In the fast-paced world of semiconductor manufacturing, the wire saw machine stands as a pivotal tool for cutting silicon ingots. This article delves into how these machines are utilized, focusing on optimizing yield and reducing costs. Whether you’re a seasoned professional or a curious newcomer, you’ll find valuable insights to enhance your operations.

Wire saw machines play a fundamental role in the semiconductor industry, particularly in the slicing of silicon ingots into wafers. These machines use a thin wire, often coated with abrasive materials, to make precise cuts. Companies like Shine have revolutionized this technology, making it more efficient and cost-effective. But what exactly makes these machines so indispensable?
Understanding the key components of a wire saw machine is crucial for optimizing its performance. The main components include:
- Wire: The cutting wire, often diamond-coated, is the heart of the machine.
- Wire Guide Rollers: These ensure the wire remains in the correct position.
- Abrasive Slurry: This aids in the cutting process by reducing friction.
- Control Systems: Advanced control systems, like those in Shine machines, allow for precise adjustments and monitoring.
These components work in tandem to achieve the high precision required in semiconductor manufacturing. The wire, guided by rollers and aided by abrasive slurry, slices through the silicon ingot with minimal waste. Control systems ensure that every cut is as accurate as possible, maximizing the yield of usable wafers.
Maximizing the yield of silicon wafers from each ingot is a top priority. Here are some strategies to achieve this:
- Precision Alignment: Ensure that the wire is precisely aligned with the ingot to minimize waste.
- Optimized Cutting Speed: Adjust the cutting speed to balance efficiency and precision.
- Regular Maintenance: Keep the machine in top condition to avoid errors and downtime.
Shine’s wire saw machines are designed with these strategies in mind, offering advanced alignment systems and customizable cutting speeds. By focusing on these areas, you can significantly increase the number of wafers produced from each ingot, thereby optimizing yield.
Reducing operational costs while maintaining high-quality cuts is a balancing act. Here are some effective techniques:
- Energy Efficiency: Use energy-efficient machines to lower electricity costs.
- Consumable Management: Optimize the use of consumables like abrasive slurry and cutting wire.
- Automation: Implement automation to reduce labor costs and increase precision.
Shine has incorporated these cost-saving measures into their wire saw machines, making them not only efficient but also economical. By focusing on energy efficiency, consumable management, and automation, you can significantly reduce your operational costs.
