In the realm of industrial manufacturing, precision and durability are paramount, especially when dealing with materials as robust and challenging as industrial ceramics. The advent of advanced wire cutting machines, particularly diamond wire cutting machines, has revolutionized the way these materials are handled. Brands like Shine have been at the forefront of this transformation, providing cutting-edge solutions that cater to the most demanding applications. But what makes wire cutting so essential in the world of industrial ceramics? Let’s dive into the details.
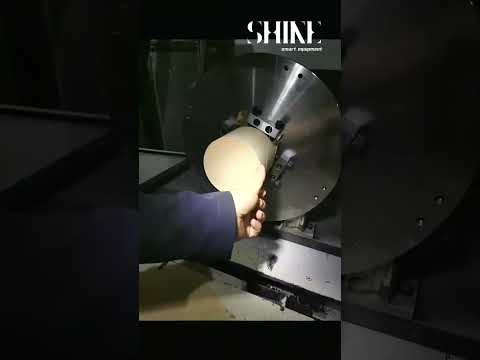
Introduction to Industrial Ceramics
Industrial ceramics are a cornerstone of modern manufacturing, known for their exceptional durability, resistance to high temperatures, and remarkable hardness. These materials, produced by companies like Shine, are engineered to perform under the most demanding conditions, making them indispensable in a variety of high-performance applications.
But what exactly are industrial ceramics? In simple terms, they are inorganic, non-metallic materials that have been subjected to high temperatures to achieve their final form. Unlike traditional ceramics, which you might find in pottery or tiles, industrial ceramics are designed for advanced technical applications. Their unique properties make them suitable for environments where other materials would fail.
Here are some key properties of industrial ceramics:
- High Hardness: Industrial ceramics are incredibly hard, often surpassing the hardness of metals. This makes them ideal for cutting and machining tools.
- Thermal Resistance: They can withstand extreme temperatures, which is why they are used in applications like turbine engines and heat shields.
- Corrosion Resistance: These materials are highly resistant to chemical corrosion, making them perfect for use in harsh chemical environments.
- Electrical Insulation: Many industrial ceramics are excellent electrical insulators, which is why they are used in electronic components.
Shine’s industrial ceramics are utilized in a multitude of sectors, from aerospace and automotive to electronics and medical devices. The versatility of these materials is astounding, and their applications are continually expanding as new technologies emerge.
One of the key processes in shaping and machining industrial ceramics is wire cutting. Utilizing advanced machinery such as wire cutting machines, diamond wire cutting machines, and diamond wire saw machines, manufacturers can achieve the precise dimensions and intricate shapes required for their specific applications. This technique is particularly essential because of the inherent hardness and brittleness of ceramics, which can make traditional machining methods ineffective or even damaging.
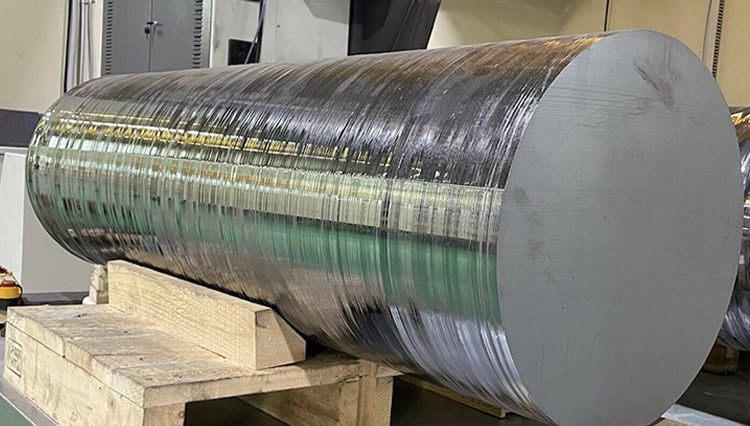
In summary, industrial ceramics are a vital component in the modern industrial landscape. Their unique properties make them suitable for a wide range of applications, and the precision offered by wire cutting machines ensures that these materials can be shaped to meet the exacting standards required by today’s high-tech industries.
