Are you tired of struggling with traditional cutting methods that compromise precision and efficiency? Do you find yourself seeking a solution that can revolutionize your cutting processes? Look no further than Diamond Wire Loop Cut Machines. In this guide, we delve into the transformative power of these machines, offering insights into their technology, applications, and operational benefits. Join us on a journey to unlock the secrets of precision cutting.
For industries ranging from semiconductor manufacturing to construction, achieving precise cuts is paramount. However, traditional cutting methods often fall short, leading to inefficiencies and material wastage. Enter Diamond Wire Loop Cut Machines—the cutting-edge solution designed to revolutionize precision cutting. In the following sections, we explore the fundamentals of these machines, their applications across various industries, and practical insights for operation and maintenance.
The Ultimate Guide to Diamond Wire Loop Cut Machines: Revolutionizing Precision Cutting
Table of Contents
Introduction
In the world of precision cutting, one technology stands out for its unparalleled accuracy and efficiency: the Diamond Wire Loop Cut Machine. This revolutionary innovation has transformed various industries, from semiconductor manufacturing to stone cutting and beyond. In this comprehensive guide, we’ll delve deep into the workings of these machines, explore their advantages and limitations, examine industry applications, and provide practical insights for operation and maintenance.
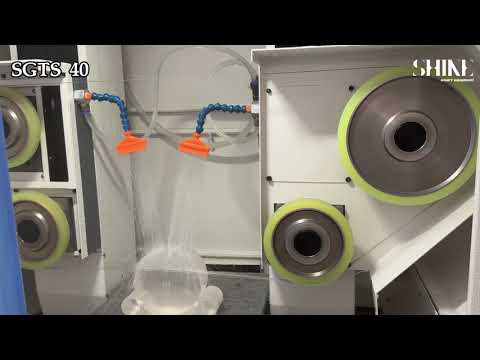
Understanding Diamond Wire Loop Cut Machines
Diamond Wire Loop Cut Machines are innovative tools used for precision cutting in various industries. These machines utilize a loop of diamond-studded wire to slice through materials with incredible accuracy and efficiency. From semiconductor manufacturing to stone cutting and construction, Diamond Wire Loop Cut Machines have revolutionized cutting processes, offering unparalleled precision and minimizing material wastage. By understanding the principles behind these machines and their applications, industries can optimize their production processes and achieve superior results.
The Evolution of Cutting Technology: From Traditional to Advanced Solutions
From manual cutting methods to advanced automated systems, the evolution of cutting technology has been remarkable. Traditional methods often lacked precision and efficiency, leading to material wastage and suboptimal results. However, with the advent of Diamond Wire Loop Cut Machines, a new era of cutting technology emerged, offering unparalleled accuracy and productivity.
Basics of Diamond Wire Loop Cut Machines
What is a Diamond Wire Loop Cut Machine?
A Diamond Wire Loop Cut Machine is a cutting tool used for precise slicing of various materials, including semiconductors, stones, and construction materials. It utilizes a loop of diamond-studded wire to achieve high-precision cuts with minimal waste.
