Keywords: Glass Cutting Machine,Cut Machine
Table of Contents
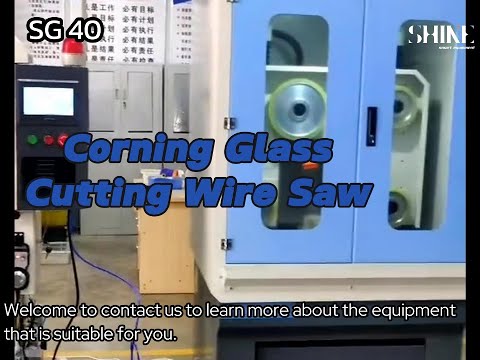
Q1: What are the Common Types of Industrial Glass Used in Semiconductor and Optical Industries?
In the realms of semiconductor manufacturing and optical applications, the type of glass used is not just a matter of transparency and aesthetics, but of precise physical and chemical properties. Two prominent types of glass used in these sectors include:
- Borosilicate Glass: Known for its low coefficient of thermal expansion, borosilicate glass is a stalwart in environments where temperature fluctuations are common. Its resilience against thermal shock makes it an ideal candidate for semiconductor applications where stability is paramount.
- Fused Silica: This type of glass boasts exceptional optical clarity and high UV transmission, making it a preferred choice in the optical industry. Its low thermal expansion and high melting point make it suitable for intricate processing and applications involving high-temperature exposures.
Q2: What are the Different Types of Glass Cutting Machines, Including the Endless Diamond Wire Cut Machine and Inner Diameter Saw?
In the world of industrial glass cutting, precision and efficiency are paramount. Various types of cutting machines have been developed to meet these stringent requirements. Here, we focus on two significant technologies – the Endless Diamond Wire Cut Machine and the Inner Diameter Saw, along with an overview of other common types:
- Endless Diamond Wire Cut Machine:
- Mechanism: Utilizes a continuous loop of wire embedded with diamond particles.
- Advantages: Offers high precision, minimal material wastage, and is capable of making intricate cuts without exerting excessive pressure on the glass, reducing the risk of cracks.
- Applications: Ideal for cutting complex shapes in optical glass, where precision is non-negotiable.
- Inner Diameter Saw (ID Saw):
- Mechanism: Employs a thin, circular blade to make precise cuts.
- Advantages: Particularly effective for creating small, precise openings and is widely used in semiconductor manufacturing for its ability to produce clean, straight cuts.
- Applications: Predominantly used in semiconductor fabrication processes, especially for slicing wafer-thin layers.
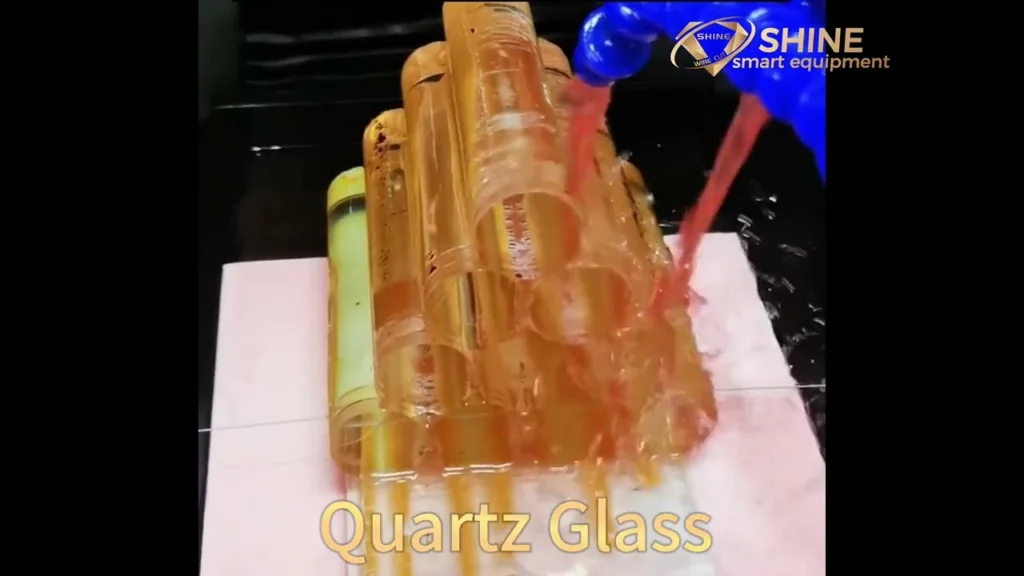
Other common types of glass cutting machines include:
- CNC Glass Cutting Machines: Controlled by computer programs, these machines can perform complex cuts with high precision.
