Are you struggling to navigate the complexities of wire cutting machines? Do you find yourself overwhelmed by the myriad options available in the market? In this guide, we’ll delve into the world of wire cut machines, shedding light on their functionalities, advantages, and key considerations for choosing the right one for your needs. Whether you’re a seasoned manufacturer or a newcomer to the industry, this comprehensive guide will equip you with the knowledge and insights you need to make informed decisions and maximize the potential of wire cut machines.
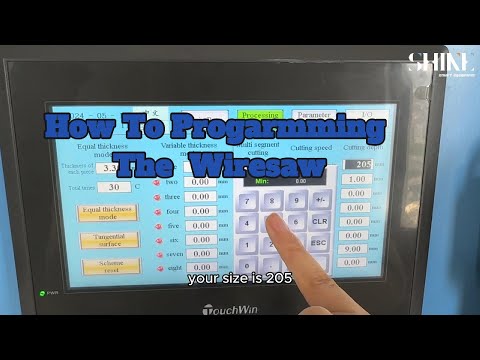
Wire cutting machines play a crucial role in modern manufacturing, offering unparalleled precision and efficiency in shaping various materials. From wire cutting machines for general applications to specialized solutions such as diamond wire cutting, the market is replete with options catering to diverse needs and preferences. Join us as we explore the intricacies of wire cutting machines, uncovering their inner workings and highlighting the benefits they bring to manufacturing processes.
What is an EDM Wire Cut Machine?
An EDM (Electrical Discharge Machining) wire cut machine is a specialized tool used in manufacturing processes to precisely cut and shape materials. It utilizes electrical discharges to erode material from a workpiece, creating intricate shapes with high precision.
In EDM wire cutting, a thin wire electrode, usually made of brass or copper, is fed through the workpiece while an electrically charged pulse generates sparks between the wire and the workpiece. These controlled sparks melt and vaporize material from the workpiece, creating the desired shape.
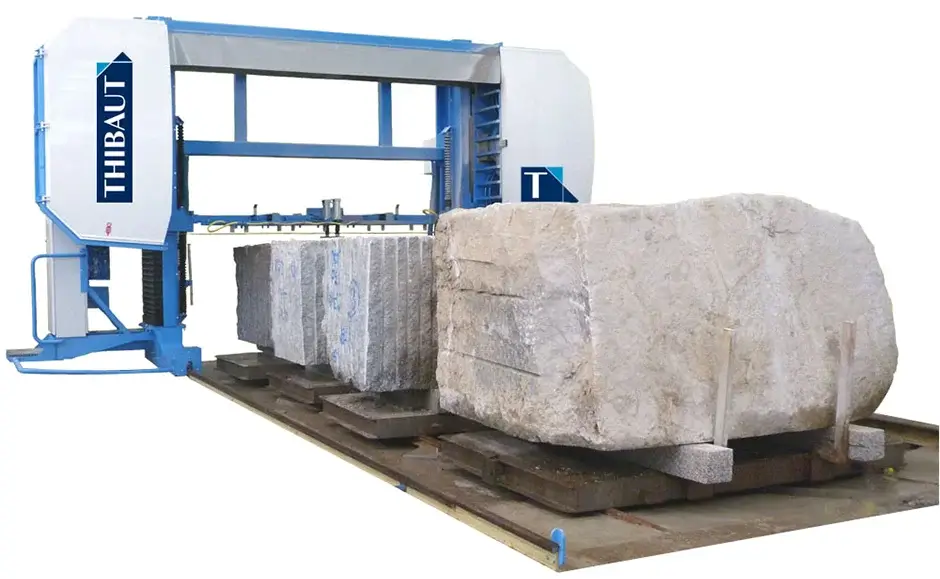
EDM wire cut machines are widely used in industries such as aerospace, automotive, medical device manufacturing, and mold making, where tight tolerances and complex shapes are required. They offer advantages such as the ability to work with a variety of materials, including hardened steels and exotic alloys, and minimal material wastage due to the non-contact nature of the cutting process. Overall, EDM wire cut machines are essential tools for achieving precision machining in modern manufacturing processes.