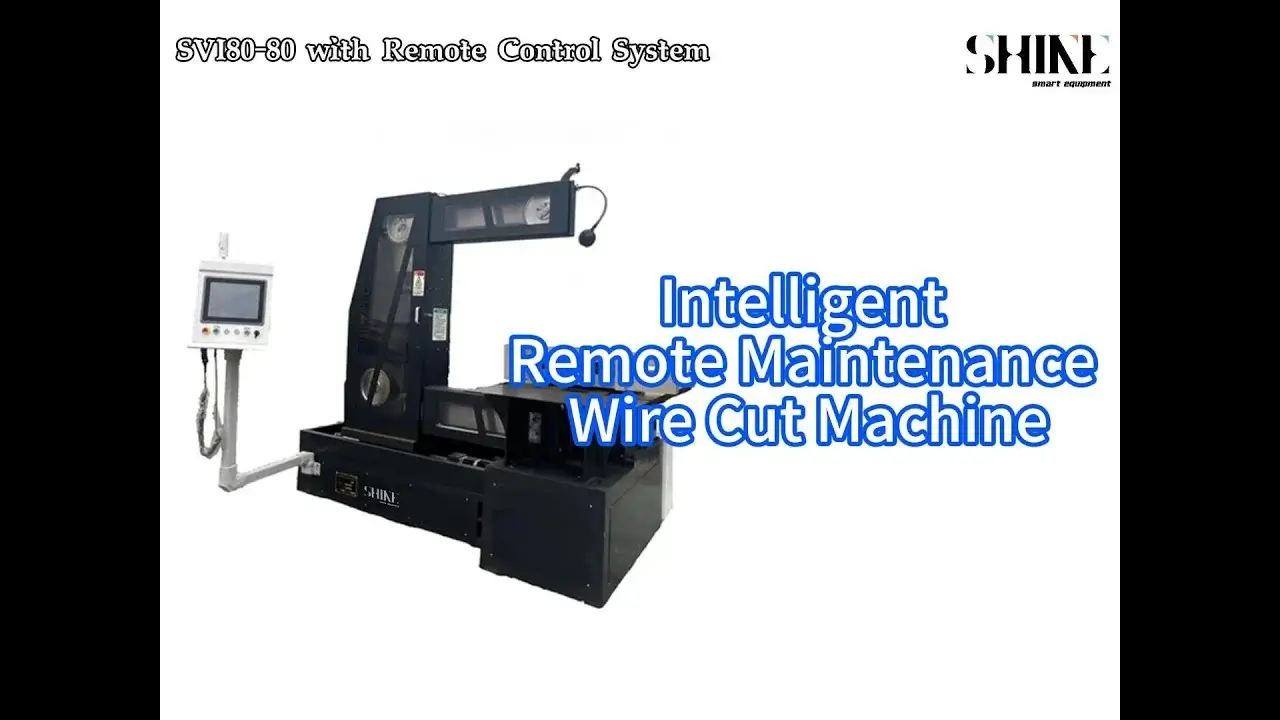
Components and How They Work Together
Diamond Wire Loop Cut Machines consist of several key components, including:
- Wire Spool: Stores the diamond-studded wire.
- Tensioning System: Maintains optimal tension in the wire loop.
- Drive System: Powers the movement of the wire loop.
- Control Panel: Allows operators to adjust parameters such as speed and feed rate.
These components work together seamlessly to ensure smooth operation and precise cutting.
The Science Behind the Cutting
At the heart of Diamond Wire Loop Cut Machines lies the science of abrasion. Diamonds, known for their exceptional hardness, are bonded to the wire loop’s surface. As the wire loop moves across the material to be cut, the diamonds exert immense pressure, gradually wearing away the material and producing a clean, precise cut.
The Role of Diamonds in Cutting Technology
Diamonds play a crucial role in cutting technology due to their unmatched hardness and abrasiveness. By embedding diamonds into the wire loop, Diamond Wire Loop Cut Machines can effortlessly slice through even the toughest materials with incredible precision.
How Diamond Wires Make Precise Cuts
The design of the diamond-studded wire loop ensures consistent cutting performance. As the wire loop moves through the material, the diamonds maintain sharp edges, ensuring uniform cutting action along the entire length of the wire.
Types of Diamond Wire Loop Cut Machines
Manual vs Automated Machines
Diamond Wire Loop Cut Machines are available in both manual and automated variants, each with its own set of advantages and limitations.
Pros and Cons of Each Type
- Manual Machines:
- Pros: Affordable, suitable for small-scale operations.
- Cons: Limited precision, operator-dependent.
- Automated Machines:
- Pros: High precision, efficient, suitable for large-scale production.
- Cons: Higher initial investment, complex setup.
Suitability According to Use Cases
The choice between manual and automated machines depends on the specific requirements of the application. For small-scale projects or research purposes, manual machines may suffice. However, for industrial-scale production or high-precision cutting tasks, automated machines are preferred.