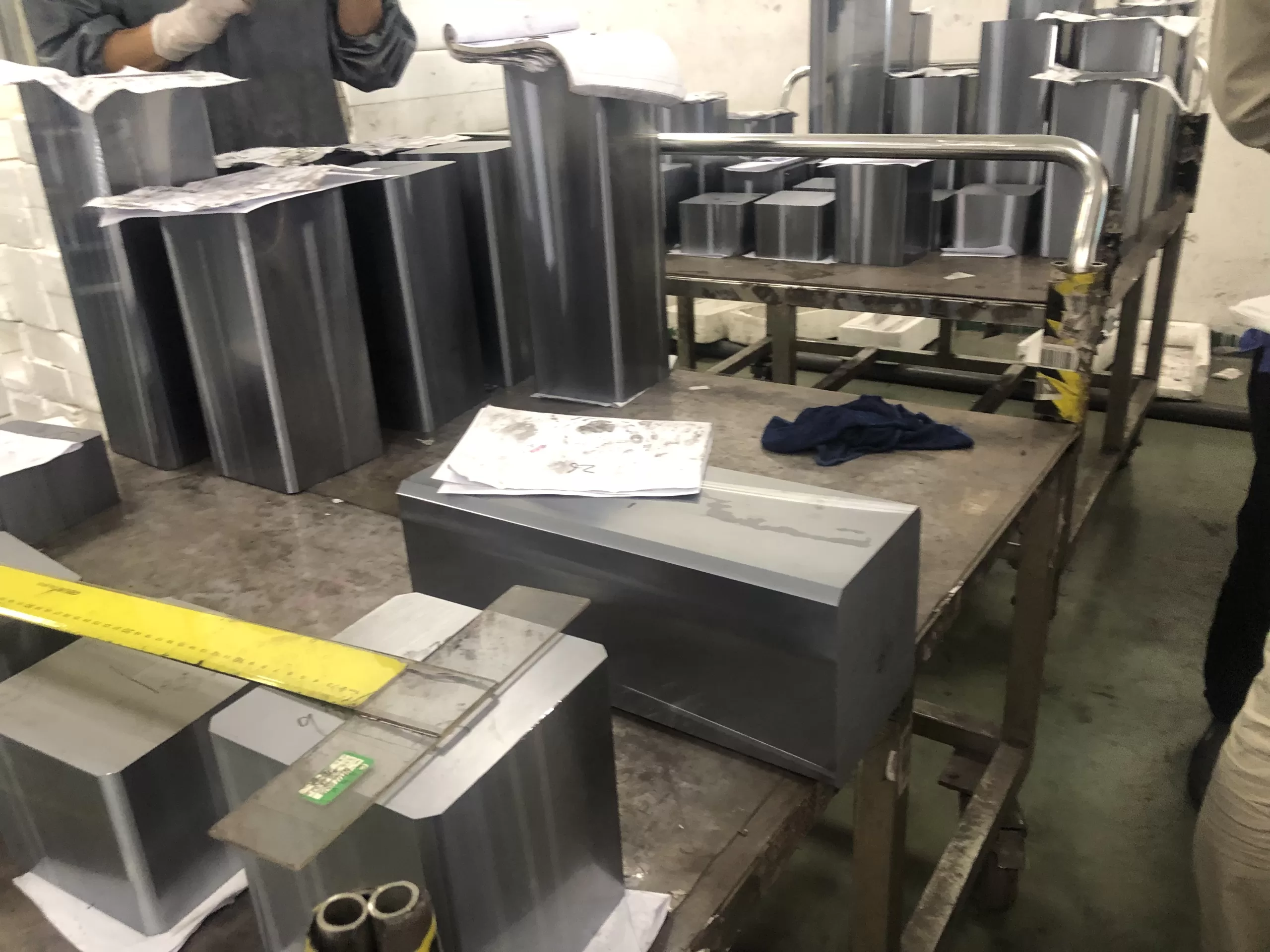
The choice of materials and wires can greatly impact the efficiency and effectiveness of the wire saw machine. Key considerations include:
- Wire Material: Diamond-coated wires are highly effective for cutting silicon.
- Abrasive Slurry: Choose a slurry that complements the wire and the material being cut.
- Ingot Quality: High-quality ingots result in better cuts and less waste.
Shine offers a range of materials and wire options designed to enhance the performance of their machines. By selecting the right combination, you can achieve faster cuts and higher yields.
Regular maintenance is essential for consistent performance. Here are some guidelines:
- Routine Inspections: Regularly inspect the wire, rollers, and control systems.
- Lubrication: Ensure that all moving parts are adequately lubricated.
- Software Updates: Keep the machine’s software updated to benefit from the latest features.
Shine provides comprehensive maintenance guidelines and troubleshooting support to ensure that their wire saw machines operate at peak performance. By following these guidelines, you can minimize downtime and extend the life of your machine.
The world of wire saw machines is constantly evolving. Future trends and innovations include:
- AI and Machine Learning: These technologies can optimize cutting parameters in real-time.
- Advanced Materials: New materials for wires and abrasives can enhance cutting efficiency.
- Eco-Friendly Solutions: Sustainable practices and materials are becoming increasingly important.
Shine is at the forefront of these innovations, continually developing new technologies to improve the efficiency and cost-effectiveness of their wire saw machines. By staying ahead of these trends, you can ensure that your operations remain competitive and sustainable.
Introduction to Wire Saw Machines
Wire saw machines are the unsung heroes of the semiconductor industry, playing a pivotal role in the precise cutting of silicon ingots. These machines, such as those produced by Shine, are designed to slice through silicon with unparalleled accuracy, ensuring that each wafer meets the stringent quality standards required for semiconductor manufacturing.
At their core, wire saw machines operate by using a thin wire coated with abrasive particles to methodically cut through silicon ingots. This process is not only efficient but also minimizes material wastage, which is crucial in an industry where every gram of silicon counts. Shine’s wire saw machines, for instance, are renowned for their precision and reliability, making them a top choice for manufacturers worldwide.
