Keywords: waterjet cutting, ring diamond wire cutting, modern cutting technologies, material processing
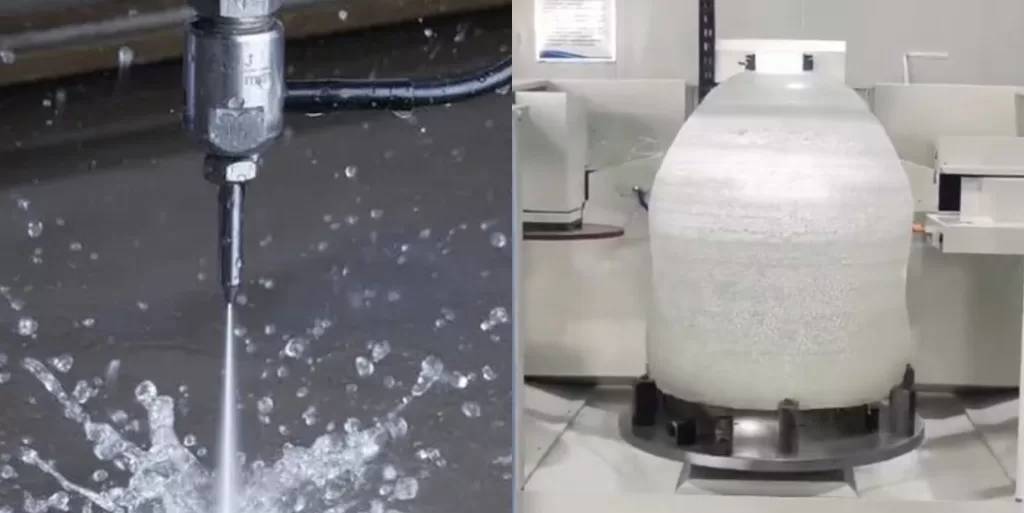
Table of Contents
Introduction
In modern manufacturing, cutting technology is of paramount importance. Waterjet cutting and ring diamond wire cutting are two highly acclaimed methods. This article delves deep into the distinctions between these two techniques and their applications across various domains.
Waterjet Cutting: The Marvel of Water
Waterjet cutting is an exceptional technology that employs high-speed, high-pressure jets of water to cut through a wide array of materials, shaping them as needed. Below are the characteristics and advantages of waterjet cutting:
- Material Versatility: Waterjet cutting is compatible with various materials, including metals, plastics, rubber, and composite materials. This versatility makes it widely applicable across numerous industries.
- Low Heat Impact: Waterjet cutting is a cold processing technique, meaning it doesn’t generate heat, thus preserving the integrity of materials.
- High Precision: Waterjet cutting can achieve high-precision cutting, making it suitable for applications that demand utmost accuracy, such as artistry and precision component manufacturing.
- Environmental Considerations: However, it’s important to note that waterjet cutting introduces abrasive particles into the cutting process, which could lead to water pollution. Thus, it necessitates proper wastewater treatment and filtration measures to ensure eco-friendliness and sustainability.
Main appilcation of water jet
Water jet cutting is a versatile technology that finds applications in various industries due to its ability to cut a wide range of materials accurately. Some of the main applications of water jet cutting include:
- Metal Fabrication: Water jet cutting is commonly used in metal fabrication to cut materials like steel, aluminum, and stainless steel. It provides high precision and can cut complex shapes in metal.
- Aerospace: In the aerospace industry, water jet cutting is used to cut parts for aircraft, such as panels and brackets, with minimal heat-affected zones and distortion.
- Automotive: Water jet cutting is employed to cut automotive components, including dashboards, gaskets, and interior trims. It is also used to cut thicker materials like metal for vehicle frames.
- Glass and Stone: Water jet cutting is ideal for cutting fragile materials like glass and stone. It is used for creating decorative patterns, custom tiles, and architectural designs.
- Gaskets and Seals: Water jet cutting is commonly used in the manufacturing of gaskets and seals from materials like rubber, foam, and composites.
- Food Industry: In the food industry, water jet cutting is used to cut food products, such as vegetables, meats, and baked goods, with precision and cleanliness.
- Art and Design: Artists and designers use water jet cutting to create intricate and detailed sculptures, signage, and decorative elements in various materials.
- Medical Devices: Water jet cutting is employed in the medical field to cut materials for surgical instruments, orthopedic implants, and medical devices
Ring Diamond Wire Cutting: Precision Diamond Power
Ring diamond wire cutting, on the other hand, is an emerging technology that employs a novel cutting approach using a fine wire embedded with tiny diamond particles to cut through materials. This technology finds wide applications in various domains, including semiconductor manufacturing, optical glass shaping, and solar cell production. Below are the characteristics and advantages of ring diamond wire cutting:
- Material Versatility: Ring diamond wire cutting exhibits remarkable versatility, effortlessly cutting both conductive and non-conductive materials, making it an indispensable tool across industries.
- High Efficiency: Compared to traditional cutting techniques, ring diamond wire cutting is faster and produces higher-quality results. It’s not limited by material size, significantly enhancing cutting efficiency.
- Reduced Material Waste: Ring diamond wire cutting aids in reducing material wastage, a crucial aspect of manufacturing sustainability.
- Non-conductive Material Cutting: Differing from traditional electrical discharge machining (EDM) wire cutting, ring diamond wire cutting doesn’t require electricity. This means it can cut non-conductive materials, further expanding its application scope.
Waterjet Cutting and Ring Diamond Wire Cutting: Coexistence’s Beauty
Waterjet cutting and ring diamond wire cutting represent combinations of different principles and methods. Waterjet cutting involves high-pressure hydro-cutting and is particularly suitable for cold cutting and processing a variety of materials. In contrast, ring diamond wire cutting employs microscopic diamond particles to achieve high precision and efficient cutting, ideal for non-conductive materials. Both of these technologies profoundly impact diverse fields and are shaping the future of modern manufacturing.
Conclusion
The continuous evolution of cutting technology propels progress in modern manufacturing. Waterjet cutting and ring diamond wire cutting, although employing different methods, both offer efficient, precise, and sustainable cutting solutions. As technology advances, these two methods will play pivotal roles in various fields, creating more opportunities and possibilities. The future of modern cutting technology is an exciting journey, where the power of water and the precision of diamonds lead us to new heights.