Variations by Application
Diamond Wire Loop Cut Machines cater to a wide range of applications, including:
- Semiconductor Manufacturing: Precision cutting of silicon wafers and other semiconductor materials.
- Stone and Construction Material Cutting: Efficient slicing of granite, marble, and other natural stones.
- Others: Aerospace, research, and various industrial applications.
Operational Insights
Setting Up Your Machine
Proper setup is crucial for the optimal performance of Diamond Wire Loop Cut Machines.
Installation Guide
Follow these steps for seamless machine installation:
- Assemble Components: Gather all components of your Diamond Wire Loop Cut Machine, including the wire spool, tensioning system, drive system, and control panel.
- Calibrate Parameters: Adjust tension, speed, and feed rate settings according to the manufacturer’s recommendations to ensure optimal performance.
- Test Run: Conduct a test run to verify the functionality of the machine and ensure that all components are operating smoothly.
- Safety Check: Prioritize safety by ensuring that all safety features are in place and functioning correctly before proceeding with installation.
- Secure Placement: Position the machine in a stable and well-ventilated area, away from potential hazards or obstructions.
- Power Connection: Connect the machine to a suitable power source, following the manufacturer’s guidelines for electrical connections.
- Final Inspection: Perform a final inspection to confirm that all components are correctly assembled and that the machine is ready for operation.
By following this installation guide, you can set up your Diamond Wire Loop Cut Machine efficiently and safely, ensuring optimal performance for your cutting needs. For more detailed instructions, refer to the user manual provided by SHINE.
Safety Protocols and Best Practices
Prioritize safety by adhering to these best practices:
- Wear appropriate personal protective equipment (PPE).
- Follow established safety protocols for machine operation.
- Conduct regular safety inspections and maintenance checks.
Operating the Machine
Master the operation of your Diamond Wire Loop Cut Machine with this step-by-step guide:
- Load Material: Secure the material to be cut in the machine’s work area.
- Adjust Parameters: Set the desired cutting parameters, such as speed and feed rate.
- Initiate Cutting: Start the machine and monitor the cutting process closely.
- Quality Check: Inspect the cut for accuracy and adjust parameters if necessary.
Tips for Efficient Cutting
Maximize efficiency with these tips:
- Optimize Cutting Parameters: Adjust parameters such as wire tension, speed, and feed rate according to the material being cut. Fine-tuning these settings ensures precise cuts and maximizes efficiency.
- Choose High-Quality Diamond Wires: Utilize diamond wires with superior quality and durability. High-quality wires ensure consistent cutting performance and minimize the need for frequent replacements, saving time and resources.
- Minimize Material Handling: Reduce material handling by optimizing cutting paths and layouts. Minimizing unnecessary movements and repositioning of materials can significantly improve cutting efficiency.
- Implement Batch Cutting: When possible, batch similar cutting tasks together to optimize machine utilization and minimize downtime between setups. This approach streamlines the cutting process and increases overall productivity.
- Regular Maintenance Checks: Perform regular maintenance checks to ensure the machine operates at peak efficiency. This includes inspecting and cleaning components, lubricating moving parts, and replacing worn or damaged parts promptly.
- Monitor Cutting Progress: Keep a close eye on the cutting process and make adjustments as needed. Monitoring cutting progress allows operators to identify and address any issues promptly, preventing potential disruptions and ensuring consistent quality.
- Invest in Operator Training: Provide comprehensive training for machine operators to ensure they understand the proper operation and maintenance procedures. Well-trained operators can maximize machine performance and minimize the risk of errors or accidents.
- Stay Updated with Technology: Keep abreast of the latest advancements in cutting technology and equipment. Upgrading to newer models or incorporating innovative features can enhance cutting efficiency and productivity over time.