Wire Cutting Techniques
When it comes to machining industrial ceramics, precision and durability are paramount. Achieving these qualities requires the use of specialized that can handle the unique challenges posed by these hard, brittle materials. Among the most effective methods are wire cutting machines, diamond wire cutting machines, and diamond wire saw machines. Each of these techniques offers distinct advantages, making them ideal for various applications in demanding environments.
One of the most widely used methods is the wire cutting machine. This technique employs a thin wire, typically made of brass or molybdenum, which is continuously fed through the material. The wire is charged with electrical energy, creating sparks that erode the ceramic material along a predetermined path. This method is known for its high precision and ability to create intricate shapes without causing thermal damage to the ceramics.
For even more demanding applications, the diamond wire cutting machine comes into play. This technique uses a wire embedded with industrial-grade diamonds, which are known for their exceptional hardness. As the diamond wire moves through the ceramic material, it grinds away the material with minimal force, reducing the risk of cracks and ensuring a smooth finish. The diamond wire cutting machine is particularly effective for cutting thick or complex ceramic components where traditional methods might fail.
Another advanced technique is the diamond wire saw machine. Unlike the continuous-feed wire cutting machine, the diamond wire saw machine uses a looped wire that moves in a sawing motion. This method provides greater control over the cutting process and allows for the creation of very fine cuts with exceptional accuracy. The diamond wire saw machine is often used for precision slicing of ceramic wafers and other delicate components.
To summarize, the key wire cutting techniques used in the machining of industrial ceramics include:
- Wire Cutting Machine: Utilizes a thin, electrically charged wire to erode the material with high precision.
- Diamond Wire Cutting Machine: Employs a diamond-embedded wire for grinding through tough ceramic materials with minimal damage.
- Diamond Wire Saw Machine: Uses a looped diamond wire for controlled, precise slicing of delicate ceramic components.
Each of these techniques, whether using a wire cutting machine, diamond wire cutting machine, or diamond wire saw machine, offers unique benefits that cater to the specific needs of industrial ceramics. By leveraging these advanced methods, manufacturers can achieve unparalleled precision and durability in their ceramic components, ensuring they meet the rigorous demands of modern applications.
Advantages of Wire Cutting in Ceramics
When it comes to machining industrial ceramics, the wire cutting machine stands out as a game-changer. The precision and efficiency offered by wire cutting, particularly with a diamond wire cutting machine, are unparalleled. Let’s dive into the key advantages that wire cutting brings to the table, especially in the context of industrial ceramics.
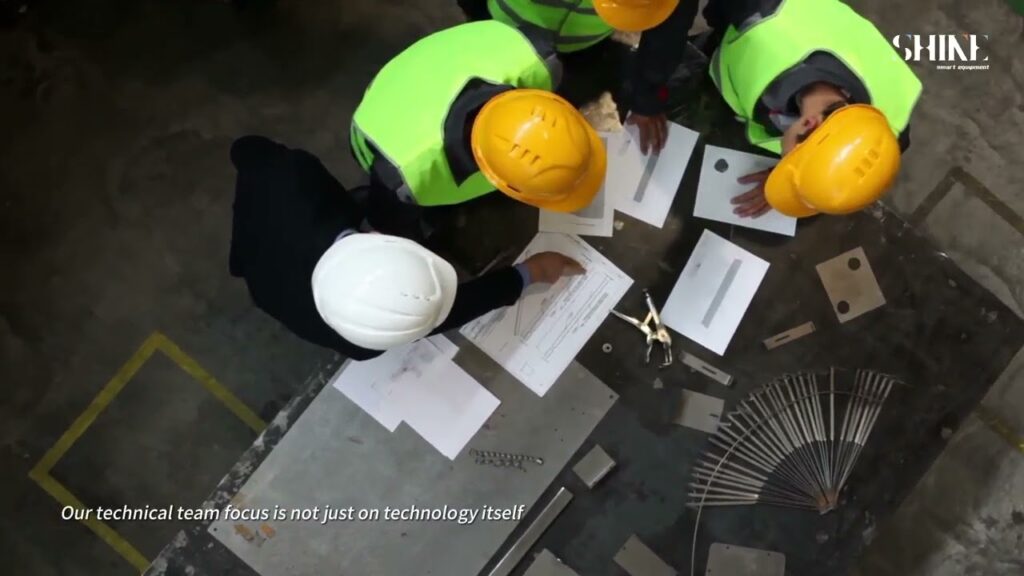
First and foremost, the precision of wire cutting is second to none. Traditional machining methods often struggle with the hardness and brittleness of ceramics, leading to cracks and imperfections. However, a diamond wire saw machine can slice through ceramics with remarkable accuracy, achieving clean cuts and intricate shapes without compromising the material’s integrity. This precision is crucial for applications requiring tight tolerances and intricate designs.