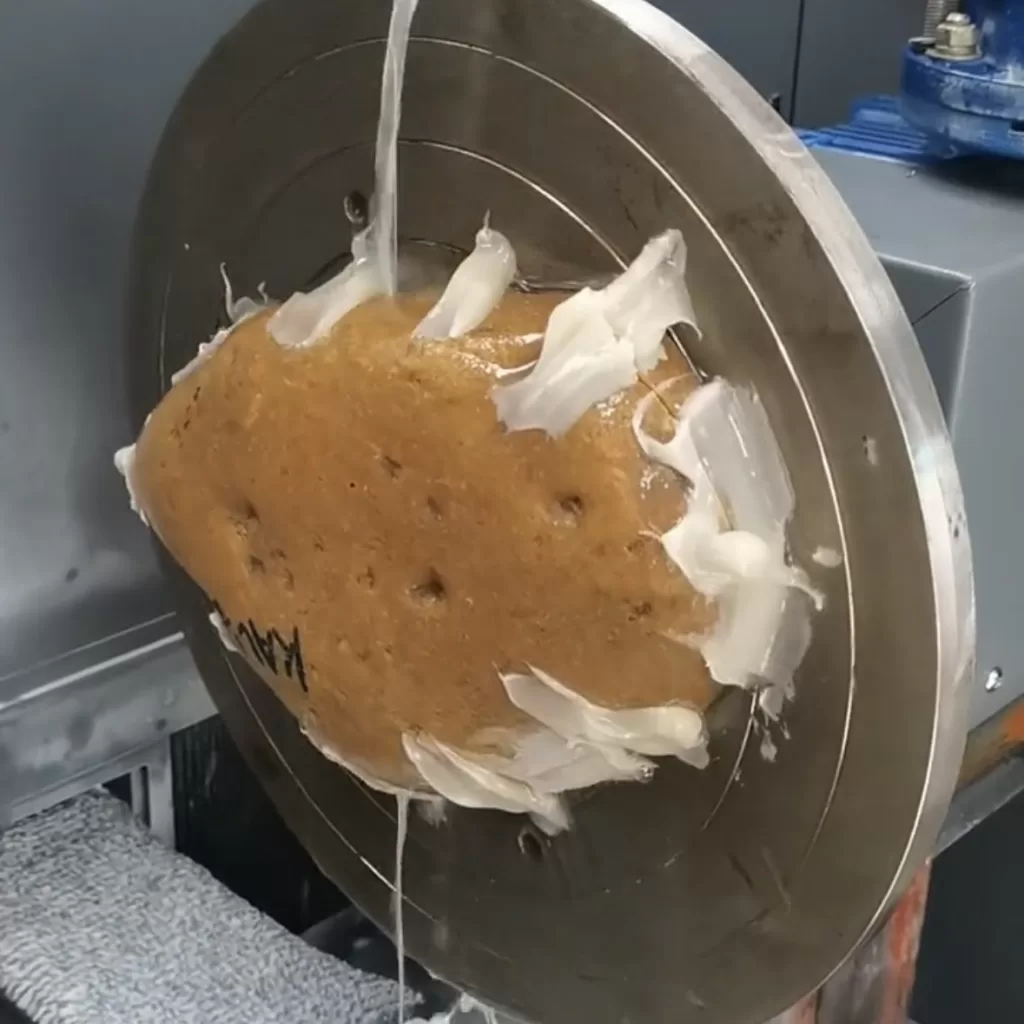
The fundamental role of wire saw machines in the semiconductor industry cannot be overstated. They are responsible for transforming bulky silicon ingots into thin, uniform wafers that serve as the foundation for electronic devices. Without these machines, the production of semiconductors would be significantly more challenging and costly. Shine has been at the forefront of this technology, continually innovating to enhance the performance and efficiency of their wire saw machines.
One of the key advantages of wire saw machines is their ability to produce wafers with minimal kerf loss – the material lost during the cutting process. This is particularly important when dealing with high-purity silicon, where maximizing yield is essential. Shine’s advanced wire saw machines are engineered to achieve this balance, ensuring that manufacturers can produce more wafers from each ingot without compromising on quality.
In summary, wire saw machines are indispensable in the semiconductor industry, providing the precision and efficiency needed to produce high-quality silicon wafers. Companies like Shine are leading the way in this field, offering cutting-edge solutions that help manufacturers optimize their yield and reduce costs. As we delve deeper into the world of wire saw machines, we’ll explore the various components, functionalities, and strategies that make these machines so effective.