Performance Characteristics of EDM Wire Cut Machines
- High Precision: EDM wire cut machines can achieve micron-level precision in cutting and shaping materials.
- Versatility: They are capable of cutting a wide range of materials, including hardened steels, exotic alloys, and non-conductive ceramics.
- Complex Shape Machining: These machines can produce intricate shapes and features with ease, allowing for the creation of complex components.
- Minimal Material Wastage: Due to the non-contact nature of the cutting process, EDM wire cut machines minimize material wastage, making them cost-effective.
- Surface Finish: They can achieve high-quality surface finishes, suitable for applications requiring smooth and polished surfaces.
- Tight Tolerances: EDM wire cut machines can achieve tight tolerances, making them ideal for applications where precision is critical.
- Automation: Some modern EDM wire cut machines feature automation capabilities, allowing for unmanned operation and increased productivity.
- Wire Recycling: The wire electrodes used in EDM wire cut machines can be recycled, reducing operational costs and environmental impact.
- Heat-Affected Zone: The heat-affected zone in the workpiece is minimal, preserving the material’s properties and integrity.
Elevate your manufacturing capabilities with the Quartz Cutting Machinery from Shine. Experience precision and efficiency like never before. Get yours today!
Upgrade Your Manufacturing with Shine’s Quartz Cutting Machinery!
Delving into the Mechanisms: How EDM Wire Cut Machines Operate
Components at the Core
At the heart of every EDM wire cut machine lies a carefully orchestrated ensemble of components, each playing a crucial role in the machining process. From the wire electrode to the control system, every element contributes to the machine’s ability to deliver precise cuts with unmatched accuracy.
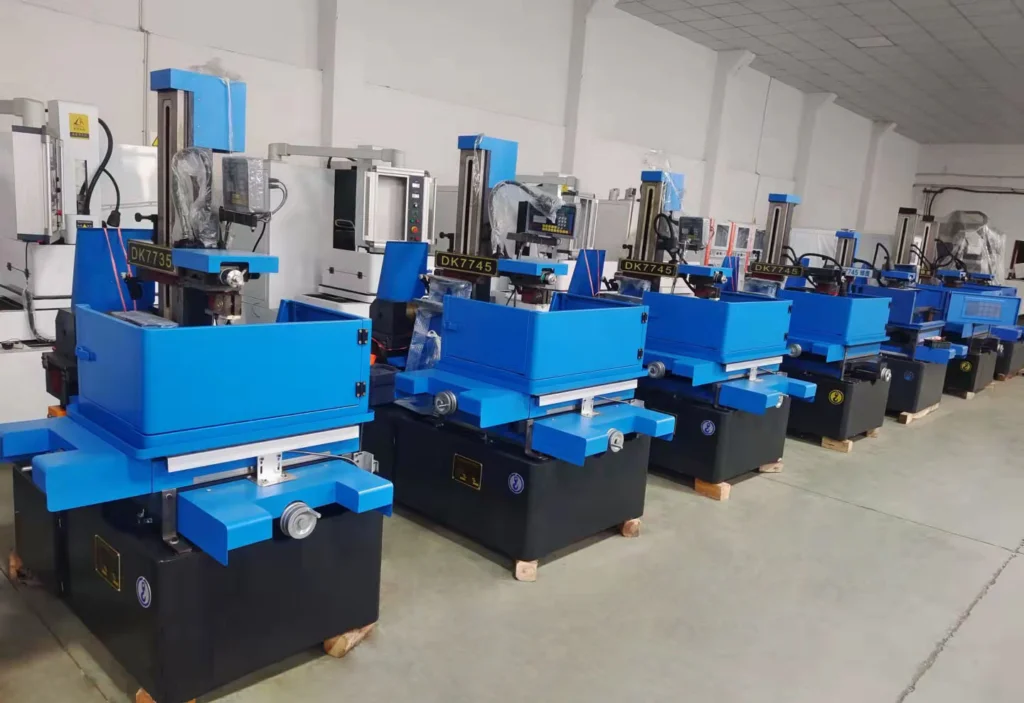
1. Wire Electrode: The Cutting Edge
The wire electrode serves as the primary tool for material removal in EDM wire cut machines. Made of conductive materials such as brass or copper, the wire delivers controlled electrical discharges to erode material from the workpiece, allowing for precise shaping and machining.