Another significant advantage is the efficiency of wire cutting. The process is not only faster but also more consistent compared to conventional methods. The continuous cutting action of a diamond wire cutting machine ensures a smooth and steady operation, reducing downtime and increasing productivity. This efficiency translates to lower production costs and shorter lead times, which are vital in competitive industries.
Material integrity is another area where wire cutting excels. Traditional methods can generate significant heat and stress, which can alter the properties of ceramics. In contrast, wire cutting generates minimal heat and stress, preserving the original characteristics of the material. This is especially important for high-performance applications where the material’s properties are critical to the end product’s functionality.
Let’s not forget the versatility of wire cutting. Whether it’s a simple cut or a complex shape, a wire cutting machine can handle a wide range of tasks with ease. This versatility makes it an invaluable tool across various industries, from aerospace to electronics, where customized ceramic components are in high demand.
Lastly, the environmental impact of wire cutting is considerably lower than traditional methods. The process generates less waste and requires fewer consumables, making it a more sustainable option. Companies like Shine are at the forefront of developing eco-friendly wire cutting solutions that not only deliver exceptional performance but also minimize environmental impact.
- Unmatched precision and accuracy
- Higher efficiency and productivity
- Preservation of material integrity
- Versatility in handling various tasks
- Lower environmental impact
In summary, the advantages of wire cutting in ceramics are clear. With the precision, efficiency, and material integrity offered by a diamond wire saw machine, it’s no wonder that industries are increasingly turning to this technology. As companies like Shine continue to innovate, the future of wire cutting in ceramics looks brighter than ever.
Applications in Various Industries
Industrial ceramics are a cornerstone in many high-performance applications, and the precision offered by wire cutting methods, particularly with the use of wire cutting machines, diamond wire cutting machines, and diamond wire saw machines, opens up a plethora of opportunities across various industries. Let’s explore how different sectors leverage these advanced techniques to enhance their products and processes.
Aerospace Industry
The aerospace industry demands materials that can withstand extreme temperatures, high stress, and corrosive environments. Industrial ceramics fit the bill perfectly, and the precision of wire cutting technology ensures that these materials are crafted to exact specifications. Shine’s wire cutting machines are instrumental in producing components such as turbine blades, heat shields, and insulators that meet the rigorous standards of aerospace applications.
Electronics Industry
In the fast-evolving world of electronics, miniaturization and precision are key. Diamond wire cutting machines are used to slice through ceramic substrates with unparalleled accuracy, enabling the production of microelectronic components like semiconductors, capacitors, and insulators. Shine’s diamond wire saw machines are particularly valued for their ability to produce clean cuts without damaging the delicate materials, ensuring high performance and reliability in electronic devices.
Medical Industry
Medical technology relies heavily on materials that are biocompatible and durable. Industrial ceramics are used in medical implants, dental prosthetics, and surgical instruments. Wire cutting machines, especially those from Shine, provide the precision needed to create these intricate components. For instance, diamond wire cutting machines are employed to craft ceramic hip joints and dental crowns with exacting detail, ensuring a perfect fit and long-lasting performance.