Key Components and Functionality
When it comes to wire saw machines, understanding their key components and functionality is crucial. These machines are the backbone of the semiconductor industry, especially for cutting silicon ingots into wafers. Let’s delve into the main components that make up these sophisticated machines and how they work together to achieve precise cuts.
First and foremost, the wire saw machine comprises several critical parts, each playing a unique role in the cutting process. Here’s a breakdown of the main components:
- Wire Web: This is the heart of the machine, consisting of a thin wire that moves continuously to slice through the silicon ingot. The wire web’s tension and speed are meticulously controlled to ensure precision.
- Guiding Rollers: These rollers guide the wire web, keeping it aligned and taut. Proper alignment is essential for achieving uniform cuts and preventing wire breakage.
- Slurry Delivery System: The slurry, a mixture of abrasive particles and coolant, is delivered to the cutting zone. This system ensures that the wire remains cool and the cutting process is efficient.
- Ingot Holder: The ingot holder secures the silicon ingot in place, preventing any movement during the cutting process. Stability is key to achieving high-quality wafers.
- Control Unit: The control unit is the brain of the wire saw machine. It regulates the wire speed, tension, and slurry flow, ensuring optimal performance and precision.
So, how do these components work together? The process begins with securely placing the silicon ingot in the ingot holder. Once in place, the wire web, guided by the rollers, starts moving at a controlled speed. The slurry delivery system ensures that the wire is adequately lubricated and cooled, reducing friction and wear.
The control unit continuously monitors and adjusts the wire’s tension and speed, ensuring a smooth and precise cut. This orchestration of components results in high-quality silicon wafers, ready for further processing in the semiconductor industry. The brand Shine has perfected this process, ensuring their wire saw machines deliver unparalleled precision and efficiency.
In summary, the key components of a wire saw machine – the wire web, guiding rollers, slurry delivery system, ingot holder, and control unit – work in harmony to achieve precise cuts. Understanding these components and their functionality is essential for anyone looking to optimize their wafer production process. With Shine’s advanced technology, you can be confident in achieving the highest yield and quality in your silicon wafer production.
Optimizing Yield
When it comes to maximizing the yield of silicon wafers from each ingot, wire saw machines play a pivotal role. The right techniques and strategies can significantly enhance the output, ensuring that every slice counts. Here’s how you can optimize yield using wire saw machines, with a special focus on Shine’s innovative solutions.