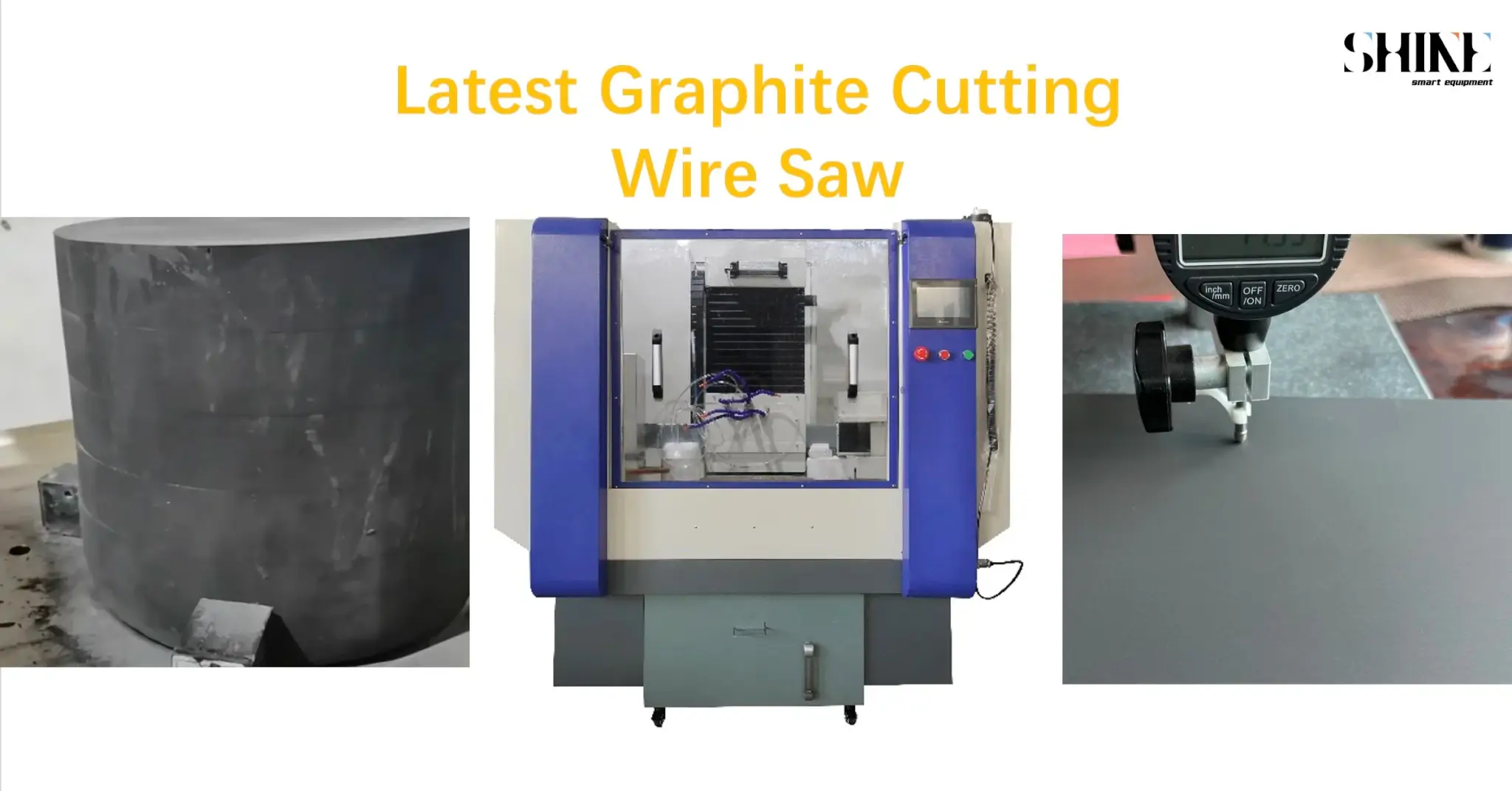
Maintenance and Troubleshooting
Preventive maintenance is essential for prolonging the lifespan of your Diamond Wire Loop Cut Machine.
Routine Maintenance Schedule
Follow a regular maintenance schedule that includes:
- Cleaning and lubricating moving parts.
- Checking and replacing worn components.
- Verifying calibration and alignment.
Common Issues and How to Resolve Them
Troubleshoot common issues such as:
- Wire breakage: Check tension and alignment, and replace worn wires.