2. Dielectric Fluid: Cooling and Cleansing
Dielectric fluid, typically deionized water, serves multiple purposes in the EDM wire cutting process. It acts as a coolant, dissipating heat generated during machining, and also serves as a medium for flushing away debris, ensuring a clean and efficient cutting environment.
3. Power Supply: Energizing Precision
The power supply unit of an EDM wire cut machine generates electrical pulses that power the machining process. By controlling the intensity and duration of these pulses, the power supply ensures precise material removal, allowing for the creation of intricate shapes and features with unparalleled accuracy.
4. Control System: Orchestrating Precision
The control system serves as the brain of the EDM wire cut machine, orchestrating its operation with meticulous precision. Integrated with advanced CAD/CAM software, the control system translates design specifications into machining instructions, ensuring seamless execution of complex machining tasks.
Precision in Action: The Machining Process
The operation of an EDM wire cut machine revolves around the principle of electrical discharge machining, a process that relies on controlled electrical sparks to erode material from the workpiece. Let’s delve deeper into the intricacies of this process and explore how it enables the creation of intricate components with micron-level precision.
Wire Tensioning and Feeding Mechanism: Ensuring Stability
The wire electrode is carefully tensioned and fed through the workpiece under controlled conditions to ensure stable and consistent machining. By maintaining optimal tension and feed rates, manufacturers can minimize the risk of wire breakage or deviation from the desired cutting path, ensuring uninterrupted machining operations.
Electrical Discharge Machining Process: Sparking Precision
During machining, a series of controlled electrical sparks are generated between the wire electrode and the workpiece. These sparks create intense heat, melting and vaporizing material from the workpiece surface, allowing for precise shaping and machining of intricate features with micron-level accuracy.
Controlling the Spark Gap: Fine-Tuning Precision
The distance between the wire electrode and the workpiece, known as the spark gap, is meticulously controlled throughout the machining process. By fine-tuning the spark gap, manufacturers can optimize cutting speed and accuracy, ensuring consistent and reliable machining results across a wide range of materials and applications.
Material Removal Mechanism: Flushing Efficiency
As material is eroded by the electrical discharge, it is flushed away by the dielectric fluid, leaving behind a clean and precise cut surface. This combination of controlled sparks and flushing action ensures high-quality machining results with minimal heat-affected zones, allowing for the creation of intricate components with exceptional surface finish and dimensional accuracy.
Want to witness the cutting-edge technology behind diamond wire cutting machines? Look no further than Endless Diamond Wire Loop! Click the link to explore our latest innovations and revolutionize your manufacturing processes. Well Watch now on YouTube Now!!!
Discover the Power of Diamond Wire Cutting Machines | Endless Diamond Wire Loop
Advantages of EDM Wire Cut Machines: Shining Bright in the Manufacturing Landscape
Precision and Accuracy: The Hallmarks of Excellence
EDM wire cut machines excel in delivering precision and accuracy that surpass traditional machining methods. With the ability to achieve micron-level tolerances and intricate geometries, these machines empower manufacturers to produce components of unparalleled quality and reliability, setting new standards of excellence in the manufacturing landscape.
Versatility in Material Compatibility: Adapting to Diverse Needs
Unlike conventional machining methods, EDM wire cut machines can work with a wide range of materials, including hardened steels, exotic alloys, and even non-conductive ceramics. This versatility enables manufacturers to tackle diverse machining challenges with confidence, opening up new possibilities for innovation and product development.
Minimal Material Wastage: Maximizing Efficiency
The non-contact nature of EDM wire cutting minimizes material wastage, making it a cost-effective solution for machining expensive or hard-to-machine materials. Additionally, the ability to recycle wire electrodes further reduces operational costs and environmental impact, ensuring sustainable manufacturing practices without compromising on quality or performance.