First and foremost, precision is key. The accuracy of the wire alignment and the consistency of the cutting process are crucial. Shine wire saw machines are renowned for their exceptional precision, thanks to advanced control systems that ensure each cut is made with minimal deviation. This precision reduces waste and maximizes the number of usable wafers from each ingot.
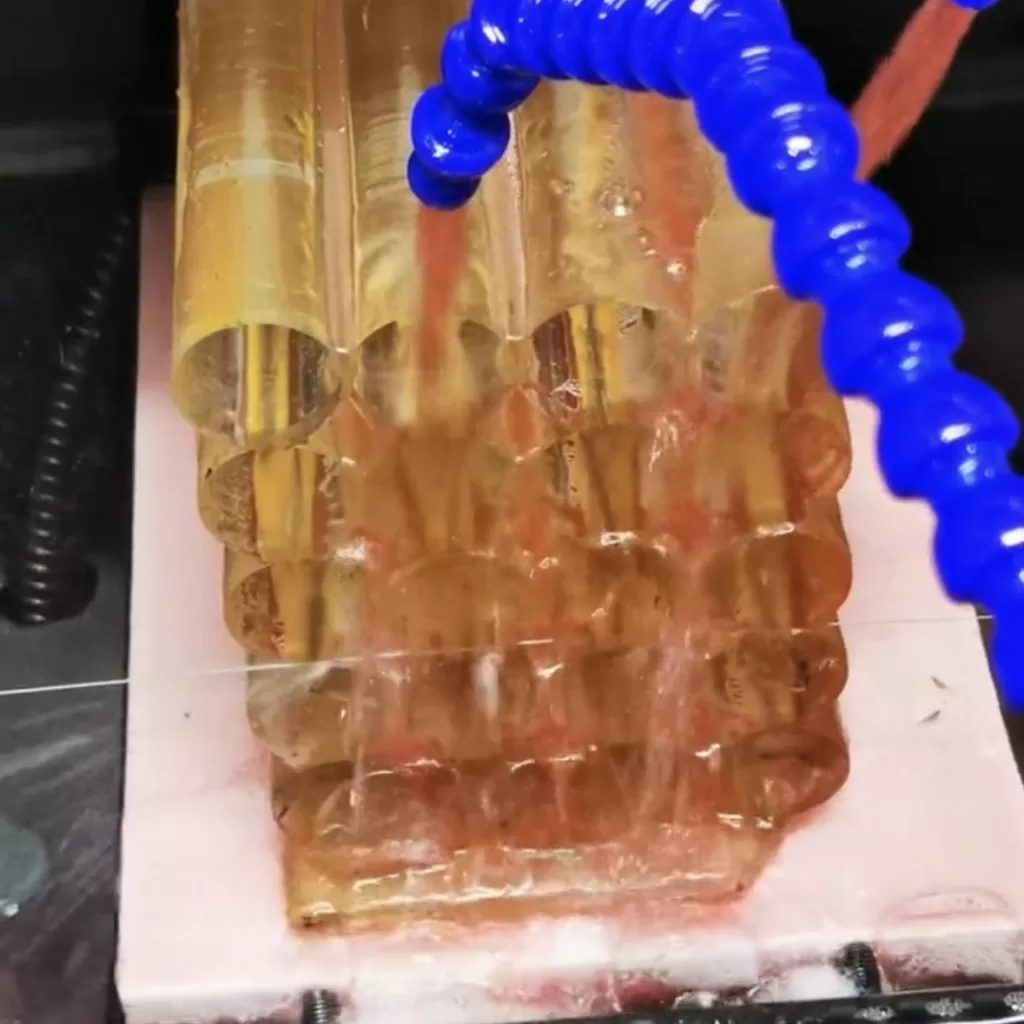
Another essential aspect is the speed of the cutting process. Faster cutting speeds can lead to higher throughput, but it’s important to strike a balance between speed and quality. Shine machines offer adjustable cutting speeds, allowing operators to find the optimal setting that maximizes yield without compromising the integrity of the wafers.
Moreover, the thickness of the wire used in the sawing process can have a significant impact on yield. Thinner wires result in less material loss, known as kerf loss, during cutting. Shine provides a range of wire options, including ultra-thin wires that minimize kerf loss and enhance yield. However, it’s important to choose a wire that maintains strength and durability to prevent breakage.
Proper ingot preparation is also critical. Ensuring that the ingot is free from impurities and defects before cutting can prevent issues that lead to wafer breakage or unusable slices. Shine offers comprehensive ingot inspection and preparation solutions that help in identifying and addressing potential problems before they affect the yield.
Additionally, employing advanced monitoring and feedback systems can greatly enhance yield optimization. Shine’s wire saw machines are equipped with real-time monitoring capabilities, providing operators with instant feedback on the cutting process. This allows for immediate adjustments to be made, ensuring that each cut is optimized for maximum wafer production.
Lastly, continuous training and skill development for operators cannot be overlooked. Skilled operators who are well-versed in the nuances of the wire sawing process can make a significant difference in yield outcomes. Shine offers extensive training programs to ensure that operators are equipped with the knowledge and skills needed to maximize yield effectively.
In summary, optimizing yield in the wire sawing process involves a combination of precision, speed, wire selection, ingot preparation, advanced monitoring, and skilled operation. By leveraging Shine’s state-of-the-art wire saw machines and comprehensive support solutions, manufacturers can achieve higher yields and greater efficiency in their silicon wafer production.
Cost Reduction Techniques
When it comes to cutting silicon ingots, reducing costs without compromising on quality is a crucial goal. Utilizing wire saw machines effectively can significantly contribute to this objective. Here are some key techniques to achieve cost reduction:
1. Optimize Wire Usage: The wire is a critical component in the cutting process and can be a significant cost factor. By optimizing wire tension and speed, you can minimize wire breakage and extend its lifespan. The brand Shine offers high-quality wires that are designed to withstand the rigorous demands of silicon cutting, ensuring longer usage and fewer replacements.