- Poor cutting quality: Adjust parameters and inspect for worn components.
Advantages and Limitations
Advantages of Using Diamond Wire Loop Cut Machines
Diamond Wire Loop Cut Machines offer numerous benefits:
- Precision and Accuracy: Diamond Wire Loop Cut Machines offer unparalleled precision, allowing for micron-level accuracy in cutting. This precision ensures consistent and high-quality results, essential for industries such as semiconductor manufacturing and stone cutting.
- Efficiency and Productivity: With their automated operation and optimized cutting parameters, Diamond Wire Loop Cut Machines can significantly increase productivity compared to traditional cutting methods. Faster cutting speeds and reduced material wastage translate to higher efficiency and cost savings.
- Material Savings: By minimizing kerf width and reducing material wastage, Diamond Wire Loop Cut Machines maximize material utilization. This not only reduces costs associated with raw materials but also contributes to environmental sustainability by minimizing waste.
- Versatility and Flexibility: Diamond Wire Loop Cut Machines are versatile tools capable of cutting a wide range of materials, including semiconductors, stones, and construction materials. This versatility makes them indispensable across various industries, from electronics manufacturing to architectural design.
- Reduced Manual Labor: Automation features in Diamond Wire Loop Cut Machines reduce the need for manual labor, leading to improved worker safety and efficiency. Operators can oversee cutting processes remotely, minimizing exposure to hazardous environments.
- Consistent Performance: Diamond Wire Loop Cut Machines deliver consistent cutting performance over prolonged periods, thanks to their durable construction and high-quality components. This reliability ensures minimal downtime and consistent quality output.
- Innovative Technology: As leaders in cutting-edge technology, Diamond Wire Loop Cut Machines incorporate innovative features and advancements to stay ahead of industry trends. Continuous research and development efforts further enhance their performance and capabilities.
- Long-Term Cost Savings: While the initial investment in Diamond Wire Loop Cut Machines may be higher compared to traditional cutting methods, the long-term cost savings in terms of increased productivity, reduced material wastage, and lower maintenance costs make them a cost-effective choice in the long run.
Limitations and Challenges
Despite their advantages, Diamond Wire Loop Cut Machines have limitations:
Initial Investment and Cost Analysis
High initial investment may deter small-scale operators.
Technical Limitations and Solutions
Address technical challenges through continuous innovation and research.
Industry Applications
Semiconductor Industry
Precision cutting plays a critical role in semiconductor manufacturing:
The Role of Precision Cutting in Semiconductor Manufacturing
Ensure the integrity and quality of silicon wafers for electronic devices.
Case Studies: Success Stories
Explore real-world examples of Diamond Wire Loop Cut Machines in action.
Construction and Stone Industry
Diamond Wire Loop Cut Machines revolutionize stone cutting and sculpting:
Advantages in Stone Cutting and Sculpting
Achieve intricate designs with unparalleled precision.
Real-World Applications and Outcomes
Transform architectural and artistic projects with precision cutting.
Emerging Fields and Future Applications
Explore the potential of Diamond Wire Loop Cut Machines in:
Aerospace and Advanced Materials
Push the boundaries of precision cutting in aerospace and beyond.
The Future of Diamond Wire Cutting Technology
Continued innovation promises even greater advancements in cutting technology.
Purchasing Guide
How to Choose the Right Machine
Experience precision cutting like never before with our Quartz Cutting Machinery. Designed for optimal performance and efficiency, our Quartz Cutting Machinery delivers superior results, making it the perfect choice for your cutting needs. Upgrade your cutting processes today with SHINE’s Quartz Cutting Machinery.