Automotive Industry
In the automotive sector, industrial ceramics are used for their thermal stability and wear resistance. Components such as brake discs, engine parts, and exhaust systems benefit from the precision cutting offered by wire cutting machines. Shine’s diamond wire saw machines are particularly effective in producing these parts, ensuring they meet the high standards required for automotive safety and performance.
Energy Sector
The energy industry, particularly in renewable energy applications, utilizes industrial ceramics for their insulating properties and durability. Solar panels, fuel cells, and wind turbines all incorporate ceramic components that are precisely cut using wire cutting machines. Shine’s advanced diamond wire cutting machines enable the production of these components with minimal waste and maximum efficiency, contributing to the sustainability of energy solutions.
In conclusion, the applications of wire-cut industrial ceramics span a wide range of industries, each benefiting from the precision, durability, and efficiency that wire cutting machines, including diamond wire cutting machines and diamond wire saw machines from Shine, bring to the table. As technology continues to advance, the role of these cutting-edge tools in shaping the future of industrial ceramics will only become more significant.
Future Trends and Innovations
The world of industrial ceramics is continuously evolving, and the future holds exciting advancements, particularly in wire cutting techniques. As the demand for precision and durability in high-performance applications grows, companies like Shine are at the forefront of these innovations. Let’s dive into some of the emerging trends and technologies that are set to revolutionize the industry.
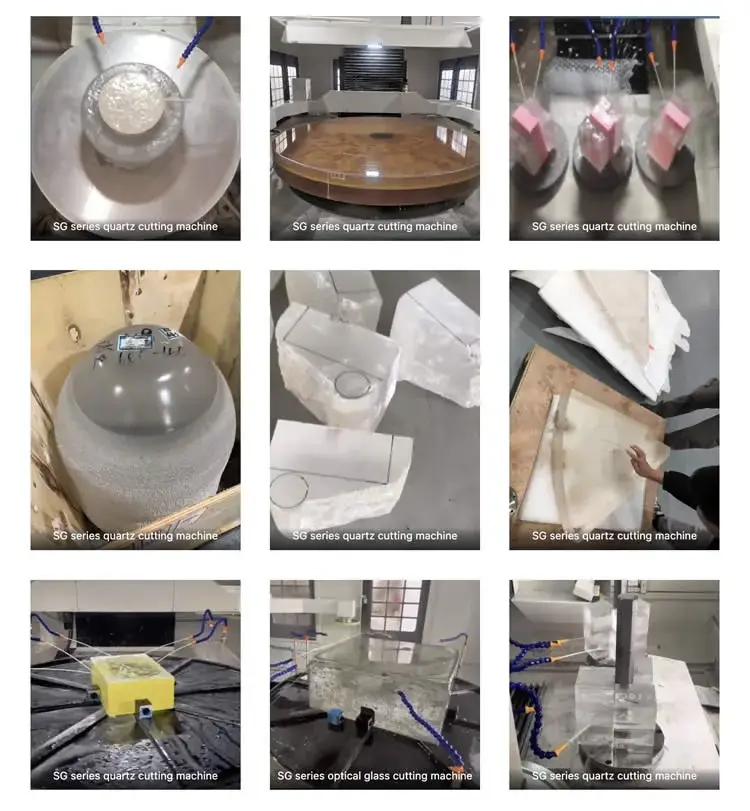
One of the most significant trends is the development of advanced wire cutting machines. These machines are becoming more sophisticated, offering enhanced precision and efficiency. For instance, the latest diamond wire cutting machines are designed to handle even the most challenging ceramic materials with ease. These machines use ultra-thin diamond wires, which not only increase cutting accuracy but also reduce material waste.
Another exciting innovation is the integration of automation and smart technology. Modern wire cutting machines are now equipped with sensors and AI algorithms that can optimize the cutting process in real-time. This means that the machines can adjust parameters such as wire tension and speed automatically, ensuring consistent and high-quality cuts. The use of AI also allows for predictive maintenance, reducing downtime and improving overall productivity.