2. Efficient Slurry Management: Slurry, a mixture of abrasive particles and coolant, plays a vital role in the cutting process. Efficient management of slurry can lead to substantial cost savings. Implementing a recycling system for slurry can reduce the need for fresh slurry, cutting down on material costs. Shine provides advanced slurry management solutions that are both cost-effective and environmentally friendly.
3. Energy Consumption: Energy costs can be a significant part of the operational expenses in wire saw machines. Utilizing energy-efficient machines and optimizing operational parameters can lead to considerable savings. Shine wire saw machines are designed with energy efficiency in mind, helping you cut down on electricity bills while maintaining high performance.
4. Regular Maintenance: Preventive maintenance is key to avoiding costly breakdowns and repairs. Regularly inspecting and maintaining your wire saw machine ensures it operates at peak efficiency. Shine offers comprehensive maintenance packages that help keep your machines in top condition, reducing downtime and repair costs.
5. Training and Skill Development: Investing in training for your operators can lead to better handling of the machines and fewer operational errors. Skilled operators can optimize the cutting process, reducing waste and improving yield. Shine provides training programs that equip your team with the necessary skills to operate wire saw machines efficiently.
In summary, reducing costs in the wire sawing process involves a combination of optimizing wire usage, managing slurry efficiently, reducing energy consumption, maintaining the machines regularly, and investing in operator training. By adopting these techniques and leveraging the solutions offered by Shine, you can achieve significant cost savings while maintaining high-quality cuts.
Material and Wire Selection
When it comes to wire saw machines, the choice of materials and wires can make or break the efficiency of your operations. The right selection is crucial for optimizing both yield and cost. So, how do you go about making these choices? Let’s dive into the details.
First off, the material of the wire itself is paramount. Different wires are suited for different tasks, and understanding the nuances can help you make an informed decision. For instance, diamond-coated wires are often preferred for their durability and precision. They can cut through silicon ingots like a hot knife through butter, making them a popular choice in the semiconductor industry.
But wait, there’s more! The core material of the wire also plays a significant role. Steel cores are common, but other options like tungsten and molybdenum are gaining traction. These materials offer higher tensile strength and longer life, which can be particularly beneficial for high-volume operations.
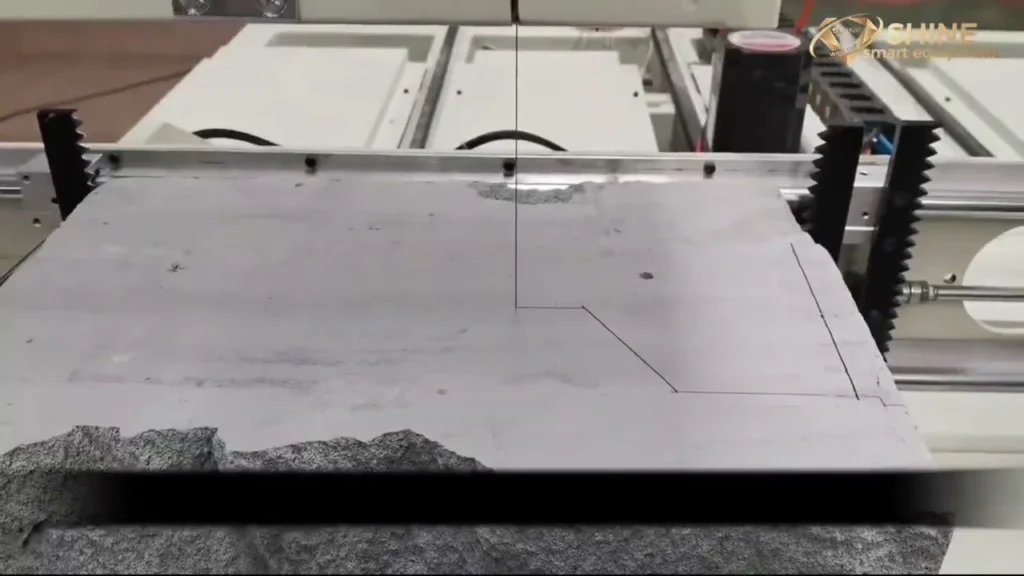
Now, let’s talk about the brand. Shine is a name that frequently comes up in discussions about high-quality wire saw machines and materials. Shine offers a range of wires that are specifically designed to maximize efficiency and minimize waste. Their products are known for their exceptional durability and cutting precision, making them a go-to choice for many in the industry.
