smaller operations.
- Abrasive Consumption: ASWJ uses abrasive materials in its cutting process. These abrasives wear down over time, leading to the need for frequent replenishment, increasing operational costs.
- Maintenance: The high-pressure pumps and nozzles used in ASWJ systems require regular maintenance to ensure optimal performance. This maintenance can be costly and time-consuming.
- Safety Concerns: ASWJ involves working with high-pressure fluids, which can be dangerous if not handled correctly. Operators need training to ensure safe and efficient operation.
- Limited to Conduction Materials: ASWJ is primarily suitable for conductive materials. It may not be the best choice for cutting non-conductive materials.
- Potential Erosion: Over time, the high-speed jet stream can cause wear and tear on the cutting equipment, leading to potential erosion and degradation of precision.
It’s essential for manufacturers and businesses to consider these disadvantages alongside ASWJ’s advantages to determine its suitability for their specific applications and projects.
Comparative Analysis: ASWJ vs. Other Cutting Technologies
While ASWJ is an efficient cutting technology, it has limitations when compared to other cutting methods. In contrast, closed diamond wire cutting uses wire embedded with tiny diamond particles to perform cutting and possesses several distinguishing characteristics:
- Material Adaptability: Similar to ASWJ, closed diamond wire cutting can cut various materials, including non-conductive materials.
- High Precision: Like ASWJ, it provides high-precision cutting, but it excels at cutting extremely thin materials.
- Speed: Closed diamond wire cutting is faster than ASWJ, allowing it to complete cutting tasks in shorter timeframes.
- Reduced Waste: Due to its wire-cutting method, closed diamond wire cutting minimizes material wastage, enhancing sustainability.
Applications of High-Pressure Water-Abrasive Cutting
ASWJ finds applications across numerous fields, including:
- Aerospace Industry: Cutting aircraft components and engine parts.
- Medical Sector: Essential for manufacturing medical equipment and surgical tools.
- Automobile Manufacturing: Cutting and processing automobile parts, including body and engine components.
- Construction: Cutting construction materials such as stone, steel structures, and concrete.
- Electronics Manufacturing: Providing precision cutting for circuit boards and semiconductor production.
- Art and Creativity: Enabling creative work in art, sculpture, and decorative fields.
Applications for Challenging Materials
In challenging cutting tasks, such as handling hard ceramics, ASWJ shines with its high precision and material adaptability, ensuring high-quality cutting results.
Conclusion
High-Pressure Water-Abrasive Cutting (ASWJ) stands as an efficient and precise material cutting technology, applicable to various materials and fields. Its high precision, material adaptability, and environmental friendliness make it vital in manufacturing, medical applications, and artistic endeavors. However, each cutting technology possesses its strengths and limitations, necessitating wise decisions based on specific requirements when selecting the appropriate method for any given task.