In addition to automation, there is a growing focus on sustainability in the industry. Companies are increasingly looking for ways to minimize their environmental impact, and wire cutting is no exception. The development of eco-friendly diamond wire saw machines is a testament to this trend. These machines use less energy and produce fewer emissions compared to traditional cutting methods, making them a more sustainable choice for industrial applications.
Moreover, the future of wire cutting in industrial ceramics is likely to see greater customization and flexibility. With advancements in 3D printing technology, it is now possible to create custom wire cutting tools tailored to specific applications. This allows for greater precision and efficiency, as the tools can be designed to meet the exact requirements of the job. Shine is leading the way in this area, offering bespoke solutions that cater to the unique needs of their clients.
Finally, there is a growing emphasis on collaboration and knowledge sharing within the industry. As the technology continues to evolve, it is essential for companies to stay informed about the latest developments. Shine is committed to fostering a culture of innovation and collaboration, regularly hosting workshops and seminars to share their expertise with other industry professionals.
In conclusion, the future of wire cutting in industrial ceramics is bright, with numerous exciting trends and innovations on the horizon. From advanced wire cutting machines and automation to sustainability and customization, the industry is set to undergo significant transformations. Companies like Shine are at the forefront of these changes, driving the development of cutting-edge technologies that will shape the future of industrial ceramics.
Frequently Asked Questions
- What are industrial ceramics?Industrial ceramics are specialized materials known for their exceptional mechanical, thermal, and electrical properties. They are used in a variety of high-performance applications, from aerospace components to electronic devices. Their durability and resistance to extreme conditions make them ideal for demanding environments.
- Why is wire cutting important for industrial ceramics?Wire cutting is crucial for machining industrial ceramics because it allows for high precision and maintains the material’s integrity. Traditional methods can cause cracks or imperfections, but wire cutting ensures smooth, accurate cuts, which is essential for applications requiring exact specifications.
- What are the different wire cutting techniques used?Several wire cutting techniques are employed in the industry, including Electrical Discharge Machining (EDM), laser cutting, and diamond wire cutting. Each method has its own advantages and is chosen based on the specific requirements of the ceramic material and the desired outcome.
- What are the advantages of using wire cutting over traditional methods?Wire cutting offers numerous benefits over traditional methods, such as higher precision, reduced material waste, and improved surface finish. It also minimizes the risk of damaging the ceramic material, ensuring that the final product meets stringent quality standards.
- In which industries are wire-cut industrial ceramics commonly used?Wire-cut industrial ceramics are utilized in a wide range of industries, including aerospace, electronics, medical devices, and automotive. Their unique properties, such as high temperature resistance and electrical insulation, make them indispensable in these fields.
- What future trends and innovations are expected in wire cutting technology?The future of wire cutting technology is promising, with ongoing advancements aimed at enhancing precision, efficiency, and sustainability. Innovations such as automated cutting systems, improved wire materials, and advanced software for better control are expected to revolutionize the industry.
- How does wire cutting improve the durability of industrial ceramics?Wire cutting enhances the durability of industrial ceramics by producing clean and accurate cuts that minimize stress points and potential weaknesses. This precision helps maintain the structural integrity of the ceramics, ensuring they perform reliably in demanding applications.
- Can wire cutting be used for all types of industrial ceramics?While wire cutting is versatile and effective for many types of industrial ceramics, the suitability of the technique depends on the specific properties of the ceramic material. Factors such as hardness, brittleness, and thermal conductivity will influence the choice of cutting method.
- What are the key considerations when selecting a wire cutting method for industrial ceramics?Key considerations include the type of ceramic material, the desired precision and surface finish, the complexity of the cut, and the production volume. Additionally, factors such as cost, speed, and the potential for material waste should be evaluated to determine the most suitable wire cutting method.
- How does wire cutting contribute to the efficiency of industrial ceramic production?Wire cutting contributes to production efficiency by reducing material waste, minimizing the need for post-processing, and enabling faster turnaround times. The precision and accuracy of wire cutting also reduce the likelihood of defects, leading to higher quality and more consistent products.