- Water Jet Cutters: These machines use a high-pressure jet of water, sometimes mixed with an abrasive substance, to cut through glass. They are versatile and can cut various thicknesses without generating heat.
- Laser Glass Cutting Machines: Employ laser beams to score the glass. They offer precise control and are used for intricate designs and shapes.
Each type of machine has its unique set of capabilities and is chosen based on the specific requirements of the task, such as the type of glass, required precision, and production volume.
Q3: Key Features of High-Quality Glass Cutting Machines for Industrial Use
When selecting a glass cutting machine for industrial applications, especially in the semiconductor and optical sectors, certain features stand out as crucial:
- Precision and Accuracy: The ability to make exact cuts according to specified dimensions is fundamental, as even minor deviations can render a piece unusable.
- Speed and Efficiency: Machines must balance speed with precision to meet industrial production timelines.
- Versatility: The ability to handle various types of glass and different thicknesses is vital.
- Durability and Reliability: Machines should withstand continuous usage with minimal downtime.
- Ease of Maintenance: Quick and easy maintenance reduces downtime and ensures consistent performance.
Q4: Challenges in Cutting Different Thicknesses of Industrial Glass
Cutting different thicknesses of glass, especially for high-precision industries, presents unique challenges:
- Thin Glass: Risk of breakage and difficulty in maintaining dimensional accuracy.
- Thick Glass: Requires more power and the risk of uneven cuts or glass chipping increases.
- Solutions include using specialized blades or wires, adjusting cutting speed, and employing advanced control systems for precision.
Q5: Customization of Glass Cutting Machines for Industry-Specific Needs
Customization is key in industrial applications:
- Tailored for Specific Glass Types: Machines can be customized to handle specific glass types used in different industries.
- Custom Cutting Patterns: Especially in the semiconductor industry, where unique cutting patterns may be required.
- Integration with Manufacturing Systems: Machines can be designed to integrate with existing manufacturing systems for streamlined operations.
Q6: Safety Precautions in Operating Industrial Glass Cutting Machines
Operating glass cutting machines, particularly in high-stakes industrial environments, demands stringent safety measures:
- Personal Protective Equipment (PPE): Operators must wear appropriate safety gear, including gloves, safety glasses, and ear protection.
- Machine Safety Features: Modern machines come equipped with safety features like emergency stop buttons, safety guards, and automatic shut-off mechanisms.
- Training and Protocols: Proper training for operators is crucial, including handling the machine, understanding safety protocols, and emergency procedures.
Q7: The Impact of Automation in Glass Cutting Technology
Automation has brought a significant shift in glass cutting technology:
- Increased Precision and Consistency: Automated systems allow for precise cuts with minimal human error.
- Enhanced Production Speed: Automation accelerates the cutting process, enabling higher production rates.
- Data Integration and Optimization: Automated machines can be integrated with production data systems, allowing for real-time adjustments and optimizations.
Q8: Maintenance Requirements for Glass Cutting Machines
Proper maintenance is vital for the longevity and optimal performance of glass cutting machines:
- Regular Cleaning and Inspections: Regularly removing glass debris and inspecting the machine for wear and tear can prevent major breakdowns.
- Routine Calibration and Adjustments: Ensuring that all components are correctly calibrated and adjusted is key to maintaining precision.
- Scheduled Professional Servicing: Regular professional maintenance helps in early identification and rectification of potential issues.
Q9: Future Trends in Glass Cutting Machine Technology
Looking to the future, several trends are set to shape the evolution of glass cutting machines:
- Advanced Material Technology: Development of new materials for blades and wires that offer higher precision and durability.
- AI and Machine Learning: Incorporation of AI could lead to smarter, more adaptive cutting machines.
- Sustainable Practices: Focus on environmentally friendly technologies and energy-efficient designs.
Conclusion
In conclusion, glass cutting machines, particularly those used in semiconductor and optical industries, are vital tools requiring precision, efficiency, and safety. From the versatile Endless Diamond Wire Cut Machine to the precise Inner Diameter Saw, each machine serves a specific purpose. As technology advances, we can expect even more innovative solutions in this field, driving forward the capabilities of industrial glass cutting.