Another critical factor is the grit size of the wire. Smaller grit sizes result in finer cuts but may take longer, while larger grit sizes can speed up the process but may compromise on precision. Shine offers a variety of grit sizes to suit different needs, ensuring that you can find the perfect balance between speed and accuracy.
Let’s not forget about the importance of the slurry used in the cutting process. The right slurry can significantly enhance the performance of your wire saw machine. Shine’s specialized slurries are designed to work seamlessly with their wires, providing optimal lubrication and cooling during the cutting process. This not only improves the quality of the cut but also extends the life of the wire.
To sum it up, selecting the right materials and wires is a multifaceted process that requires careful consideration. Brands like Shine offer a range of options that can help you optimize your operations. By choosing the right wire material, core, grit size, and slurry, you can achieve precise cuts, maximize yield, and reduce costs. So, next time you’re in the market for wire saw materials, remember to consider Shine for your needs.
In conclusion, the right material and wire selection can significantly impact the efficiency and cost-effectiveness of your wire saw machine. With brands like Shine offering top-notch products, you can ensure that your operations run smoothly and efficiently. Happy cutting!
Maintenance and Troubleshooting
Maintaining your wire saw machine is crucial for ensuring its longevity and consistent performance. Regular maintenance not only optimizes the cutting efficiency but also minimizes downtime and unexpected costs. The brand “Shine” offers several maintenance tips and troubleshooting guidelines to keep your wire saw machine in top condition.
First and foremost, it’s essential to conduct routine inspections of the machine. These inspections should include checking the tension of the wire, the alignment of the cutting components, and the condition of the cutting fluid. A well-maintained wire saw machine from Shine can significantly reduce the chances of operational hiccups.
Here’s a detailed list of maintenance tasks to keep your Shine wire saw machine running smoothly:
- **Daily Checks**: Ensure the wire tension is within the recommended range. Check for any visible wear and tear on the wire and replace it if necessary.
- **Weekly Checks**: Inspect the cutting fluid levels and top up if required. Also, check the alignment of the wire guides and adjust them to prevent uneven cuts.
- **Monthly Checks**: Conduct a thorough cleaning of the machine to remove any debris or silicon dust that may have accumulated. Lubricate all moving parts to ensure smooth operation.
- **Quarterly Checks**: Perform a comprehensive inspection of the machine’s electrical components. Ensure that all connections are secure and free from corrosion.
Troubleshooting common issues is equally important to maintain the efficiency of your Shine wire saw machine. Here are some common problems and their solutions:
- Wire Breakage: If the wire keeps breaking, it could be due to excessive tension or misalignment of the wire guides. Adjust the tension and realign the guides as needed.
- Uneven Cuts: Uneven cuts are often a result of worn-out wire or improper alignment. Replace the wire and check the alignment of the cutting components.
- Machine Vibration: Excessive vibration can be caused by imbalanced wire tension or worn-out bearings. Ensure the wire tension is balanced and replace any worn-out bearings.
- Overheating: Overheating may occur due to insufficient cooling or clogged filters. Ensure that the cooling system is functioning correctly and clean or replace the filters regularly.
By following these maintenance and troubleshooting guidelines, you can ensure that your Shine wire saw machine operates at peak performance. Regular upkeep not only enhances the machine’s efficiency but also extends its lifespan, ultimately leading to cost savings and higher productivity.
In conclusion, maintaining a Shine wire saw machine involves regular inspections, timely replacements, and addressing issues promptly. By adhering to these practices, you can optimize the yield and reduce operational costs, ensuring that your wire saw machine continues to deliver precise and efficient cuts.
Future Trends and Innovations
When it comes to the future of wire saw machines for silicon ingots, the landscape is brimming with exciting possibilities. The industry is constantly evolving, and staying ahead of the curve is crucial for maintaining a competitive edge. So, what can we expect in the coming years? Let’s dive into some of the most promising trends and innovations that are set to revolutionize the field.
First and foremost, the integration of artificial intelligence (AI) and machine learning (ML) is poised to transform wire saw machines. Imagine a machine that learns from each cut, optimizing its performance over time to deliver unparalleled precision and efficiency. This is not just a pipe dream; companies like Shine are already investing heavily in AI and ML technologies to make this a reality. With AI-driven algorithms, wire saw machines can predict wear and tear on wires, adjust cutting speeds in real-time, and even foresee potential issues before they arise.