How to buy the Quartz Cutting Machinery
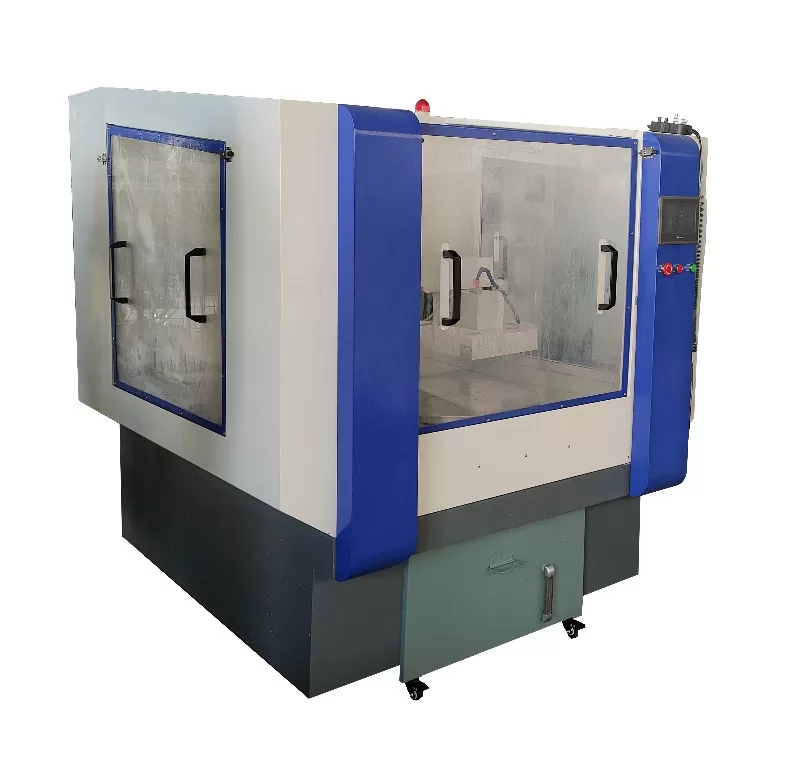
Consider these factors when selecting a Diamond Wire Loop Cut Machine:
Factors to Consider
- Cutting capacity
- Precision and accuracy
- Automation capabilities
Vendor Comparison and Recommendations
Evaluate different vendors based on:
- Product quality
- After-sales support
- Cost-effectiveness
Cost Analysis and ROI
Calculate the return on investment (ROI) based on:
- Initial cost
- Long-term savings
- Case Studies: ROI for Different Industries
For more insights into Diamond Wire Loop Cut Machines and their applications, check out our informative video on Endless Diamond Wire Loop’s YouTube Channel.
Conclusion
In conclusion, Diamond Wire Loop Cut Machines represent a paradigm shift in precision cutting technology. With their unparalleled accuracy and efficiency, these machines are poised to transform industries and optimize production processes. Are you ready to elevate your cutting standards and maximize efficiency? Explore our range of Diamond Wire Loop Cut Machines and embark on a journey towards precision perfection with SHINE.
Experience the cutting-edge technology of Diamond Wire Loop Cut Machines and revolutionize your cutting processes today. Visit SHINE to explore our range of machines and unlock a new era of precision cutting.
FAQs
- What materials can be cut with a diamond wire loop cut machine? Diamond Wire Loop Cut Machines can cut a wide range of materials, including semiconductors, stones, construction materials, and more.
- How long does a diamond wire last? The lifespan of a diamond wire varies depending on factors such as material hardness, cutting parameters, and maintenance practices. Generally, diamond wires can last for multiple cutting cycles before replacement.
- Can these machines cut complex shapes? Yes, Diamond Wire Loop Cut Machines are capable of cutting complex shapes with precision, making them versatile tools for various applications.
- What are the main maintenance requirements for a diamond wire loop cut machine? Regular maintenance tasks include cleaning and lubricating moving parts, checking tension and alignment, and replacing worn components as needed.
- How does the cost of a diamond wire loop cut machine compare to traditional cutting methods? While Diamond Wire Loop Cut Machines may have a higher initial investment, they offer long-term cost savings through improved efficiency, reduced material wastage, and higher precision cutting.
- Is training required to operate a diamond wire loop cut machine? Yes, operators should undergo training to familiarize themselves with machine operation, safety protocols, and maintenance procedures to ensure optimal performance and safety.