Complex Shape Machining Capability: Pushing Boundaries of Design
With EDM wire cut machines, the only limit to geometric complexity is the designer’s imagination. From intricate cavities to complex contours, these machines can faithfully replicate even the most challenging shapes with unparalleled accuracy, empowering manufacturers to push the boundaries of design and innovation in product development.
How to Choose the edm wire cut machines?
Choosing the right EDM wire cut machine is crucial for achieving optimal results in your manufacturing processes. Here’s a guide to help you navigate the selection process, with a focus on the brand Shine:
Factors to Consider When Choosing Shine EDM Wire Cut Machines
- Precision and Accuracy: Evaluate the machine’s ability to achieve tight tolerances and high precision, ensuring it meets your specific machining requirements.
- Versatility: Consider the range of materials the Shine EDM wire cut machine can work with, including compatibility with hardened steels, exotic alloys, and non-conductive ceramics.
- Technology and Innovation: Look for advanced features and innovations in Shine’s EDM wire cut machines, such as automation capabilities, integrated CAD/CAM software, and enhanced control systems.
- Quality and Reliability: Assess Shine’s reputation for manufacturing high-quality and reliable machines, backed by robust warranties and after-sales support services.
- Cost-Effectiveness: Balance the initial investment cost with the long-term benefits and cost savings offered by Shine’s EDM wire cut machines, considering factors such as material wastage, operational efficiency, and maintenance requirements.
- Customer Reviews and Feedback: Research customer reviews and testimonials to gauge user experiences and satisfaction levels with Shine’s EDM wire cut machines, helping you make an informed decision.
- Training and Support: Inquire about the availability of training programs and technical support services offered by Shine, ensuring your team is adequately trained and supported in operating and maintaining the machine effectively.
- Future Expansion and Upgrades: Consider Shine’s commitment to product development and future upgrades, ensuring compatibility with evolving industry standards and technological advancements.
By carefully considering these factors and conducting thorough research, you can confidently choose Shine’s EDM wire cut machine that best aligns with your manufacturing needs and objectives.
Conclusion: Illuminating the Future of Manufacturing
In conclusion, EDM wire cut machines stand as shining beacons of innovation in the field of precision engineering. By harnessing the power of Electrical Discharge Machining, these machines enable manufacturers to achieve levels of precision and accuracy that were once thought impossible, revolutionizing the way intricate components are produced across diverse industries. As we look to the future, the potential of EDM wire cut machines to drive further advancements in manufacturing technology is boundless, promising new opportunities for innovation, efficiency, and excellence in the ever-evolving landscape of modern industry.
What is a wire cutting machine?
A wire cutting machine is a specialized tool used in manufacturing processes to precisely cut and shape materials. It utilizes a thin wire electrode to deliver controlled electrical discharges, eroding material from the workpiece to create intricate shapes with high precision.
How does a wire cutting machine work?
In a wire cutting machine, a thin wire electrode is fed through the workpiece while an electrically charged pulse generates sparks between the wire and the workpiece. These controlled sparks melt and vaporize material from the workpiece, allowing for precise shaping and machining.
What materials can be cut using wire cutting machines?
Wire cutting machines can work with a wide range of materials, including metals, plastics, ceramics, and composites. They are particularly suitable for cutting materials that are difficult to machine using traditional methods or require high precision.
What are the advantages of using wire cutting machines?
Wire cutting machines offer several advantages, including high precision, versatility, minimal material wastage, and the ability to create complex shapes and features. They are widely used in industries such as aerospace, automotive, medical device manufacturing, and mold making.
How do I choose the right wire cutting machine for my needs?
When choosing a wire cutting machine, consider factors such as precision, versatility, technology and innovation, quality and reliability, cost-effectiveness, customer reviews and feedback, training and support, and future expansion and upgrades. It’s also essential to assess your specific machining requirements and industry standards before making a decision.