Another exciting development is the advent of smart sensors and IoT (Internet of Things) integration. These technologies allow for real-time monitoring and data collection, providing valuable insights into the cutting process. For instance, Shine has been at the forefront of incorporating IoT solutions into their wire saw machines, enabling users to track performance metrics, receive maintenance alerts, and optimize operations remotely. This not only enhances efficiency but also significantly reduces downtime and operational costs.
Material science is also making significant strides, with new materials being developed to enhance the durability and performance of cutting wires. Companies like Shine are experimenting with advanced composites and coatings that can withstand higher stress and temperatures, leading to longer-lasting wires and more precise cuts. This is particularly important for reducing material wastage and improving the overall yield of silicon wafers.
Moreover, the push towards sustainability is driving innovations in wire saw machine technology. Eco-friendly lubricants and coolants are being developed to minimize environmental impact, while energy-efficient designs are becoming a standard. Shine, for example, is committed to sustainability and has introduced several eco-friendly solutions in their latest wire saw machine models. These innovations not only help reduce the carbon footprint but also contribute to cost savings in the long run.
Let’s not forget the role of automation in shaping the future of wire saw machines. Fully automated systems are becoming increasingly prevalent, allowing for seamless integration with other manufacturing processes. Shine is leading the charge with their state-of-the-art automated wire saw machines that offer unparalleled precision and consistency. These machines can operate 24/7 with minimal human intervention, drastically improving productivity and reducing labor costs.
Lastly, the future holds promise for customization and flexibility in wire saw machine design. As the semiconductor industry diversifies, the need for machines that can handle a variety of materials and cutting requirements is growing. Shine is pioneering modular designs that allow users to customize their wire saw machines to meet specific needs, whether it’s cutting ultra-thin wafers or handling larger ingots. This flexibility ensures that manufacturers can adapt to changing market demands without significant investments in new equipment.
In conclusion, the future of wire saw machines for silicon ingots is incredibly bright, thanks to advancements in AI, IoT, material science, sustainability, automation, and customization. Companies like Shine are at the forefront of these innovations, continually pushing the boundaries to optimize yield and reduce costs. As these technologies evolve, we can expect wire saw machines to become even more efficient, reliable, and versatile, paving the way for a new era in semiconductor manufacturing.
Frequently Asked Questions
- What is a wire saw machine and why is it important for cutting silicon ingots?A wire saw machine is a specialized device used in the semiconductor industry to cut silicon ingots into thin wafers. These machines are crucial because they ensure precise cuts, which are essential for maximizing yield and reducing material waste.
- How do wire saw machines optimize yield?Wire saw machines optimize yield by using advanced cutting techniques and precise control mechanisms. They minimize kerf loss (material lost during cutting) and ensure uniform thickness across all wafers, thereby maximizing the number of usable wafers from each ingot.
- What are the key components of a wire saw machine?The key components include the wire, slurry or cutting fluid, tensioning system, and the control unit. Each part plays a vital role in ensuring accurate and efficient cutting of silicon ingots.
- How can operational costs be reduced while using wire saw machines?Operational costs can be reduced by optimizing the cutting process, using high-quality wires, and maintaining the machine regularly. Additionally, recycling the cutting slurry and using energy-efficient systems can contribute to cost savings.
- Why is material and wire selection important?Selecting the right materials and wires is crucial because they directly impact the cutting efficiency and quality. High-quality wires ensure precise cuts and longer machine life, while the right materials minimize wear and tear.
- What maintenance practices are recommended for wire saw machines?Regular maintenance practices include cleaning the machine, checking and replacing worn-out parts, and ensuring the tensioning system is properly calibrated. Periodic inspections and timely troubleshooting of issues can prevent costly downtimes.
- What are some common troubleshooting tips for wire saw machines?Common troubleshooting tips include checking for wire breakage, ensuring the slurry is not contaminated, and verifying the tensioning system is functioning correctly. Regular software updates and calibrations can also help in maintaining optimal performance.
- What future trends and innovations can we expect in wire saw machines?Future trends include advancements in automation, the use of AI for predictive maintenance, and the development of more durable and efficient cutting wires. These innovations aim to further optimize yield and reduce operational costs.